基于模态轮胎模型的路面振动噪声仿真分析
由路面不平度引起的车内振动噪声响应,是整车NVH仿真领域中需要关注与把控的关键性能之一。在设计前期通过CAE技术对其性能进行前期把控,是解决路面振动噪声问题、提升产品品质的最有效途径。由于整车NVH仿真方面存在诸多技术瓶颈,使国内在路面振动噪声仿真领域进展缓慢。其中,模态轮胎建模技术的不成熟,严重滞缓了国内整车企业在该工程领域的能力发展。由于轮胎本身存在非线性等特性,并在整车状态下需要考虑充气、接地等多方面因素,因此其详细模型的建立,以及与NVH整车模型的匹配便成为国内仿真工程师面临的主要难题。
针对上述背景,本文对详细模态轮胎建模、轮胎缩减等关键技术进行了研究,并基于模态轮胎模型开展了路面振动噪声仿真分析,为整车路面振动噪声性能设计提供了有效的工程仿真方法。
2、详细模态轮胎模型建立
汽车在行驶过程中,路面不平度产生的激励通过轮胎传递到车身中,并在乘员舱内形成振动噪声响应。由于轮胎自身的特性,部分激励经过轮胎将被放大,而部分将被过滤,因此在整车仿真模型中,需要考虑轮胎的振动特性,从而真实的再现路面激励下的车内振动、噪声问题。
模态轮胎模型的建立通常需要经过三个过程:轮胎特征参数及橡胶热机械特性测试、轮胎详细模型建立、模态轮胎缩减。其中,详细轮胎模型的建立过程相对复杂,其建模过程中集成了整车厂(轮胎公司)诸多工程经验参数,其方法与流程也是企业的核心技术所在。
本文工作中,该过程的建立均在Abaqus软件中完成。模型建立前,需通过测试的手段对其将要建模的实物轮胎进行相关材料性能测试,其中包括轮胎的结构组成(如图1所示)以及一些几何、材料特征参数等。获取所需的结构组成及参数后,在Abaqus软件中建立轮胎平面模型。
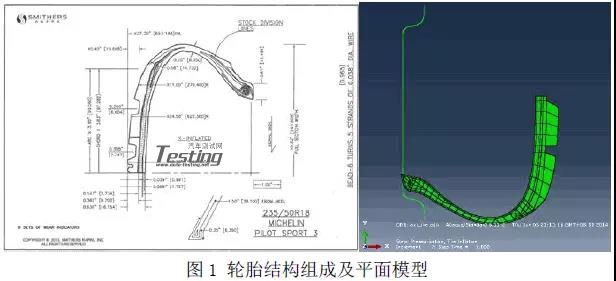
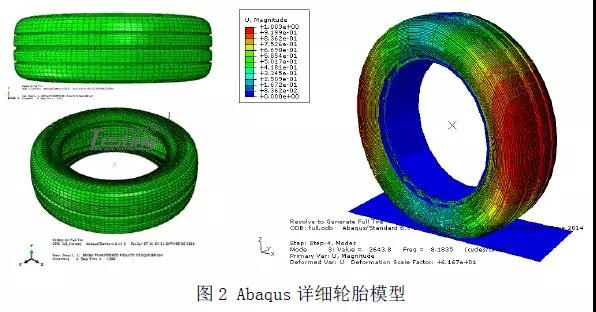
基于建立后的平面模型,可在软件中生成轮胎整体模型,其过程中考虑充气、接地以及与轮毂装配等过程,这些也是影响轮胎振动特性的关键因素。由于需要考虑路面振动噪声工程化仿真的操作性,又需满足精度的要求,因此在本文工作中,轮胎转速等因素未在模型中体现。建立后的模型可在Abaqus求解器中得到其模态结果,其典型模态振型如下图所示。
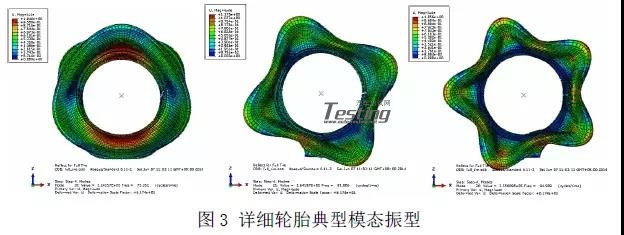
3、轮胎缩减理论
由于轮胎有限元模型单元数量、自身非线性的特性,以及需要考虑充气、轴荷和接地等因素,直接将有限元模型用于整车NVH仿真分析不易实现。因此,国外先进企业通常将缩减后的模态轮胎模型集成在整车有限元模型中,从而实现路面激励工况下的整车振动噪声性能的计算。鉴于模态轮胎缩减技术的关键性,这里对其进行简述。
根据动力学方程,对于单一轮胎存在:
.jpg)
其中和分别.轮胎K和M分别为轮胎刚度矩阵和质量矩阵,下脚标b为边界结构,即轮胎接地点,a为非边界约束结构,包括与轴心连接点和其它轮胎本体特征点。通过特征向量矩阵,可将物理空间自



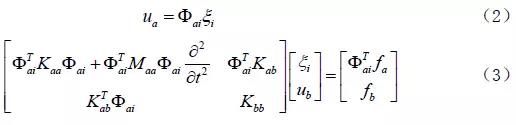
定义模态刚度矩阵和模态质量矩阵分别为kii,mii,则在上式(3)中,两者分别为:

同时定义:

则公式(3)可以转化为:

其中:
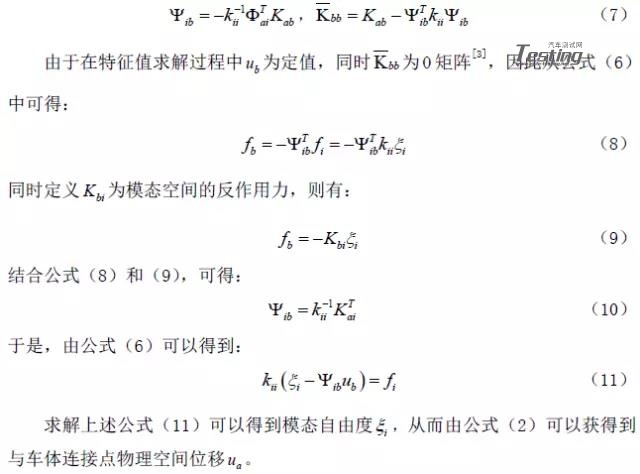
基于上述理论,基于上述理论,可以建立NASTRAN格式的轮胎NVH仿真模型。其模态轮胎模型包含四个部分:第一部分为轮胎接地点,即ub,每个轮胎接地点均有6 个自由度,在整车仿真中轮胎接地点为全约束状态;第二部分为模态刚度、模态质量和

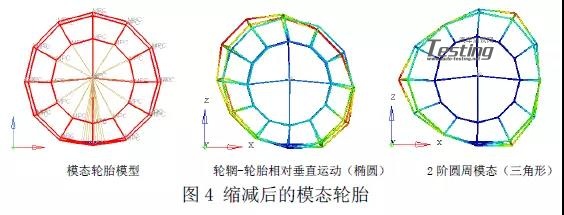
4、整车路面振动噪声仿真分析
低频路面振动噪声仿真(结构噪声,小于200Hz),是基于有限元方法,计算车辆在不同随机路面和车速下的振动、噪声性能。在完成轮胎建模工作后,建立整车有限元模型(如下图5所示),模型中的轮胎与轴头相连接。在进行路噪仿真之前,需通过典型模态验证该底盘模型连接关系的正确性,如:根据前后悬同步、异步跳动模态等。
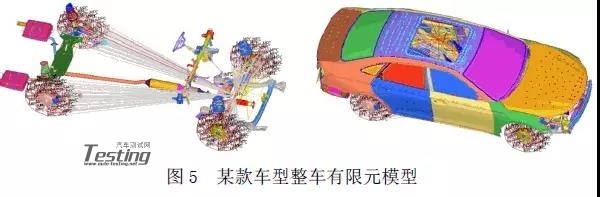
整车路面振动噪声仿真流程分成两个步骤:第一步是计算整车从输入点到响应点的传递函数,即轮胎接地面到响应点,如方向盘、座椅导轨、耳朵位置等;第二步是传递函数模的平方乘以路面的PSD谱,输出响应点的响应PSD谱。同时综合考虑振动及噪声两种性能,输出点分别为方向盘12点处、驾驶员座椅导轨右后安装点振动加速度(单位g),以及驾驶员右边人耳处和后排乘员人耳处声压(单位dBA)。计算所得到的振动、噪声响应曲线如下图6所示。
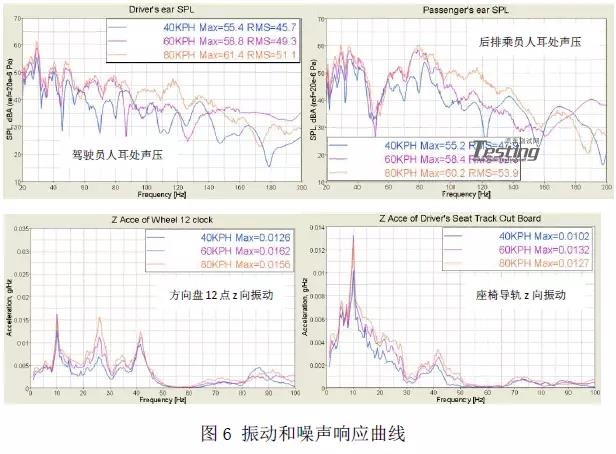
从结果中可知,该车型在三种车速下后排人耳处声压值均较高(RMS分别为47.9dBA、52.3dBA和53.9dBA)。同时,与参考车AtoB对标结果显示,相同位置与相同工况下,该结果均高出目标值,这与主/客观评价结果相符合;另外,前排驾驶员人耳处声压结果与参考车目标值相近,与主观和客观评价结果也一致。上述对标结果证明了该仿真过程的有效性。
5、结论
通过文中方法建立模态轮胎模型,并基于该轮胎模型实现整车路面振动噪声仿真,可以有效地计算出路面激励工况下的车内响应。由于实车路噪试验过程中,发动机激励还没有理想的方法进行屏蔽,因此目前缺少工况一致的数据对比,这也是在今后的研发过程中需要进一步完善的工作。
最新资讯
-
全国汽车标准化技术委员会汽车节能分技术委
2025-04-18 17:34
-
我国联合牵头由DC/DC变换器供电的低压电气
2025-04-18 17:33
-
中国汽研牵头的首个ITU-T国际标准正式立项
2025-04-18 17:32
-
为什么要进行汽车以太网接收测试?汽车以太
2025-04-18 17:26
-
产品手册下载 | NI 全新USB数据采集-NI mio
2025-04-18 16:39