动力电池系统DV测试浅析
叶磊Ray:IND4汽车人资深注册用户,目前在上海一家大型国企负责BMS开发。
本文介绍了DV测试的概要和内容,其中,来自三星的Pack测试工程师陈勃分享了一些他的测试经验。
DV(Design Verification) 设计验证,目的是验证产品设计是否符合规定要求而进行的测试活动。另一个经常提到的概念,PV(Production Validation)生产确认,目的是确认制造状态是否符合规定要求。DV和PV通常是一组平行的测试计划,且DV测试内容包括了大部分的PV测试。总得来讲,一份好的DV或PV测试活动,需要以法规要求为基准、以功能需求为驱动、以真实使用场景为背景并配合适当的测试技巧来进行。本文主要围绕DV进行简要阐述。
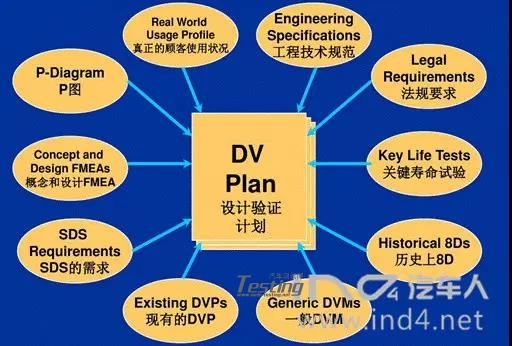
一.动力电池系统DV测试概述
1.1 对于开发流程与样品状态的对应关系
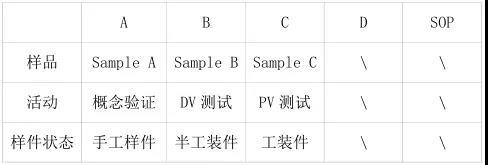
注1:手工样件与工装件的主要区别在于结构件是否通过工装模具加工得到(开模件);半工装件与工装件在于动力电池系统是否由正式的生产线组装。
注2:因为国内各公司对零部件的开发流程定义不同,这里提供的仅是笔者遇到的某个案例。
1.2 对于测试活动与对应的开发流程对应
A sample:对于零部件供应商来说,需要进行功能测试,比如BMS的采样精度,控制策略,SOC算法等等的验证。也有供应商会利用A样的产品进行DV的摸底试验。另外,整车厂还会使用交付的A样件动力电池系统进行基本的实车装配以及通讯联调,简单启动等测试。
B sample:对于零部件供应商来说,需要进行DV测试、设计整改等等。另外,整车厂还会使用交付的B样件动力电池系统进行实车标定、匹配、路测等。
C sample:在经过B阶段的设计整改后,电池包的基本结构、工装夹具均已定型。此时,随着生产线的建立,C样件动力电池系统出现并适用于PV测试。
1.3 责成划分
A sample:一般由公司(SW)TE主导进行,工作内容偏研发方向,如精度验证、控制策略及算法调试等,需要熟悉动力电池系统及软硬件设计的人员充分介入。
B sample:主要由公司TE主导进行,工作内容大多为型式试验。技能需求上不仅需要对BMS软硬件设计上有一定的理解,还得扩展到其它如电芯特性、材料力学等。
C sample: 一般则由公司的QE主导进行,测试项目一般是DV内容的子集。
1.4 测试依据
动力电池系统DV的测试依据主要有以下几个方面:
1、与OEM之间的技术协议书
2、OEM的企标
3、相关国家/国际标准
4、过往测试经验
1.5 流程计划
从流程上看,DV主要有以下几个节点:
(1)与客户签订项目的商务合同
(2)编写DV测试大纲及测试计划
(3)与客户Review测试大纲和计划
(4)考察供应商,并和供应商进行技术交流(第三方测试机构)
(5)三方比较,确认供应商
(6)和供应商签订商务合同
(7)测试物料,样品的准备,夹具的制作
(8)测试活动的进行
(9)测试活动的结束及善后
(10)测试报告的提交及review
(11)测试总结
注:有公司会提前进行供应商的考察活动并与供应商签订框架协作合同,故第4、5、6步不固定。
二.动力电池系统DV测试内容
动力电池系统DV测试主要包括以下几方面:
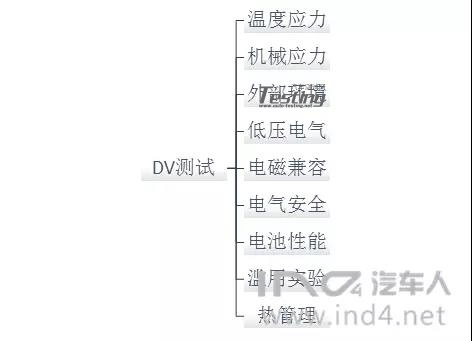
2.1 温度应力试验包括:高/低温操作、温度冲击、结露试验、湿热循环。
2.2 机械应力试验包括:耐振动、机械冲击、负重。
2.3外部环境试验包括:IP防护、盐雾试验、化学液体暴露、碎石轰击、模拟高海拔。
2.4 低压电气试验包括:直流供电电压、过电压、叠加交流电压、电压缓升缓降、供电电压间断、反压、参考接地和供电补偿、开路测试、短路保护、绝缘电阻、耐电压。
2.5 电磁兼容试验包括:瞬间传导发射、电磁传导发射(voltage/current)、电磁辐射发射、瞬态传导抗扰、瞬态耦合抗扰、电磁辐射抗扰度(BCI/ALSE)、静电放电(ON/OFF)、电快速瞬变脉冲群抗扰、浪涌抗扰、低频电磁电子场强等。
2.6 电气安全试验包括:绝缘电阻、耐电压、IPXXB/D电位均衡。
2.7 电池性能试验包括:容量和能量、能量效率、直流内阻、功率确认、自放电、混合动力特性脉冲、高低温启动特性、循环寿命等。
2.8 滥用试验包括:跌落、模拟碰撞、盐水浸泡、挤压、球形挤压、针刺、翻转、热失控、外部火烧、PACK短路、过充/过放电(带或不带保护功能)等。
2.9 热管理试验包括:高温冷却性能、低温加热性能、隔热性能、管壁压降(水冷)、气密性(水冷)、噪音(风冷)等等。
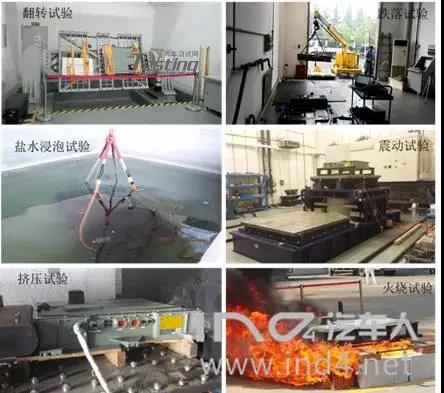
三.测试经验总结
1.50%的时间用来试验准备,30%的时间用来写报告,20%的时间用来做实验。
2.选择测试供应商时,除了资质、报价,设备资源(排期)、测试人员素质、配合程度、地理位置等均应列入考虑范畴。
3.商务合同上,闭口合同可以享受更大的折扣但是所有测试项目必须进行,开口合同优惠较少但比较灵活。对于DV这种不确定因素比较大的试验(可能的调试、排故、整改),闭口可能更为适合。当然有能力也可以谈成按开口合同方式执行的闭口合同,折扣、机动性两不误。
4.关于DV测试大纲、计划的编写
-测试大纲需要客户认可
-测试大纲应尽可能详细、严谨且切合实际,制定完成后需再次梳理预演一遍(经验很重要)。否则很可能使自己和现场的操作人员在具体的执行过程中陷入窘境。
(举个例子,低压电气试验,考察对BMS供电电压的那个,有很多项目,过压,欠压,反压之类,因为繁琐很多人制定的时候简单写到参考ISO16750/GBT28046或者干脆直接复制粘贴标准内容,真正执行的时候,傻眼了,为什么,比如短路试验描述,“对于信号电路的短路试验,将DUT所有有效输入端和输出端,依次连接到Usmax”,那么问题来了,所有有效的输入端和输出端在哪?不清楚,试验暂停,回去查Pin脚定义,改大纲,通知客户...)
-制定测试计划前需要充分了解测试机构的设备排期,切勿仅凭单方面的意志制定不可执行的方案。
-测试序列安排应合理,需要考虑到前序试验项目对样品损伤,影响后续试验项目。
5.横向的对比试验是一种高效的trouble-shooting手段。
6.物料准备方面尽可能有充分的备件准备,一旦发生特殊情况,可有效节约测试时间和成本。
7.有些试验项目电池包需要特殊处理,比如温度试验,需要放开保护条件;比如IP防尘防水,需要布置遇水变色纸;比如振动,需要划线确认扭力甚至感压纸;比如热失控,缠绕加热膜(或引出充电线)...这里需要特别注意的是软件上放开了保护条件的包,一定要注意记录和跟踪,从风险控制上来说,这些电池系统比常规状态少了一层安全保护机制,更容易触发安全事故。
8.测试现场经常会遇到充放电机对绝缘采样(特别是国标法)的干扰,或者因为共地问题,或者因为Y电容的影响。如果实车上未发生过此异常情况,且对于本实验绝缘采样结果对评价上并无客观影响,在得到客户认可的情况下,可以考虑对绝缘采样功能屏蔽处理的方案。
9.挤压测试时若BDU部件受到挤压将显著提升失效概率。
10.关于振动
-试验前一定要确认振动台的尺寸、承重以及频响范围,是否能满足试验要求
-夹具试装叫上供应商可以省很多不必要的麻烦
-夹具的安装孔进行热处理可以有效防止孔位变形
11.关于模拟碰撞
-电池包整车安装点的螺栓与夹具安装孔之间应严格匹配,不能有过大间隙,否则会产生滑动并有螺栓断裂的风险。
12.热失控
-加热、过充、针刺均能实现热失控。但实际操作上,加热用缠绕膜适用在电芯上后重新组装比较困难;针刺对设备有所要求(角度、速率等),个人比较倾向于过充的方法。
还有其他的一些测试经验,下次有机会再分享。
四、总结
动力电池系统的DV测试还是一份比较有挑战性的工作,需要在对系统整体把控的情况下结合自家的产品特点熟练的将相关标准适用其中。个人认为,一个好的测试工程师,现场指导测试方法、安排设备、排故、替公司拿到最终的报告等等这些事固然重要,试验前对测试活动尽可能详细的规划与潜在的失效分析这才是整个测试活动中的重中之重。所以,人们常说,作为测试工程师,经验很重要,因为经验能减少你对时间、经济、安全上损失,走更少的弯路。
编辑推荐
最新资讯
-
飞书项目落地ASPICE解决方案,助力汽车软件
2025-04-24 09:59
-
驾驶员监控系统DMS合规认证的“中西结合”
2025-04-24 08:23
-
自动驾驶汽车测试关键行人场景生成
2025-04-23 17:12
-
R171.01对DCAS的要求⑧
2025-04-23 17:08
-
迄今为止最先进的版本:imc发布全新imc STU
2025-04-23 17:06