电动车变速箱的研发过程
本文主要介绍了这款产品的基础参数,驻车功能集成,振动噪声优化,润滑冷却等方面信息。
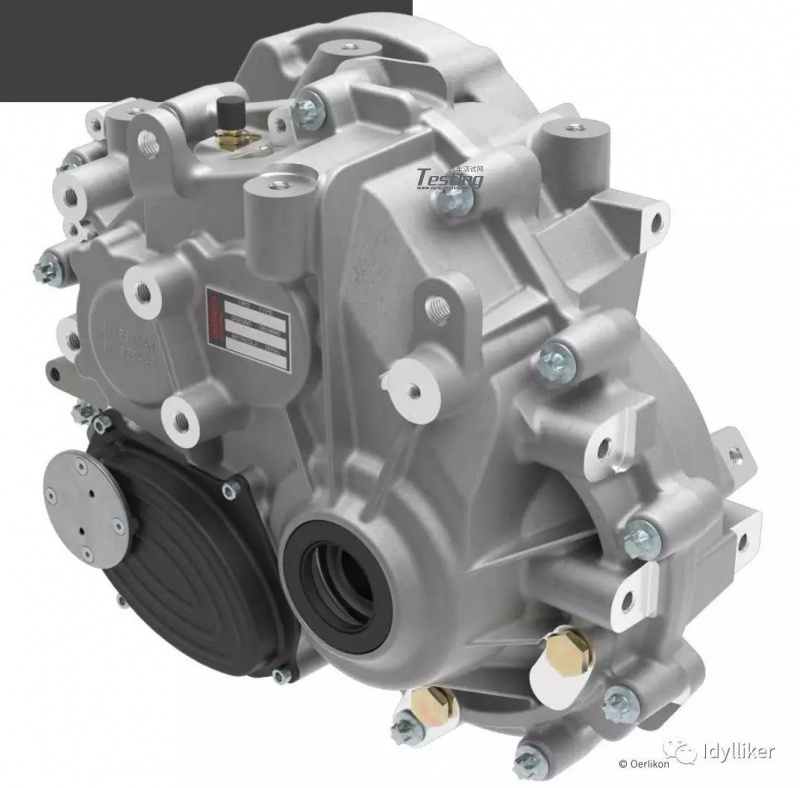
前言:电动动力传动系统在技术规格,尤其是成本方面的要求越来越高。高度集成电力驱动是一个有吸引力的选择,欧瑞康(Oerlikon)推出了一款新开发的电力驱动变速箱。
1. 导言(EINLEITUNG)
作者介绍到,自从2013年开始,Oerlikon和Continental就开始一起紧密合作,为即将到来的电动车趋势做好准备,研发一款高度集成的、高功率的以及价格合理的电驱动产品。Continental研发和完成了第三代的电机和功率电子设备,Oerlikon负责全部的变速箱和驻车锁止装置的研发。
2. 系统要求(SYSTEMANFORDERUNGEN)
这款新的驱动系统包含三个部分:电机,变速箱,逆变器。目标是供应给电动车的前后横桥使用,使其前后拥有同样的驱动力并实现四驱功能。工作寿命是30万公里或者8000小时。
系统的要求是针对大概2200kg重的中型车而来,另外还包含一个驻车锁止结构。由于对于价格和功率上的严苛的要求,所以研发的指导思想就是简化、集成子系统功能以及精确化细节设计,尤其还要注意其噪声和振动特性。
电机的转子和变速箱的输入轴会共用一个轴承,电机和冷却循环系统和其他子系统必须集成化设计,以减小占有空间,质量和部件的个数。系统规格参数见下表:
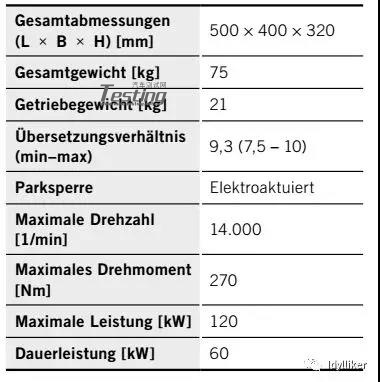
3. 变速箱的技术参数(TECHNISCHESPEZIFIKATIonEN DES GETRIEBES)
变速箱净重21kg,有两对减速齿轮并带有喷射润滑系统。整体轴距150mm,一级变速齿轮组轴距是75mm,二级变速齿轮组的轴距是117mm。主传动比是i = 9.37,其中一级传动比是3.42,二级的传动比是2.74。由于电机的转子和输入轴公用一个轴承,所以它们两个总共使用了三个轴承,使用的是滚珠轴承。中间轴和输出轴则使用的是摩擦小的圆锥滚子轴承,以实现紧凑的结构和减低自重。
.jpg)
最终输出传动齿轮被带有两个行星齿轮的紧凑型开式差速器固定在一起,输出轴通过连接式结构与行星锥齿轮连接。齿轮系的设计旨在使用ATF机油(自动变速器油)来实现所有环境条件(>96%)下的效率目标。
4. 设计上挑战(HERAUSFORDERUNGENDES KONZEPTS)
该产品的一个明显的特征是整体悬挂系统的设计和安排,深刻的影响着系统的噪声和振动以及功率输出能力。从健壮设计的指导思想出发,首先需要考虑的是轴承搭建,然后是从主轴到静力学结构的轴向载荷路径,以及铝箱体方案都要被考虑到:
- 在一个中央分流的轴承中,两个主轴中只能有一个直接支撑,而另一个主轴需要通过一个联轴器(花键和定心直径)进行布置。由离合器承载的轴的公差链需要更多的设计特征,并且因此可能导致更大的位置误差 - 影响变速器的NVH性能和电动机的性能。此外,联轴器还会影响主轴的径向载荷。
- 固定悬挂位置的设计,首先必须保证承受足够的轴载荷,其次也应该仔细分析,这些悬挂位置也应该有很好的适应性,以满足不用的边界条件和功能上的要求。
- 全铝箱体的用来实现不同的悬挂的点的设计布局的关键,这些点的设计布局可以影响轴的位置误差和负载路径的支撑。
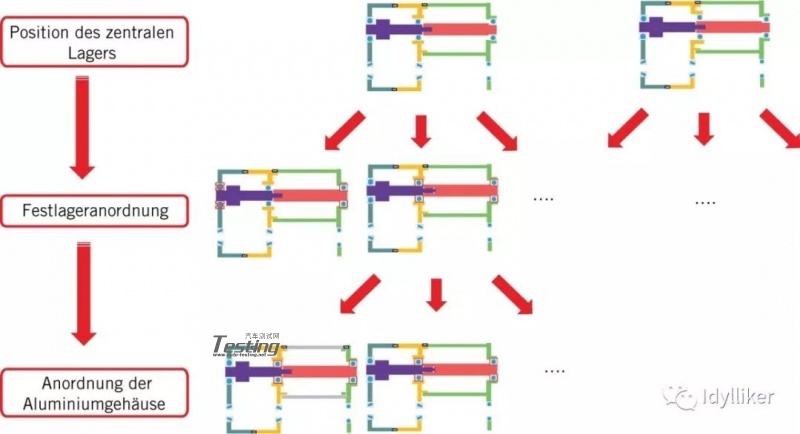
满足三个主要设计要求的集成方案会有超过三十种以上的选择。为了研究这些集成方案的优劣性,需要进行计算机虚拟分析和测试分析,这些将在样机制造和方案验证阶段中进行。
变速箱对整个系统的影响的预测主要集中在传递缺陷分析,主轴的表面应力/滑差状态。具有不同公差范围的实验统计设计(DoE)也是评估过程的一部分。很明显,验证耦合方法是系统最大的挑战之一。
5. NVH优化(NVH-OPTIMIERUNG)
为了实现NVH优化的目标,必须利用多种软件进行各类分析。齿轮变速箱设计的研发可以分为三个主要步骤:刚性环境中齿轮系的预先计算,在代表系统刚度的环境虾计算齿轮传动系以及在全系统环境下进行NVH模拟。
在刚性的环境中执行的计算,使得通过传递缺陷的预测和应力状态的预测,在可用的安装空间内来定义可能的齿轮传递链成为可能。
在变速器“代表性刚度”环境中的齿轮系的计算,已经算是子系统级的一个分析。其边界条件是基于静态刚度来确定,为了对齿轮,轴和铝外壳的设计进行定义,将会进行峰到峰传输误差和齿轮载荷的评估分析。
完整的NVH系统仿真是评估基于有限元方法的动态系统仿真的最后一步。
变速器的NVH模拟考虑了变形和构件刚度,共振和结构振动的所有影响。模型的精确度通过与实验测试的相关性来优化,所述实验测试包括传输组件的实验模态分析(EMA)以支持一步一步的从部件到组件相关性分析。对虚拟模型的所有结果的实验验证,对于仿真成功是至关重要的。因此,在项目早期的阶段就已经计划,在消声动力系统测试单元的系统层面的工作条件下进行噪声辐射测量和表面振动分析。
6. 驻车锁止(PARKSPERRE)
一种新颖的机电制动驻车锁能降低机构占用空间,并降低了有刷直流电机必须施加的用来租车锁止的扭矩。系统通过凸轮轮廓驱动驻车棘爪,通过该机构可以在各种情况下减少负载和啮合锁止的时间。自锁激活模块也被集成为系统的关键部分。
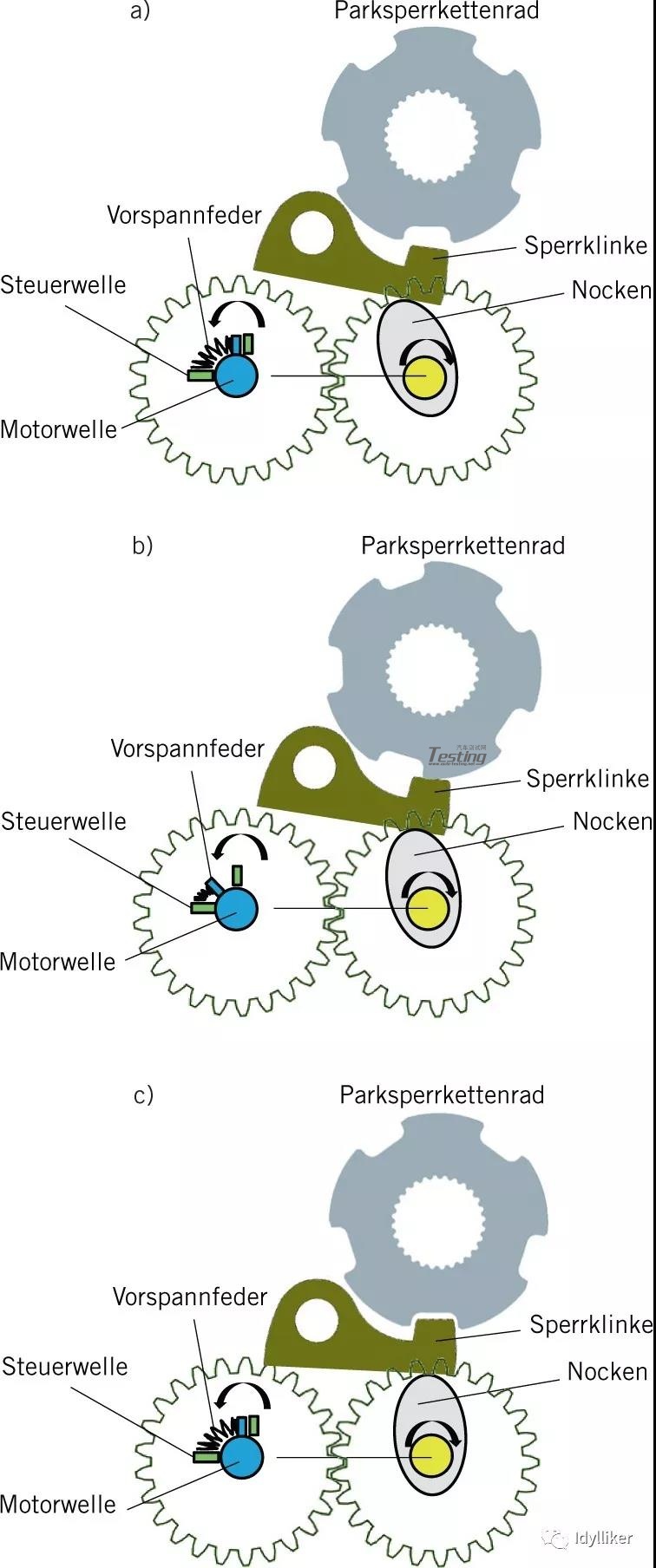
驻车锁有三种状态:
- 停车锁定解除:凸轮轮廓将驻车棘轮齿保持在驻车锁止链轮之外,图(a)
- 停车锁已启动:驻车棘轮齿正对驻车锁止链轮,因此无法完全啮合。由预加载弹簧储存弹性能量,图(b)。这一过程允许继续向前的车辆运动(最大允许车辆轴向运动90毫米)
- 停车锁定啮合:当凸轮轮廓处于啮合位置时,将锁定啮合齿锁定在驻车锁止链轮中,图(c)。
测量的锁定和释放时间在所有环境条件下<400ms,电流消耗总是<10A。
7. 润滑(SCHMIERUNG)
全铝箱体的设计主要是聚焦在轻量化,不同整车上安装的灵活性,以及集成所有喷射润滑的功能。此润滑系统的设计的目标是,尽可能的减少此功能所需要的不部件的数量,以及针对不同的电机的安装角度的功能的适应性。
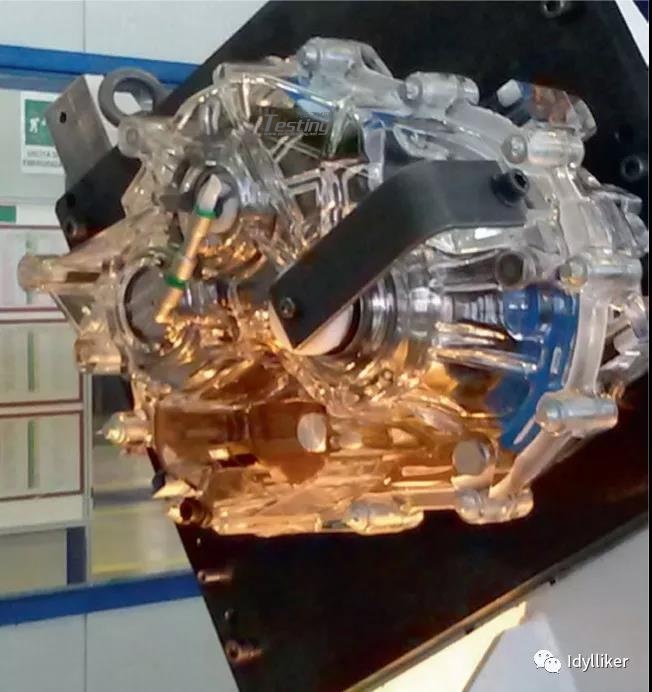
目前,各种解决方案通过在专用润滑系统上,使用透明外壳进行测试和评估,该系统能够模拟所有车辆的运行状况。
实验验证用于提供润滑设计的详细设定,而计算流体力学(CFD)分析可以用于项目早期采用,以便让开发团队对变速箱中润滑剂的运动过程有一个基本的了解。
这种方法可以最好的评估变速箱中的空气 -油混合物的行为。配油量可以随着变速器的不同安装角度而微调,可灵活应用于不同的发动机结构设计。
输油轴齿轮箱远高于油位,可以获得优化的外壳几何形状,用于收集在齿轮啮合区域离心的润滑油。
8. 为市场而设计(DESIGNKRITERIENFÜR DEN MARKT)
研发产品需要提前了解顾客的需求和新的要求。
一个重要的点是,应该明确定义出传动链的受载类型。利用虚拟的汽车模型进行驾驶周期模拟,利用受载等价原理计算其生命周期,用于对产品的定位的依据。其次是分析各类OEM对受载的需求,找到一个和谐的使用范围,以此来减少设计的冗余,进而实现产品的简化并降低成本。
还有一个重要的方面是,产品的安装布置应该适应不同的电机安排位置,以及变速范围应该有一个合理的变动范围。
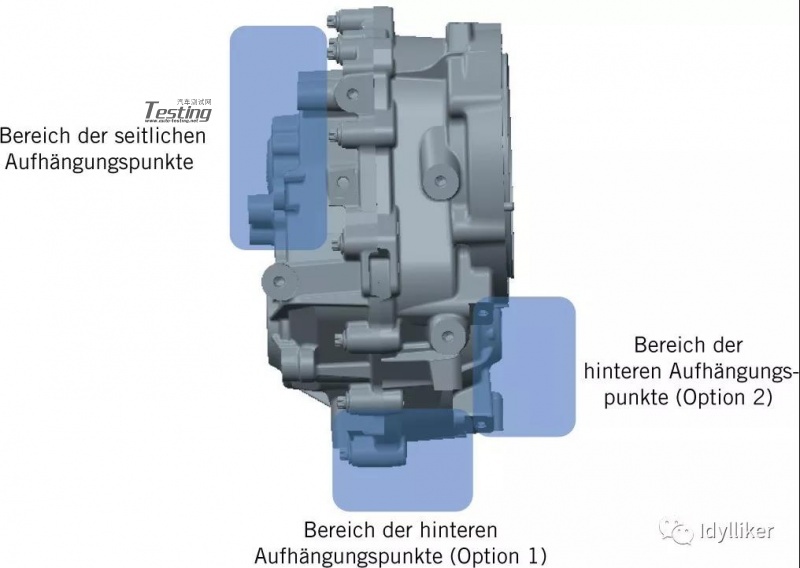
该系统的设计允许相对于标称位置的安装角度为25°,这是内部润滑概念的主要原因。传动比是可以修改的传动参数之一,以使传动系满足不同的客户要求。适用范围是i = 7.5 - 10。
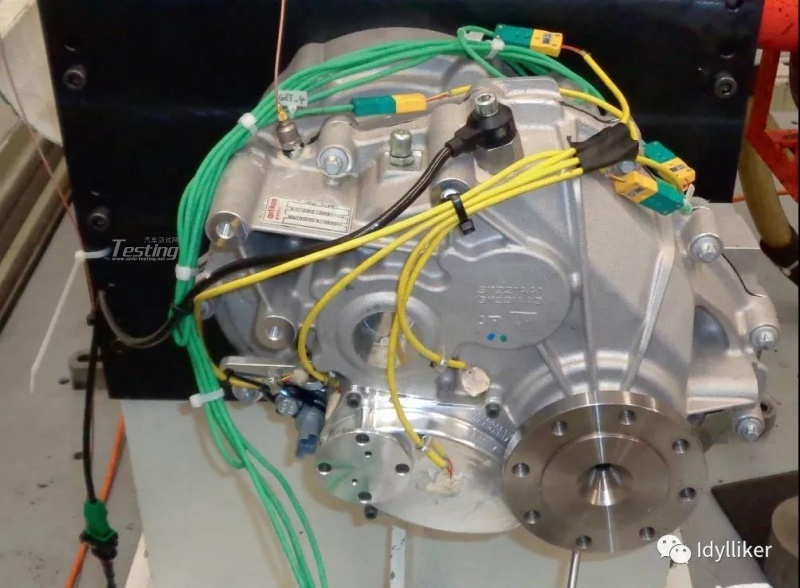
9. 样机和验证(PROTOTYPEN UNDVALIDIERUNG)
原型验证基于三个主要阶段,并且针对独立子系统和整个系统并行执行。这是产品开发的一个基本原则,它是一系列中间优化步骤,是设计开发的一个活跃部分。测试计划包括实验验证,以支持验证设计背后的虚拟模型和确保产品开发进度的强制性目标。
每个原型样机的各个阶段都必须通过润滑测试,效率测量,耐久性测试,声学测量,峰值扭矩测试,停车锁性能分析和负载下偏差导向分析,来验证系统的功能以及实现设定使用寿命目标的能力。各种原型样机的各个阶段被定义为以“一步一步”的方式实现概念验证,从而日益增加产品的成熟度和大规模生产到最终产品验证的技术水平。
10. 总结(ZUSAMMENFASSUNG)
电力驱动给开发者带来了新的挑战。在组件和系统层面都要考虑不同的发展标准,特别是在整合操作方面。借助这款EMR3变速箱,欧瑞康为下一代电池驱动的电动车开发了一款小巧,轻便,高效,安静且具有成本效益的单速变速箱。
- 下一篇:走进同济大学新能源汽车工程中心
- 上一篇:滚动噪声的主动消音以提升车内音质
最新资讯
-
中汽中心工程院能量流测试设备上线全新专家
2025-04-03 08:46
-
上新|AutoHawk Extreme 横空出世-新一代实
2025-04-03 08:42
-
「智能座椅」东风日产N7为何敢称“百万级大
2025-04-03 08:31
-
基于加速度计补偿的俯仰角和路面坡度角估计
2025-04-03 08:30
-
《北京市自动驾驶汽车条例》正式实施 L3级
2025-04-02 20:23