重载运输车轴疲劳分析
1 引言
世界铁路在“货运重载、客运高速”的主题下得到了快速发展,重载运输技术已被国际公认是铁路货运发展的方向。随着铁路运输向高速、重载方向发展以及机车段维修公里的延长,对机车走行部质量提出更高的要求。车轴是机车机械走行部关键部件之一,在运行中起着向钢轨传递静载荷、牵引力和制动力的作用,另外还刚性承受来自钢轨接头、道岔、线路不平的垂直和水平作用力,是一个受力复杂、工作条件恶劣的部件。车轴结构无论采用哪种形式,随着机车走行公里的不断提高,车轴材质最终由于疲劳而产生疲劳源并扩展形成疲劳裂纹。因此要对机车车轴疲劳区域进行超声波检测,以便发现车轴是否产生疲劳裂纹及其发展情况,及时掌握车轴状态并采取措施,确保铁路运输安全。
2 国内外车轴变化趋势
车轴是机车车辆转向架的关键承载部件,其疲劳破坏直接危及运输安全。近年来,随着铁路的重载化和高速化,车轴不可避免地会受到日趋严重的冲击作用。根据国内外车轴故障的数据显示,车轴故障有逐渐攀升的趋势。北京铁路局在2002年至2013年的13个月的时间里,连续发生3起RD2型车轴轴颈卸荷槽处冷切事故,造成车辆脱轨,构成险性事故。我国的重载和高速列车在现有线路条件下运行,这就使得深入研究车轴疲劳强度问题变得更加重要和迫切。
提高轴重是世界各国重载运输一致采用的一项重要举措,是降低运行成本的最有效的办法。重载运输的三大标准之一是轴重应在25t以上,美国所有一级铁路的标准轴重1990 年以后已是33t,加拿大一级铁路标准轴重已于1995 年改为33t。澳大利亚BH载铁路的轴重已经提高到35t,巴西卡拉齐斯重载铁路的轴重已经达到30 t 南非重载铁路的轴重已经达到26t(窄轨),瑞典重载铁路已将轴重由25 t提高到30 t俄罗斯铁路正在将货车轴重提高到27t,并且在加紧研究适用于35t轴重的轨道零部件,印度铁路在2001年开始计划将重载列车轴重提高到25t。过去北美铁路很少发生车轴故障,据报道,每年也就发2到3起,然而自1995年以来,车轴故障数量已经不断增长,增长的原因可能是由于轴重的增加、循环直达货运专列的里程增加和车辆装载量的逐渐增加。
随着重载运输的发展,轴重在不断增加,过去所使用的轴承在维修和运用安全性及可靠性方面存在的问题日益暴露。由于轴颈在轮重作用下会产生弯曲,导致轴承旋转运动时各部件表面间产生微量的相对移动,随着时间的推移,这些相对运行产生磨损(腐蚀)磨耗,逐渐地减少了轴承与轴颈间的预压力,由于相对移动和磨损磨耗率不断增加,最后导致轴承与轴颈间的松弛,轴承难以保持正常的工作性能。鉴于此,美国、南非和澳大利亚的铁路部门均在研究改善现有轴承的工作性能,提出了新的和改进的设计方案,用以减少和消除轴承的松脱现象等。新的和改进后的设计主要包括下列几方面: 第一是采用合适的轴承后档; 第二是采用稳定可靠的密封圈; 第三是采用最新的密封技术,如液力迷宫密封及在轴承与轴颈间使用液力迷宫密封衬套等; 第四是缩短轴颈并设计新的与短轴颈相配的轴承,轴颈的缩短等于有效地增加了轴承座的抗弯刚度,从而大大减少了轴承座的磨损量,保证了轴承工作的可靠性。美国研制的AP-2 型轴承就是基于此原理设计的并取得了较好的效果。
美国、同本、前苏联等国铁路部门都曾积极地采用疲劳可靠性理论对车轴作过可靠性分析,并逐步将车轴疲劳可靠设计与分析方法加以完善,纳入标准。Horger论文中的表列出了用各种热处理方法处理的车轴疲劳强度。对未处理车轴、2次正火和回火处理车轴、传统淬火回火处理车轴进行了试验。我国铁路采用可靠性技术解决车轴的疲劳问题丌展较晚,目前尚处于起步阶段,尽管国外的许多经验可供我们参考。
3影响车轴疲劳强度因素
影响车轴疲劳强度的因素有很多,比如材料特性、应力集中、尺寸效应、表面状态、载荷特性、压装条件、腐蚀环境等。但是在实际运用中,这些因素并不是单一作用于车轴的,而是多种因素的综合作用。
3.1车轴应力
在国际铁路联盟UIC515-3/1994《铁道机车车辆转向架车轴计算方法》和欧洲铁路联盟EN13041-1995《铁道转向架驱动车轴设计和计算方法》中,车轴结构应力集中系数分为两类,轮轴压装部位、滚动轴承及定位部位。
根据Mohr应力分析原理,车轴危险截面的应力可以表示为:
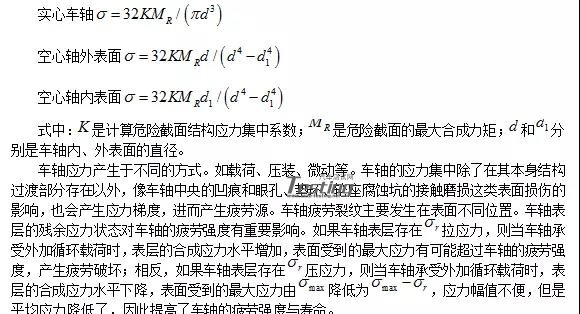
3.2 压装部位的影响
车轴断裂多源于车辆压装区的微动疲劳,分界区微观粘着点根部在疲劳过程中会产生驻留滑移带,从驻留滑移带可以萌生出短裂纹,短裂纹的生长导致了车轴的最终断裂。压装力不足同时会加剧轮座部位的磨损,从而加快疲劳裂纹的萌生。而过盈量和压入力过大会使轴向静态拉应力增大。在应力较高和过盈量较大的情况下,车轴上的裂纹扩展迅速,从而影响车轴的使用寿命。
压装部位疲劳强度受表面残余应力的影响更大于受表面硬度的影响。硬化层深度、压缩残余应力不论哪个加大都能提高压装部位的疲劳强度,但裂纹扩展的疲劳极限比裂纹萌生的疲劳极限更为显著。这是因为晶粒级的疲劳裂纹的萌生状态受剪切应力的强烈支配,与断裂有关的疲劳裂纹的扩展性质受拉伸应力支配。就是说压缩残余应力对前者无效,而轮毂端面和台阶端部的相对位置也对压装部位的疲劳强度有很大的影响。
3.3 载荷的影响
载荷对车轴疲劳强度的影响包括载荷类型,变化的应力幅,应力循环比率,载荷水平、数量和平均应力等。目前国内有关载荷对车轴疲劳强度的研究基本上是停留在小试件和理论研究阶段。1848年,James和Galton发表了基于铁道车轴交变载荷条件下的大量铁棒实验结果。这些是最早的车轴动载荷试验和思想。1995年日本铁道技术协会和铁道总研对四根新干线实物车轴进行了动载荷试验。试验中采取尽可能保持与实际工作应力相关的原则选取应力等级和循环次数。运行中发生弯曲应力的主要外力是轮重和横压力。其中横压力发生在通过曲线的时候,其影响占动应力的大部分。
3.4 其他因素的影响
车轴产生疲劳的原因是很多方面的,既受车轴材质、结构、制造工艺、牵引电动机和轮对参数选配的影响,同时又受机车运行线路状况、运行速度、牵引吨位以及司乘人员操作等客观因素的影响,由于受力特点、受力状态和工作环境不同,车轴在运行过程中受到弯曲应力、扭转剪切应力及组装应力同时作用,且均为复杂的交变应力,由此车轴疲劳是不会单纯由一种因素造成而是在多种因素共同作用下产生的。
4车轴疲劳检测
随着对车辆载重及使用可靠性要求的进一步提高,近年来国内外各铁路运输公司都在不断地改进车轴、轴承结构,如:缩短了车轴轴颈载荷中心到根部的距离,降低了车轴轴颈根部应力和弯曲变形;对轴承内圈及密封装置进行了优化设计,使结构设计紧凑,有效地改善了微动磨损对轴承性能的影响,极大地提高了车轴、轴承的使用可靠性[9,10]。但车轴结构无论采用哪种形式,随着机车走行公里的不断提高,车轴材质最终由于疲劳而产生疲劳源并扩展形成疲劳裂纹。因此要对机车车轴疲劳区域进行超声波检测,以便发现车轴是否产生疲劳裂纹及其发展情况。
疲劳可靠性问题涉及的不确定性因素主要有三大类:应力的随机性、构件材料疲劳性能(如疲劳寿命、疲劳强度等)固有的分散性以及影响构件疲劳强度和寿命各因素的随机性。疲劳可靠性分析的内容主要包括两个方面:其一、分析和计算交变载荷作用下在一定时期内构件或结构发生疲劳失效的概率或不因疲劳而失效的概率(即疲劳可靠度);其二、计算在交变载荷作用下构件或结构给定可靠度下使用期限(即可靠寿命)。根据疲劳载荷的类型,构件疲劳可靠性分析的研究还可分为:
等幅载荷下构件的疲劳可靠性
- 变幅载荷下构件的疲劳可靠性分析
- 随机载荷时间历程作用下构件的疲劳可靠性分析——根据疲劳载荷的类型,构件疲劳可靠性分析的研究还可分为:应用可靠性分析来评价车轴,主要有以下几方面的任务:
- 对新设计的车轴作可靠性分析及寿命估算。
- 按要求的可靠性指标改进设计。
- 按要求的可靠性指标对车轴作可靠性分析,制定出合理的厂、段修周期。
- 进行车轴报废及更新换代的经济性评价。
- 现有的超声波探伤法是将探头接触在车轴的端面或表面上,或是没有拆卸的重要部件上,向车轴中射入超声波,观察是否有伤痕的反射波。要有垂直探伤、斜角探伤和局部探伤三种方法,如图所示。
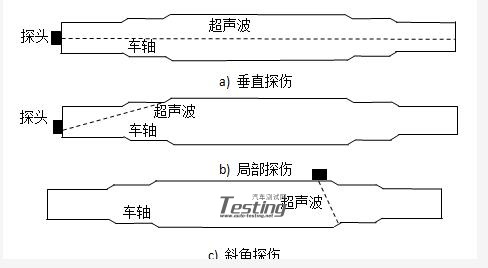
现有车轴检测方法
(1)垂直探伤
垂直探伤是由车轴端面垂直的射入2.5MHz的超声波。检测车轴在全长方向是否有损伤。垂直探伤的探伤范围最广,可以扫查到整个车轴纵向,但由于超声波不易接触裂纹,小裂纹难以检测出来,精度较低。
(2)局部探伤(小角度探伤)
针对可能发生裂纹的端部配合处,以10~15度的折射角从车轴两端面倾斜的射入2MHz的纵波超声波进行检查,该方法也称为纵波斜角探伤。局部探伤虽比垂直探伤精度高,但不能像垂直探伤那样扫查车轴全体,只能检测车轴的一部分。因此,仅以局部探伤检查车轴时,要使用多个探头。
(3)斜角探伤
斜角探伤一般使用37~45度的折射角从有曲率的车轴表面斜方向射入2MHz的横波超声波。斜角探伤可检查到齿轮座、制动盘座等部位的伤痕。斜角探伤比局部探伤更能检测出细小的伤痕,但是为便于探伤,必须把车轴表面打磨干,还要采用与车轴表面曲率相匹配的探头。
上述三种方法扫察的范围和精度各有所长,可采用多种探头对车轴多部位进行探伤,以提高探伤的精度和准确度。
5结语
随着我国铁路运输向高速和重载方向的发展,在现有条件下,需要进一步定量研究影响车轴疲劳强度的因素,为新型车轴设计提供依据。其中包括材料疲劳性能的研究,动态力学性能研究,各种生产工艺的研究,车轴设计研究等,并对超高周疲劳下车轴钢裂纹萌生和短裂纹的生长规律进行试验研究,分析冲击载荷和变幅载荷耦合作用对超高周疲劳损伤的影响和规律,从中寻找抑制车轴断裂的方法并建立超高周疲劳寿命预测模型。
物联网技术研究院旗下运营的,是专业从事有限元分析服务的专业机构,致力于有限元技术在企业中的推广应用,为企业提供专业的有限元技术服务,CAE技术开发咨询中心拥有一批经验丰富的专业技术工程师,涉及力学、机械、材料、汽车等多个领域,在各自的专业领域内均有丰富的理论知识和实践经验,与企业强强联合,共同解决产品研发过程中的技术难题。
CAE技术开发咨询中心开设巡讲培训班达120多场次,培训学员近6000余人,并且为众多的知名企业提供了有限元内训技术培训、咨询服务,特别是在航天航空、造船、工程机械、钢铁、汽车、能源动力等行业拥有众多的成功案例
阅读原文阅读 151赞 投诉
留言
最新资讯
-
飞书项目落地ASPICE解决方案,助力汽车软件
2025-04-24 09:59
-
驾驶员监控系统DMS合规认证的“中西结合”
2025-04-24 08:23
-
自动驾驶汽车测试关键行人场景生成
2025-04-23 17:12
-
R171.01对DCAS的要求⑧
2025-04-23 17:08
-
迄今为止最先进的版本:imc发布全新imc STU
2025-04-23 17:06