电动汽车电控系统参数匹配及优化深度解析
近年来,随着大气污染的日益严重、全球石油资源供应紧张及环保意识的增强,传统的燃油汽车面临着巨大的挑战,纯电动汽车越来越受到人们的青睐。实现电动汽车替代传统汽车的关键是纯电动汽车的整车动力性是否满足人们的需要。解决整车动力性能的关键因素在于如何实现电池质量小且储存能量大、提高电机的性价比及优化电驱动控制策略。通过选择动力系统参数,使得电机、电池及电控更好地集成到一起,是现阶段提高纯电动汽车整车动力性的重要方法之一。文章通过研究匹配电机、电池参数及整车控制器参数的基本原则,为纯电动汽车初期设计动力匹配提供了理论依据及基础数据,对新产品的开发提供了指导作用,大大缩短了开发周期。
纯电动汽车整车动力系统设计流程和需求
纯电动汽车动力系统由整车控制器、电机控制器、永磁同步电机、电池管理系统及动力电池等构成,整车动力系统的基本架构,如图1所示。纯电动汽车动力系统开发过程可采用“V”模式,如图2所示。定义好各个环节的功能需求,按照开发流程进行新产品的动力系统开发,文章针对具有单速比和永磁同步电机的纯电动汽车的参数匹配展开研究。
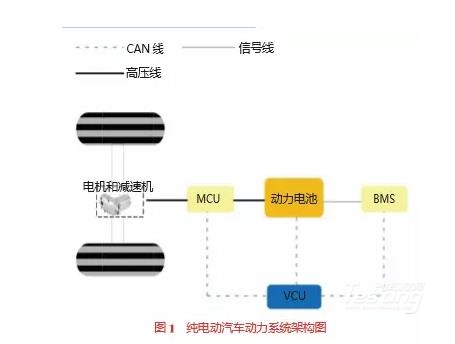
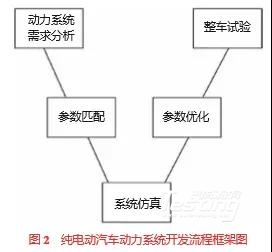
纯电动汽车的电机控制器(MCU)响应整车控制器(VCU)的控制和输出的扭矩值,负责驱动电机的控制并对电机状态进行实时检测,电池管理系统(BMS)对电池的荷电状态(SOC)、电压、电流及温度等参数进行测量,VCU通过采集、接收MCU及BMS等信息实现整车驱动模式控制、能量优化控制及制动回馈控制等功能。因此,纯电动汽车的整车动力性主要依赖于驱动电机、动力电池组、传动系统及电控系统的参数匹配。在电动汽车动力系统设计初期,汽车的续航里程、加速性能、最高车速及爬坡能力等能够反应系统的动力性,可根据动力系统指标选择合理的电机参数和动力电池参数等,以满足整车的动力需求。
驱动电机参数的选择和匹配
电机是纯电动汽车的核心功能模块,它将电能转变为机械能,并通过传动系统将能量传递到车轮来驱动汽车行驶。合理地选择电机参数能够更合理的使用动力电池的储存能量,从而提高汽车续航里程等性能。电机和MCU组成了纯电动汽车的驱动系统。MCU是一种能将动力电池输入的电能转变为适合于目标电机运行需求的另一种电能形式的电能转化装置。因此,整车的动力性能主要取决于MCU选择的合理性。可以根据动力系统设计需求目标匹配电机的峰值功率、额定功率、最高转速、额定转速及最大扭矩等参数。
(1 )驱动方程
根据汽车的驱动力和行驶阻力之间的力学平衡关系,估算电机的基本性能。汽车的驱动力-行驶阻力平衡关系的方程,如式(1)所示。
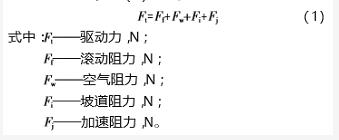
纯电动汽车传动系统传动比与效率、车轮半径、空气阻力系数、迎风面积及汽车的质量等性能指标确定后,可确定汽车的驱动力-行驶阻力平衡关系方程组,如式(2)所示。
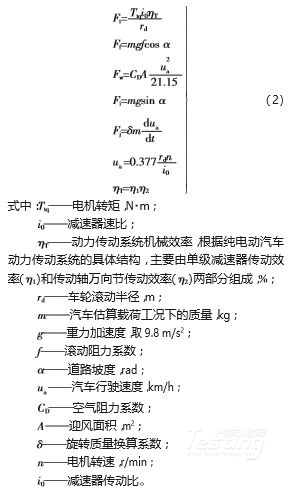
将式(2)代入式(1)可得汽车的驱动力-行驶阻力平衡关系方程,如式(3)所示。
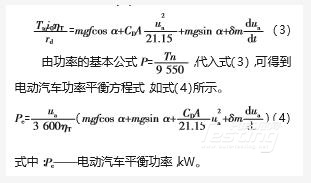
通过式(4)计算纯电动汽车在平衡状态下的功率大小,为后续电机功率选择提供基础数据。
(2) 电机功率的选择
纯电动汽车电机功率匹配的好坏直接影响汽车的动力性。如果选择较低功率的电机,将导致电机常工作在过载状态,如果选择较大功率的电机则其常工作在欠载状态,所以功率过大或过小都会大大降低电机运行效率。匹配合理的电机功率,不仅可提高汽车的续航里程,而且可提高能量利用率,符合设计电动汽车的目的。由式(4)可知,根据设计目标,驱动电机的功率(Pm)应不小于最高车速时对应的功率,另外由于电机不能长时间在最大功率下运行,那么最高车速时对应的功率需是额定功率。并且电机的峰值功率必须满足最大爬坡度和加速时间对应的功率要求,因此式(5)不等式组成立。
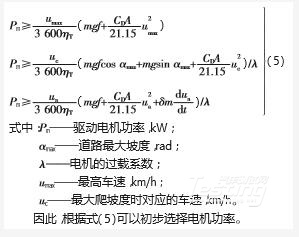
(3)电机转速匹配
纯电动汽车最高车速是指在没有风速和路面平坦的条件下电动汽车所能达到的最高行驶速度,即加速度为零、行驶阻力与驱动力平衡时的速度。最高车速作为评价汽车动力性的重要指标,使电机的转速匹配至关重要。
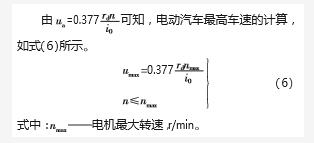
通过式(6)匹配出电机的转速即为电机的最高转速。
动力电池参数的匹配
(1) 动力电池数目和功率匹配
对于纯电动汽车在设计初期,系统选择的动力电池的功率必须满足驱动电机所需功率,而所需电池的最大放电功率取决于动力电池的电压与最大放电电流。因此,根据所选择电机型号的工作电压范围、功率参数等匹配电池功率,如式(7)所示。
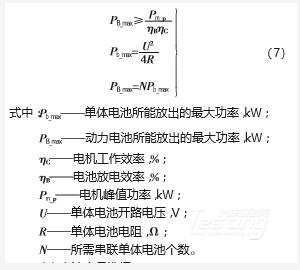
(2) 动力电池容量选择
动力电池作为纯电动汽车的动力来源,其容量决定了整车的续航里程,从而影响整车的动力性能。在设计初期为了提高续航里程,单纯匹配较大容量的电池会增加整车的质量并大大增加设计成本,因此,合理地匹配电池容量对提升整车的性能起着关键性作用。对于纯电动汽车,计算整车的续航里程采用GB/T18386《电动汽车能量消耗率和续航里程标准》,即用等速法和续航里程设计目标值法计算电池容量。
由能量守恒定律可得:
.jpg)
因此,通过式(9)即可初步计算动力电池应具备的容量值。然后再根据选择的驱动电机所需的额定输入电压范围、功率大小及续航里程所需的动力电池容量,确定电池组数量和所需动力电池总电压。根据工况法计算电池容量。
传动系统参数匹配
传动比对纯电动汽车的性能有较大的影响。不同的行驶工况下,合适的传动比可以很好地满足电动汽车的性能要求,使电机运转在高效率的范围内,同时减轻电机和电源的负荷,减少功率损失。
当电动机输出特性一定时,传动比的选择需满足整车的动力性指标的最高车速、加速时间及最大爬坡度的要求。电动汽车在最高车速时以最小的传动比挡位行驶,在最大爬坡度时以最大的传动比挡位行驶。因此,传动比的上限(iu)、下限(id)可由式(10)计算。
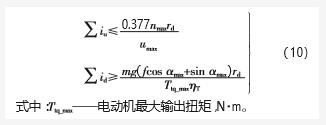
整车动力性能仿真及控制策略优化
(1)整车动力性能仿真
ADVISOR软件是一种在MATLAB和Simulink环境下的一系列模型和数据。使用ADVISOR可灵活配置汽车各部分参数和试验条件,在纯电动汽车开发前期可快速地仿真分析纯电动汽车经济性、动力性及参数匹配的合理性,使动力匹配的开发周期大大缩短。根据设计车型的目标参数,以及文中相应的计算公式,计算电机、动力电池及传动系数,然后打开ADVISOR仿真软件,将相对应的M文件进行相应的修改进行仿真验证,仿真界面,如图3所示。在仿真过程中可实时调整优化所设计的动力参数,以满足设计目标。
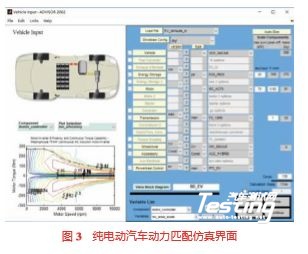
(2)整车控制策略优化
动力参数匹配完成,VCU作为纯电动汽车的中枢系统,起着指挥协调的作用,并对整车动力优化起关键作用。VCU根据驾驶员操作意图及汽车运行状态判断汽车相应驱动模式,整车控制策略的好坏直接影响着整车系统的能量综合利用率。经仿真验证和试验标定后选择最优数据,使得整车动力电池能量利用率达到最高,从而节省电量、增加续航里程。此外,在汽车减速或滑行时,可根据设计目标及驾驶习惯选择合适的能量回收系数,将整车不能利用的机械能转换为能为动力电池组充电的电能。
作为纯电动汽车的中枢系统,当整个电气系统出现故障时,VCU将检测到的故障进行等级划分,按照不同的故障等级提供相应的应对策略,这样就可以按照设计目标对整车系统进行功率限制,在保障安全的前提下,减少动力电池电量的浪费,同时减轻驱动电机的负荷,以保障整车控制系统处于能量最优状态。
结论
电动汽车电控系统的参数匹配选择对其动力性和经济性有着很大的影响。文章介绍了在纯电动汽车设计初期,根据整车设计目标,通过驱动电机参数、动力电池参数匹配仿真方法及设计整车控制策略,使得纯电动汽车“电池+电机+电控”三电系统在电动汽车动力匹配开发初期更好地集成到一起。为电动汽车的前期设计分析及后续整车各性能指标优化等提供基础理论数据,极大地缩短了新产品的开发周期。
- 下一篇:NVH测试使车辆更安静
- 上一篇:模型验证大大缩短模态测试时间
最新资讯
-
飞书项目落地ASPICE解决方案,助力汽车软件
2025-04-24 09:59
-
驾驶员监控系统DMS合规认证的“中西结合”
2025-04-24 08:23
-
自动驾驶汽车测试关键行人场景生成
2025-04-23 17:12
-
R171.01对DCAS的要求⑧
2025-04-23 17:08
-
迄今为止最先进的版本:imc发布全新imc STU
2025-04-23 17:06