镀锌板在乘用车车身中的应用
乘用车车身耐腐蚀状况受所处环境、使用材料、结构设计、生产制造工艺和维修保养等因素影响。其中,生产制造工艺中的车身电泳涂装防腐在国内主机厂已被广泛关注,且展开了同步工艺分析,但是镀锌板材料的使用率由于受成本约束却仍相对滞后。对于乘用车车身防腐工艺十分有必要建立一套行之有效的车身镀锌板设计数据库,从而制定乘用车车身镀锌板使用规范,来有效提高产品的防腐性能,优化防腐设计成本。
镀锌钢板耐蚀特性
锌的标准电极电位较低,铁基上的镀锌层在一般的腐蚀介质中为阳极镀层,该镀层可以有效减缓钢基板遭受腐蚀的程度,其在耐腐性能方面较冷轧板有着明显优势。平整致密的镀锌层可以通过锌的耐蚀性能进行腐蚀保护,切口、镀层局部破损区域可以通过牺牲阳极(锌层)保护,降低腐蚀速率。此外,锌镀层的无毒、廉价且防护性能优良,令镀锌工艺在防腐技术中占有重要的地位。
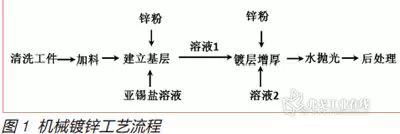
1. 镀锌板的腐蚀过程
一般将镀锌钢板的腐蚀过程分为4个阶段,即:镀层腐蚀阶段;镀层局部消失后对基材的牺牲防蚀阶段;镀锌腐蚀生成物抑制基材腐蚀的阶段;基材以无镀层时的腐蚀阶段。
2. 镀锌层耐蚀性因素
镀锌层的厚度是决定钢基板耐腐蚀性的最重要因素之一,根据瑞典防腐研究表明,镀锌层在7~10mm厚时防腐蚀性能最为合理,也有国内进行的相关研究认为,镀层厚度大于60g/m2时具有较好的耐膜下腐蚀性能。同时,镀锌钢板在实际使用中的耐蚀性,不但取决于镀锌钢板本身,还决定于镀锌钢板的加工工艺状态和使用环境,这三个因素也可成为镀锌钢板腐蚀三角形。
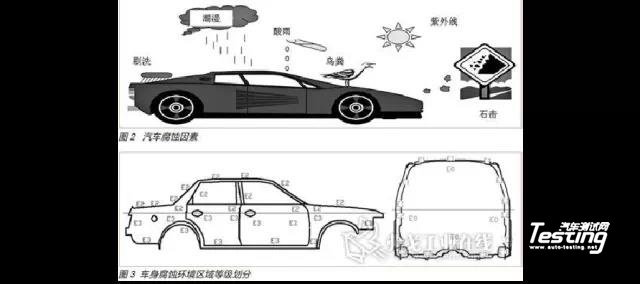
3. 几种常见的镀锌方式
采用金属锌镀层防腐方法主要有热镀法、电镀法、渗镀法和热喷涂法等,以及近年发展起来的机械镀等。
(1)电镀锌(EG) 电镀锌的基本工艺流程如下:预镀件→除油→侵蚀→抛光→镀锌→除氢→钝化/染色。电镀锌可以形成均匀、致密的镀锌层,镀层表面纯洁,氧化膜较薄,表面活性高于磷化,同时具有柔韧性好、耐蚀性高等特点。镀层的质量均匀性比热镀锌好,但镀层没有热镀锌镀层厚。因其具有表面质量高的特点,最适合用于乘用车车身外板。
(2)热镀锌(GI/GA) 热镀锌生产工艺流程如下:预镀件→脱脂→水洗→酸洗→水洗→挤干→涂水溶剂→烘干→镀锌→冷却→矫直→涂油→打包。
热镀纯锌(GI):AlxOy富集,ZnO膜较厚且厚度变化范围大,表面化学活性低于电镀锌;耐蚀性较好,其表面质量已可以与电镀锌媲美。
热镀锌铁合金(GA):通过热处理工艺使GI产品中冷轧基板的Fe向锌层中扩散,形成含铁10%左右的锌铁合金,耐蚀性相对更好;合金化处理使镀层形成多层相结构,提高了镀层结合力,同时也使得镀层的焊接性能得到改善;镀层表面做磷化处理后,具有较好的耐膜下扩蚀性能,但是存在较为普遍的针孔缺陷。
(3)机械镀锌 机械镀锌工艺的流程如图1所示,不同的工艺主要区别在建立基层和镀层增厚的方法上,大致可分为两种。
除动力电源外,机械镀不需要调控电源,也不需要加热装置,其操作方便,设备简单,能耗低,见效快。与电镀相比,当镀层厚度小于12.5mm时,电镀比机械镀稍占优势,但差异不大;随着镀层厚度的增加,机械镀的优势逐渐显露;当镀层厚度达到30mm时,电镀与机械镀的成本比约为1.8∶1。
针对镀层硬度和摩擦系数,将电镀锌、热镀锌、热镀锌铁合金和冷轧板进行对比,检测数据如表1所示。
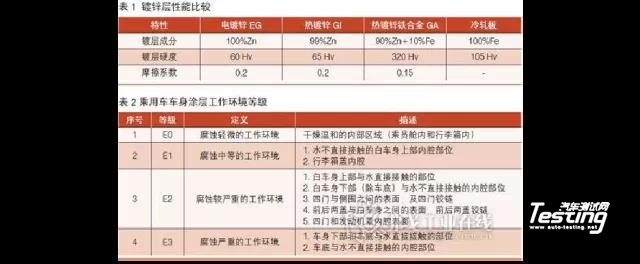
车身腐蚀环境
乘用车整车腐蚀一般按照三类进行分析:一是外观腐蚀,主要是外观面表面发生锈蚀,对外观件定义一般是3年无锈蚀;二是内侧腐蚀,产品件孔隙或腔体表面发生腐蚀,严重时锈穿孔,一般定义为10年无穿孔;三是结构腐蚀,重要功能件结构腐蚀会导致功能失效,从而出现安全性问题。上述三类腐蚀根据严重程度需要采用镀锌板。
随着汽车工业的快速发展和汽车企业间竞争的激烈化,人们对汽车抵御外界环境(见图2)破坏能力和汽车长期运行的可靠性、稳定性、耐腐蚀性以及汽车的整体外观性提出了更为苛刻的要求。从一些汽车企业售后反馈的信息看,汽车所受外界环境的三种损坏(事故损坏、磨损损坏和腐蚀损坏),其中以腐蚀损坏最为普及和严重。
影响整车腐蚀的因素有盐水、雨水(含酸雨)、湿气、化学品、阳光和石击等,同时汽车在不同地区、不同季节所处的环境也不相同。近年,国内自主品牌汽车制定了相应的车身防腐技术要求或者标准。根据乘用车车身结构特点及参考国外防腐要求,并结合整车海南强化腐蚀试验情况,对车身工作环境做出划分。典型的划分方式是按照腐蚀环境的严重程度进行阶梯式划分,如表2和图3所示。
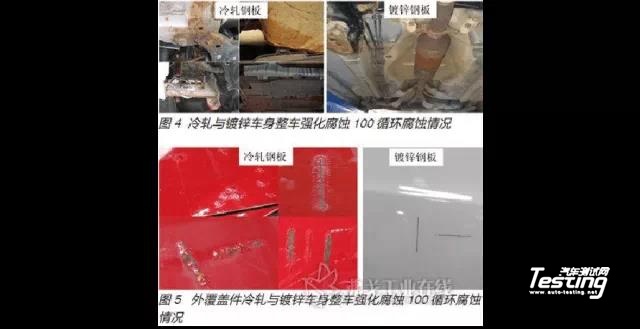
车身常见腐蚀情况分析
随着电泳涂装的发展,车身防腐性能上了一个新的台阶。然而,由于车身的结构特性,会存在一些无电泳或电泳不良的区域,这些区域往往在车身区域中又处于腐蚀严重或较严重的工作环境。通常,针对车身无电泳或电泳不良区域,主要是以涂胶密封、喷蜡和采用镀锌板应对。
1. 钣金贴合无电泳涂层区域
钣金贴合主要分为三种情况:一是焊接边贴合,在白车身中最为普遍;二是安装件之间的贴合,如翼子板与支架的贴合、门铰链与A/B柱的贴合;三是钣金件贴合或者间隙很小(间隙小而产生电磁屏蔽,无电泳),如加强板上贴合一个或几个加强件、纵横梁加强板与外板的贴合等。
(1)焊接边贴合锈蚀 一般也称为缝隙锈蚀。地板下侧焊接边缝隙,一些车由于未进行密封刷胶或喷底涂而未刷涂,整车强化腐蚀60循环出现严重锈蚀,侧裙边缝隙腐蚀也较为严重。
(2)安装件之间的贴合 白车身安装件之间的贴合区域。在无电泳层的情况下,一些车型并未做密封处理或者密封不严,而出现锈蚀。如开闭件外板折边胶密封不好,引起折边锈蚀严重。
(3)钣金件贴合 其主要表现在下车体的纵横梁腔体表面的锈蚀。
根据整车海南强化腐蚀试验(见图4)发现上述三种锈蚀区域采用镀锌钢板腐蚀程度相比于冷轧板较轻。
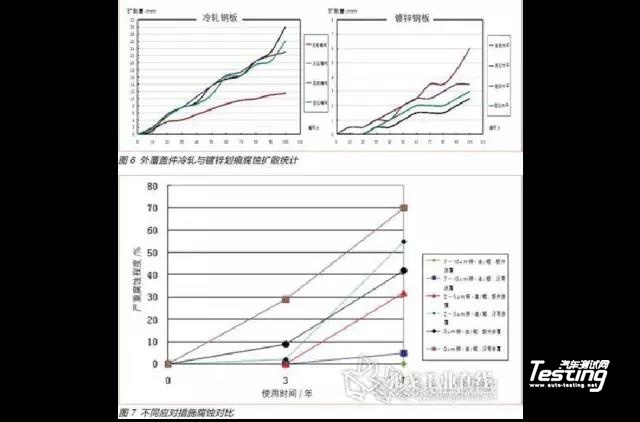
2. 石击或外力破损区域
石击区域主要有:下车体地板、侧裙边、发盖外板前端、翼子板和侧门部分区域等。此外,如开闭件外板、顶盖外板和侧围外板还易受到树枝或人为等划伤而发生锈蚀。图5所示为外覆盖件采用冷轧和镀锌钢板的整车海南强化腐蚀试验情况。
对分别采用冷轧和镀锌板的车身外覆盖件,根据海南强化试验抗划痕腐蚀性能的情况进行统计分析(见图6),发现外覆盖件采用镀锌板的划痕腐蚀扩散速度远低于冷轧板。
防腐应对措施
研究报告指出:使用预涂锌层及电泳,对提高底围缝隙腐蚀等级十分重要。在对乘用车的考察中,既没有预涂材料也没使用蜡和PVC的车辆,使用7年后底围缝隙表面的70%发生严重腐蚀,使用厚镀锌层板同时部分或完全用PVC涂覆的车型缝隙表面没有严重腐蚀。
如图7所示的统计结果表明,只靠电泳本身不能充分地防止一些能渗入水分和道路泥土的缝隙长达7年不发生严重腐蚀。为获得较好的防腐效果,要求采用电泳层及7~10mm的厚镀锌层 。
结语
随着镀锌技术的发展和汽车防腐蚀性能要求的进一步提升,镀锌钢板在车身上的应用越来广泛,欧美乘用车白车身镀锌钢板的应用比例高达90%。
如今,镀锌钢板已开始在国内自主品牌乘用车上应用,但是具体在车身哪个区域以及哪些件采用镀锌钢板仍有一些不明确的地方,且国内自主品牌还有一些企业没有具体的车身镀锌板设计标准。随着乘用车车身品质的不断提高,相信在不久的将来镀锌钢板在车身上的应用会更加明确,镀锌技术的要求也将更加成熟。
- 下一篇:数值仿真技术在车架防腐性能开发中的应用
- 上一篇:整车防腐蚀开发目标设定分析
最新资讯
-
沃尔沃汽车:创新驱动的豪华品牌
2025-04-24 18:16
-
飞书项目落地ASPICE解决方案,助力汽车软件
2025-04-24 09:59
-
驾驶员监控系统DMS合规认证的“中西结合”
2025-04-24 08:23
-
自动驾驶汽车测试关键行人场景生成
2025-04-23 17:12
-
R171.01对DCAS的要求⑧
2025-04-23 17:08