汽车车门过开强度分析与试验研究
摘要
以某车型为例,对该车门进行过开强度分析及试验。运用Hypermesh软件建立车门有限元模型,并对车门过开工况进行仿真分析得出车门位移数据和附件受力情况;提出车门过开试验方案,完成车门过开性能测试,得出试验推论;对比仿真结果和试验数据,验证有限元模型的准确性与试验方案的可行性。
车门是车身上的一个相对独立的总成,其性能状况对于汽车的安全性和舒适性都有重要影响。车门性能分析主要包括过开、下沉、全力关门、开闭耐久等。其中过开工况主要考察车门过开角度及受力状况,评价车门过开状态下性能,包括最大开启角度与变形等。过开性能反映车门及铰链系统和限位器抵抗超负荷开门力作用的能力。过开相当于在车门全开状态下,在车门打开方向施加载荷。车门过开工况属于模拟车门使用者误操作,车门过开下,会在车门、铰链系统、限位器、车身侧围外板产生很大应力,如果车门过开频繁发生,可能会引起车门系统过早老化和金属损伤,造成车门性能变差,甚至无法关闭车门,严重影响车门开合便利性。
CAE技术可以分析车門相关性能是否达到设计目标,而通过验证后的CAE模型可以进一步针对具体性能提出有效的解决方案。目前行业关于车门过开工况法规标准和试验方案研究较少,为了分析并改善车门多项性能,以某车型前门作为研究对象,搭建CAE仿真模型,模拟车门过开过程,并设计试验方案,建立试验系统,探讨确定过开角度的试验方法,完成车门过开试验。通过分析与验证确定了该车门及铰链系统、限位器系统抵抗过开的能力,确保车门性能达到目标值。
本文不仅对车门整体进行了有限元分析,并且进一步研究了车门过开工况中的车门附件受力情况,详细完整的分析了车门过开性能。在进行过开仿真分析的基础上设计了简单易行的试验验证,得出了相应推论。为车门过开性能开发验证提供了借鉴。
1 车门过开强度有限元分析
1.1车门有限元模型
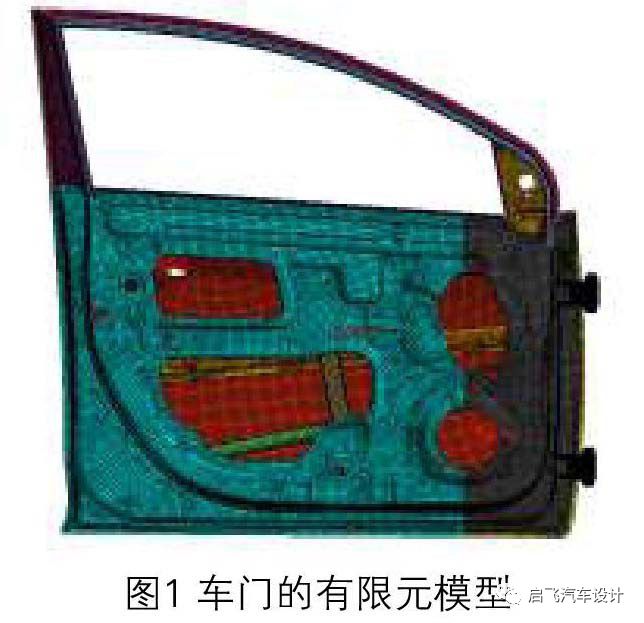
根据车门CAD数模建立有限元模型(图1),车门主要由不同厚度的薄板件构成,通常采用壳单元对其进行离散化。网格大小选择8mm,忽略尺寸较小的工艺孔,重要区域适当加密,焊点采用ACM焊接模拟,螺栓采用梁单元与rigid单元模拟,焊缝采用刚性连接。限位器有限元模型处于车门开启到最大角度位置。模型搭建完成后节点总数287385个,单元总数235662个,三角形单元总数10133个,三角形单元总数占单元总数的4.3%(<10%)利用Hyperworks中Optistruct求解器静力学分析功能对该车门进行过开分析。
1.2边界条件
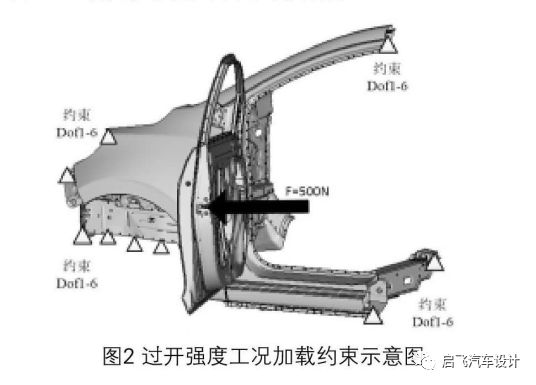
约束车身截面全部自由度,将车门旋转至最大开启角65.4度,移除对限位器和转轴绕其轴线的旋转约束以及车门锁点y向自由度,铰链连接处移除车门旋转约束。在车门过开工况过程中,车门自重是不可忽视的因素,使用CONM 2集中质量单元加载22kg。由于车门已经到达最大开启位置,铰链与车身外板、限位器压块上下端与车门外板已经接触,仿真中采用固联,限位器与车身连接部分采用螺栓连接。在锁点位置沿车门开启方向施加500N载荷,强迫车门继续开启。
1.3 分析结果
1.3.1过开性能评估
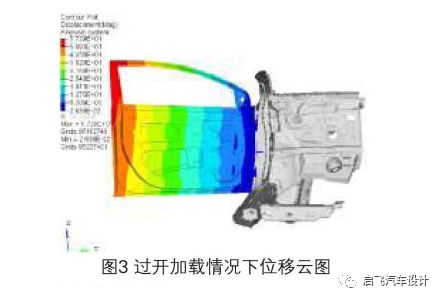
通过Hyperworks中的Hyperview后处理模块得到车门在过开加载情况下的位移云图(图3),在车门模型上通过Distance工具选择四个测点,获得四个测点位移数据,从而计算车门过开角度,评估车门过开性能(数据比较见表3)。
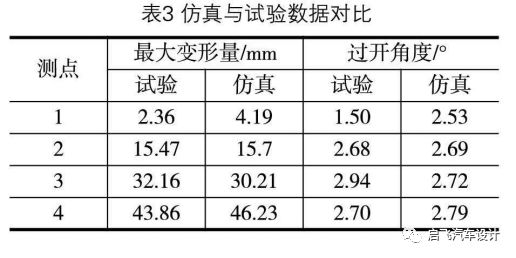
在过开工况中,除车门受力变形外,所施加载荷会在限位器与铰链处产生较大应力,若应力值超标,会产生永久变形,对车门开启与正常使用产生严重影响。以下对车门过开中车门主要附件进行分析说明。
1.3.2车门受力评估
在过开工况中,铰链承受较大载荷,铰链与车门连接处会产生较大应力,同时限位器支架通过螺栓固定在门外板,所以车门在过开工况中主要的受力位置在铰链安装孔与限位器安装位置附近,加载时所受应力如图4所示。车门所受最大应力位于铰链安装孔附近,其应力值为150MPa,小于零件材料许用应力。
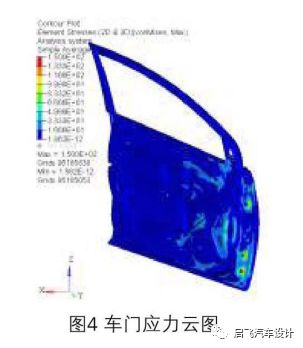
1.3.3限位器受力评估
车门限位器具有门半开时的支承功能和全开时的限位功能,其作用是限制车门的开启角度,减缓车门的开启及关闭速度,提高开关门手感。因此限位器是车门过开工况中重要承力件。限位器支架通过安装螺栓紧固在车身上,限位盒通过两个安装螺钉紧固在车门内板上,当开门的时候,限位盒便会沿着限位臂进行运动。
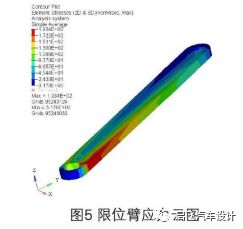
以车门开启到最大时为分析位置,此时限位拉杆处于最大行程。限位器拉杆应力云图如图5所示,限位器最大应力位于限位拉杆上,最大应力为193.4 MPa,小于零件材料许用应力,其他位置所受应力均满足要求,无破坏风险。
1.3.4铰链受力情况评估
车门铰链是车门总成中的主要受力件,当车门打开时,车门的重力完全由铰链承受,在过开工况中,铰链不仅需要承受车门重力,而且需要与限位器一同限制车门开度。随着载荷等级增加,铰链通过与车身连接端的接触限制车门开度,所以铰链在车门过开工况中应力水平也会影响车门过开性能。
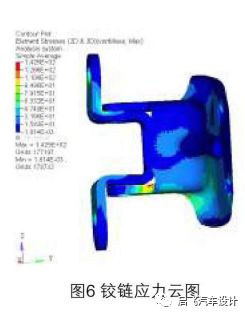
铰链应力云图如图6所示,铰链最大应力位于连接处根部,最大应力为142.5 MPa,小于零件材料许用应力,无破坏风险。
1.3.5侧围外板最大位移
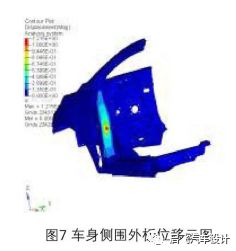
限位器支座通过螺栓固定在车身侧围,过开工况下,车身侧围承受较大载荷,所以车身侧围外板设计中需要保证车身有足够刚度。侧围外板位移云图如图7所示。侧围外板最大位移位于与限位臂安装孔附近,其位移值为1.215mm,满足设计要求。
2 车门过开试验
2.1试验方案
将车门安装在车身上,车身放置在平坦地面并加以固定,沿锁位处加载。由于角度难以测量,通过测试各测点位移,再经过换算得出车门过开角度。车门测试系统如图8所示:
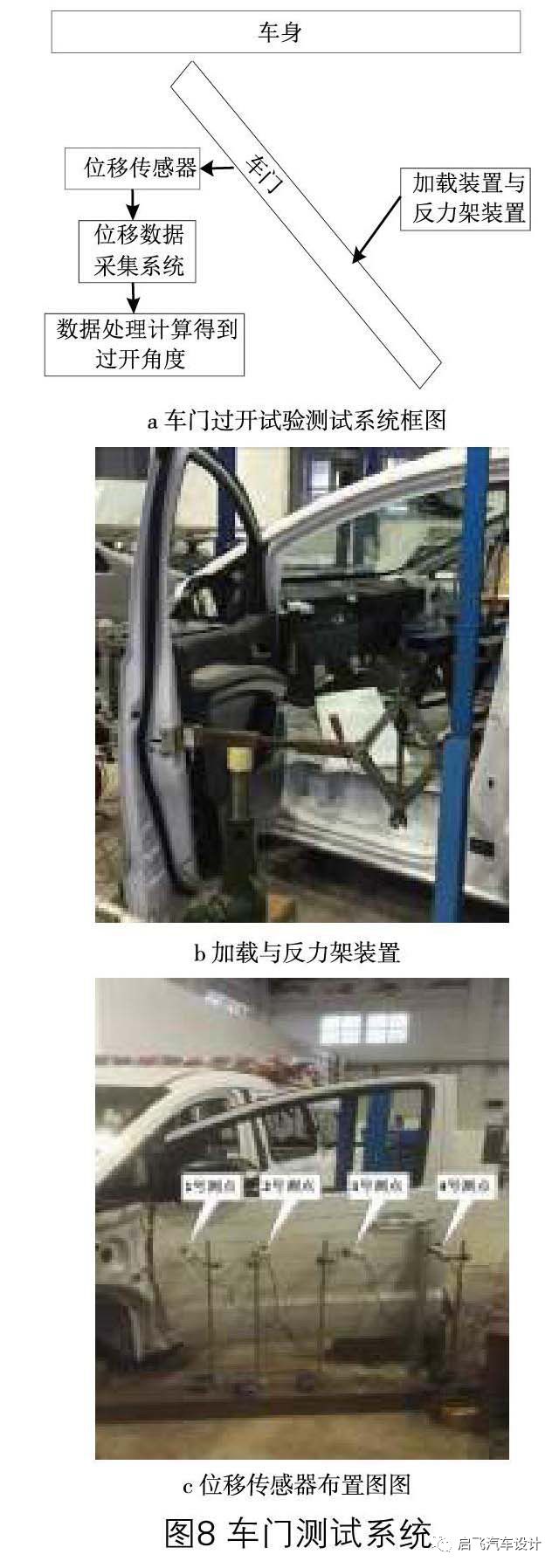
为了得到准确数据,在车门锁点与车门铰链轴线之间布置四个测点,一测点选择在加载点位置,其余三测点沿外板布置。另外,加载点位置设置标尺,量测标尺移动位置,作为车门开启角度参考。采用剪式千斤顶加载装置,前端放置力传感器。千斤顶一端顶住车门,另一端抵住反力装置,依靠千斤顶加载装置缓慢旋转实现对加载力的控制。
2.2试验过程描述
(1)将车门开启至最大开启角65.4°,用加载装置一端顶住车锁位置,另一端连接力传感器,调整好车门与测试系统,力与位移初值显示为0。
(2)缓慢逐级加载,加载级别为10kg,按设计要求最大载荷级别为51kg(500N),然后再逐级卸载至0,通过位移测试系统采集数据,得出在各级加卸载状态下车门各测点变形。
(3)试验重复3次并核实数据重复性,取3次数据平均作为处理依据。通过测点位移,计算车门过开角度。其基本计算原理见图9;各测点到铰链轴线距离见表1。
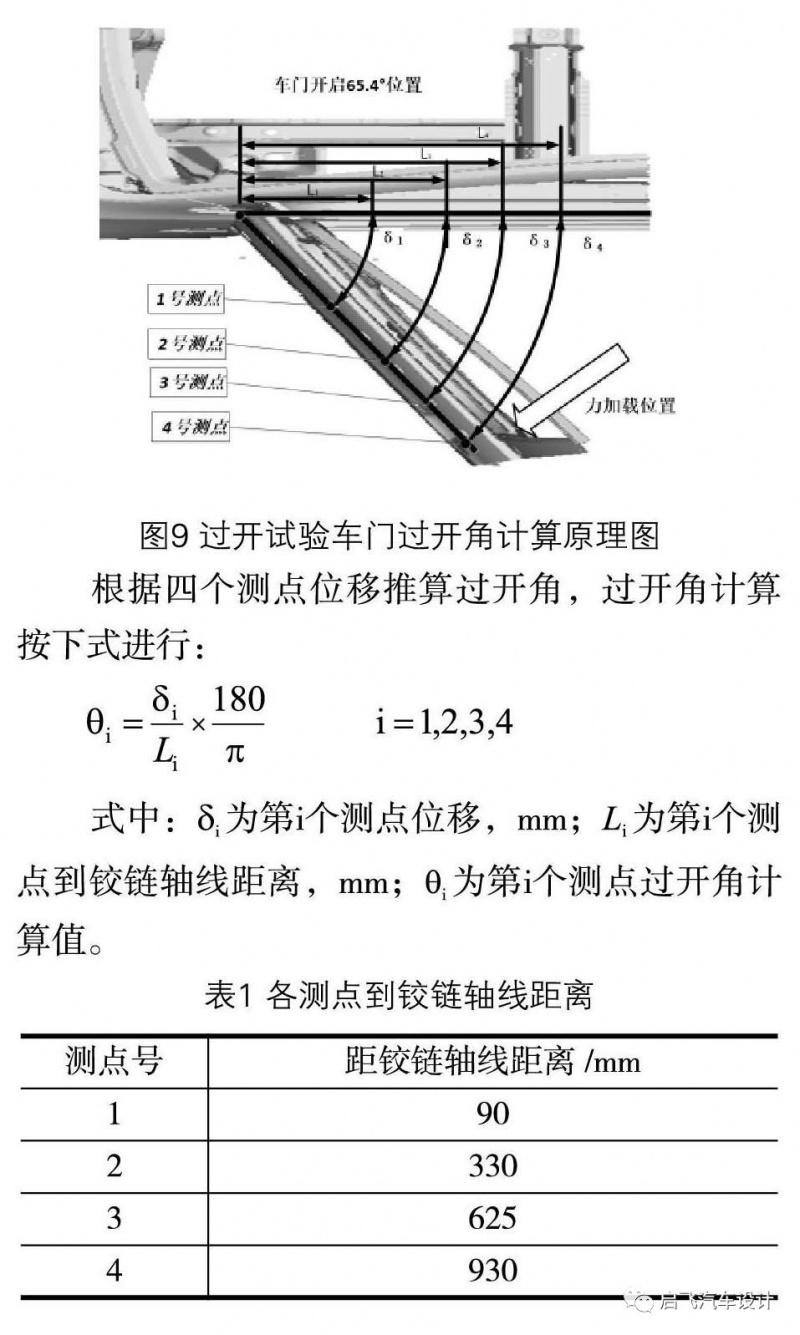
根据四个测点位移推算过开角,过开角计算按下式进行:
2.3过开强度试验结果分析
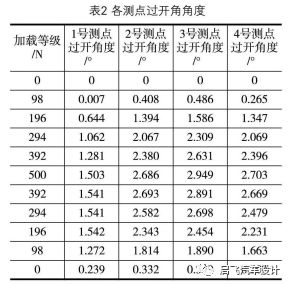
由各测点位移数据计算出四个测点过开角度与残余值(表2),反映4个测点在5个载荷等级下的加载与卸载过开角度试验值,多测点数据互相验证,说明车门总体过开情况,易于给出正确推断。由表2可知除1号测点外其余测点过开角度数据重合性较好,这是由于1号测点接近铰链轴线,位移变化值较小,对位置敏感。选取2,3,4号点过开角度作为依据,试验得出车门在500N载荷作用下,三号点过开角度最大,最大过开角为2.949°,锁位处则为2.703°,最大残余变形角度为0.349°,满足设计要求,试验结果表明该车门过开性能满足要求。

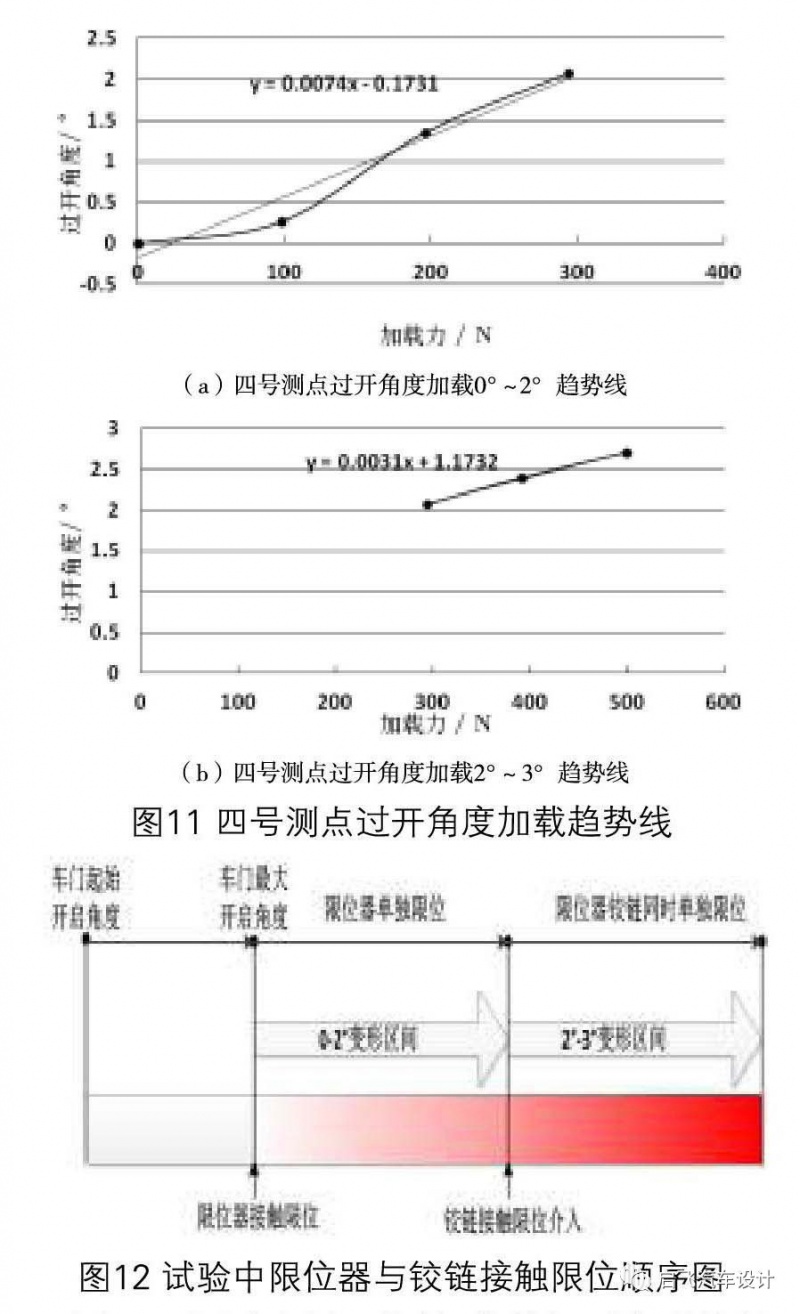
车门各测点加卸载荷工况下过开角变化曲线如图10 a、b、c所示,四个测点加载曲线在0~2°变形区间过开角度变化较大。以四号测点加载曲线为例,分段添加趋势线得出曲线斜率,如图11a、b所示,测点在0~2°变化区间趋势线斜率为0.0074,在2°~3°变化区间趋势线斜率为0.0031,可知在2°~3°过开角度变化率明显低于0°~2°区间。通过试验观察,这是由于在分级加载过程中,铰链与车身接触明显滞后于限位器限位,0~2°变形区间主要由限位器进行限位,在后续加载中2°~3°变形区间铰链与限位器同时进行限位,角度变化率小于0°~2°变形区间,具体过程见图12。试验推论为当车门过开时,铰链限位会滞后1.5°~2°。
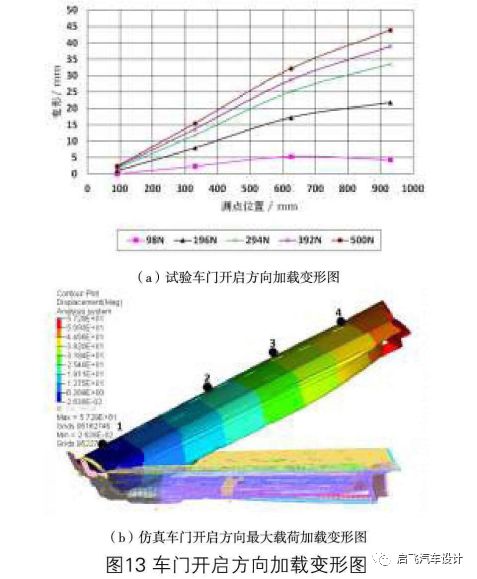
图13a反映各测点不同加载等级下变形情况,即各测点所在车门平面整体变形情况。曲线表明各测点变形趋势一致,图13b中线框图为车门起始加载位置,为方便与试验结果比较,位移云图为最大加载等级500N下位移结果放大十倍后的结果,可以看出仿真与试验数据变形趋势基本一致,同时在0~98N、98N~196N、196N~294N加载区间位移变化大于其余加载区间。
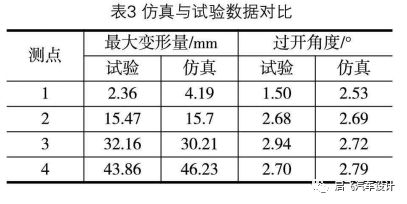
将仿真数据和试验数据对比如表3所示,对比数据表明,测点仿真数据与试验数据误差基本在±5%之内,说明了仿真模型的正确性。对照车门过开角度设计目标值,仿真与试验数据均说明该车门满足相关性能要求,同时反映车门过开试验方案合理,能有效验证仿真分析结果。3号测点试验值偏大的原因是由于车门在加载过程中铰链固定端与加载端同时受力,车门外板会发生一定弯曲变形,导致位于车门间位置的三号测点位移值较大。
3 结果分析
本文阐述了某款车型车门过开性能的仿真分析与试验测试,在仿真过程中计算出最大过开角和车门附件的应力状况。建立了车门过开试验简易方案,得出了车门过开角以及残余变形,验证了仿真的正确性。试验与仿真数据表明,该车门符合过开设计性能标准。
1)通过有限元分析与试验验证得出车门最大过开角,试验仿真相互验证,说明了有限元模型的准确性与试验方案的可行性。目前行业关于车门过开工况法规标准和试验方案研究较少,本文参考企业相关设计标准,进行了完整的車门过开工况仿真分析与试验验证,为车门过开性能的开发验证提供了借鉴。
2)有限元分析与试验结果表明,该车门在500N载荷作用下,其过开角度和残余变形、车身侧围外板位移,以及车门与限位器、铰链最大应力均满足设计目标值,车门过开性能达到设计要求。
3)车门过开试验曲线呈现出一定的非线性,这与仿真分析中的线性关系仍有不同,反映实际车门构造关系的复杂性。
4)在试验过程中,铰链接触限位滞后于限位器接触1,5°~2°,在铰链与限位器同时作用时,位移变化明显变慢。可以通过改进设计,减小铰链接触限位滞后角度,从而改善车门过开性能。
- 下一篇:三维石墨烯铂催化剂用于燃料电池研究获进展
- 上一篇:广汽新能源传祺GE3续航测试
最新资讯
-
腾势N9通过鱼钩测试的关键技术
2025-04-21 14:05
-
腾势N9鱼钩测试中的具体表现
2025-04-21 14:03
-
鱼钩测试的行业意义与历史成绩
2025-04-21 14:02
-
鱼钩测试的原理与流程
2025-04-21 14:02
-
邀请函 | 智能声振:NVH及语音音频质量技术
2025-04-21 11:23