汽车轮毂轴承失效模式与分析方法
关键词:轮毂轴承;性能试验;失效模式;分析方法
轿车轮毂轴承是汽车底盘上的一个重要组件,其是否能够平稳可靠地运转直接关系到行车的安全。普通轴承失效模式识别和分析方法的研究已有相关学者做过大量的工作。而轮毂轴承的失效分析起步较晚,近年来随着汽车工业的迅猛发展而逐渐受到重视。文献[5]对轮毂轴承载荷谱和失效机理做了深入探索。文献[6 - 7]分别就轮毂轴承的失效分析步骤及其对策与诊断方法进行了研究。
由于轮毂轴承失效模式多种多样,且相关研究工作存在一定的局限性,故在轮毂轴承开发阶段就需要进行各种性能试验,通过早期失效分析,找出其失效原因,为改善轮毂轴承的品质提供参考。
1 性能试验范围
轮毂轴承开发验证的台架试验包括:一般耐久性试验、高速耐久性试验、疲劳强度试验、密封试验、刚性试验、动摩擦试验及冲击试验等。设计的样品只有顺利通过台架试验,才能在主机厂所指定的路试场进行道路试验。道路试验综合了台架试验的各种考评项目,能够真实反映实际工况。不同的主机厂有各自的台架试验和道路试验规范,并明确了评判标准。当试验样品没有达到试验规范或标准的相关要求时,认为样品发生了早期失效,该样品便属于失效分析的对象,需查找出失效的原因。
2 失效模式
根据国内、外著名轴承厂商,如洛阳轴研科技,浙江万向精工,SKF,FAG,NSK 及NTN 等的统计,轮毂轴承早期失效模式有腐蚀、压痕、烧伤、裂纹和剥落等多种,现大致归纳如图1 所示。
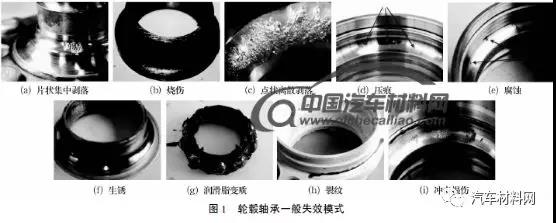
通过大量失效分析工作的统计发现,同一种失效模式可能是由不同的单一原因引起的,也可能是由各种原因综合作用的结果,因此,为分析轮毂轴承的失效机理,需要具备较全面的分析手段。
3 失效分析过程
开发阶段轮毂轴承的早期失效,即图1 所示的各种失效模式通常来源于5 个方面:( 1) 产品设计不合理;( 2) 工艺过程未能保证设计要求;( 3)试验设备不稳定; ( 4) 轴承安装不当; ( 5) 工作载荷过大,超出产品承受能力。针对这些方面,一般的分析过程如下。
3. 1 原始信息收集
当失效轴承被委托给分析室进行分析时,非常重要的一环是分析者首先要收集失效件的原始信息。原始信息一般包括: 设计图纸、工艺图纸、车型参数、试验规范、试验设备、工装信息、失效时试验员所做的轴承异常运转情况记录及失效样品原始检测报告。其中失效样品原始检测报告应包括轮毂轴承组件中各零件( 外圈、内圈、钢球、密封圈、保持架和润滑脂) 的材质报告和相关尺寸检测报告、装配件的相关检测结果等。由于失效件的原始状态已经受到极大破坏,故原始信息的收集对分析者非常重要,可以说收集信息的完备性决定着分析结果的准确性。
3. 2 设计确认
设计确认的目的在于以现行轮毂轴承行业的水准来评判轴承设计的合理性。为完成产品的设计确认,分析者需要对轮毂轴承设计理论有一定深度的了解,并能够运用一些辅助工具,如数学计算方法、小程序编译,相关辅助软件MATALAB,ANSYS,ABAQUS 及MSC. FATIGUE 等; 根据所提供的设计图纸和试验载荷谱信息[9],对产品设计工程师所完成的设计进行确认。需要确认的项目包括: 负游隙、静强度、刚性、滚道疲劳寿命、滚道挡边高、接触应力、疲劳强度和密封结构等。
由于目前广泛应用的第1 代、第2 代和第3 代轮毂轴承结构大不相同,故在设计确认上也会存在一定的差异。第1 代、第2 代和第3 代轮毂轴承的装车差异如图2 所示。相比于第1 代,集成程度较高的第2 代和第3 代轴承存在与凸缘心轴及转向节的配合,由于其通过锁紧螺母进行预紧,因此会影响到最终的装车游隙。游隙的设计应以最终装车状态的游隙作为目标,通常装车状态的理想游隙为- 0. 03 ~ - 0. 06 mm。
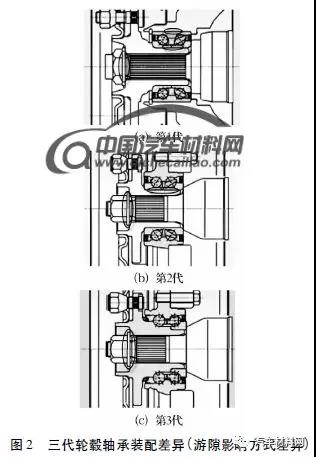
以带凸缘的第2 代或第3 代轮毂轴承为例,有些确认项是相互矛盾的。在客户要求轮毂轴承质量控制在某一特定量的前提下,需要在滚道疲劳寿命与所需强度间进行有效的平衡。通过增大钢球尺寸提高额定动载荷来强化滚道疲劳寿命就会降低轴承的强度,此时,应把轴承强度放在首位考虑,其属于关乎安全性的重要项目。
3. 3 工艺过程确认
在确定产品无设计缺陷后,需要以设计图纸和企业规范作为评价标准进行工艺过程确认,以明确设计是否得到保证。对于轴承制造商而言,轮毂轴承套圈材料、密封圈和保持架一般为外购件,套圈较关键的终加工工艺则由轴承制造商完成。工艺过程确认主要以相关检测报告为基础,根据检测报告逐一核实是否达到设计要求。需要核实的项目主要有:
(1) 原材料信息。所提供的钢材一般为热轧状态,需要对材料的元素成分、氧含量、非金属夹杂物、晶粒度及力学性能做出核实。
(2) 热处理信息。原材料在加工过程中进行的相关热处理,如正火和淬火,需要核实其基体和滚道的组织、硬度( 梯度) 及锻造流线是否满足要求。
(3) 成品零件尺寸。包括滚道沟曲率半径、沟径、沟间距、圆度、轮廓度、表面粗糙度、密封口径及其圆度、密封圈各唇口配合直径、唇口结构尺寸、滚道挡边高度和重要外轮廓尺寸等的核实。
(4) 外购件特性。查看外购件的检测报告,确认其是否满足使用要求。如密封圈的材质、拉伸特性、硬度,润滑脂的九大性能指标———黏度、高低温性能、极压性与抗磨性、抗水性、防腐性、胶体安定性、氧化安定性和机械安定性。
(5) 装配件检测结果。装配件的游隙和凸缘跳动均会对轴承滚道寿命产生较大影响; 装配件压装密封圈的平行差会影响到产品的密封性能,故均需要核实其是否满足设计要求。
在设计得到确认、失效样品原始状态的工艺信息核实无误及试验过程状态明确的前提下,基本能够推断出轮毂轴承是否具备通过各项性能试验的能力。
3. 4 分析流程
分析者接到失效件后,需要对失效件做相应的处理,从失效件的失效模式和损伤痕迹,并结合设计及工艺过程明确失效的原因。失效件在试验前的原始状态通过收集的数据得到分析后,对试验失效件也要进行一些辅助检测,旨在对比试验前、后及设计标准之间的差异程度。如果有差异,还需确定差异是否在可接受范围; 如果某项指标不在经验值范围内,则应作为失效的关注点有所侧重。
失效轴承检查分析流程和所用仪器见表1。根据国家标准、行业标准或企业标准进行相关检测。针对某型号轮毂轴承进行的失效分析项目,即表1 中的实施项目并非全部为必须的,而是需要根据逐步的观察、分析确定。有些失效原因能够较早、较容易被发现,而有些则较复杂,隐藏较深,基本要经历整个过程才能够发现。
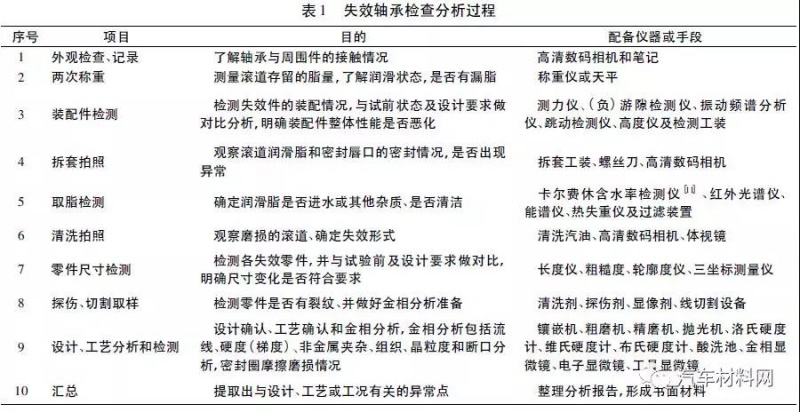
4 分析案例
以M 型轮毂轴承为例,安装于路试车辆上进行道路试验。车辆行驶64 000 km( 要求100 000km) 后左前轮出现异常声。经拆套发现: 外圈滚道外侧剥落,润滑脂变成棕黄色。按照上述流程逐步检测排查,最终确定为轴承密封失效。轴承密封失效分析的主要信息如下。
4. 1 润滑脂含水率
按照卡尔费休法对提取的润滑脂含水率进行检测,发现其含水率严重超标,检测结果见表2。
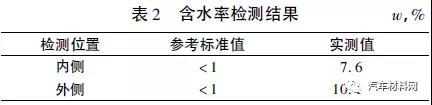
4. 2 沟道剥落
通过观察轴承沟道情况( 图3) 发现,的确是轴承密封发生了失效,导致泥水侵入轴承中,引起轴承润滑不良,最终导致沟道产生早期剥落。
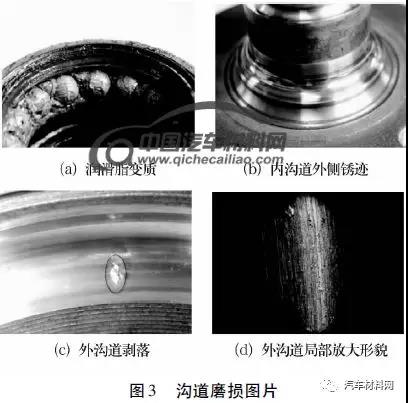
4. 3 密封圈磨损
在体视镜下对密封圈进行放大观察,发现外密封圈存在明显的偏磨损情况( 图4a 和图4b) 。对密封圈制样后在工具显微镜下检测其尺寸,也发现外密封圈存在偏磨损,图4c 和图4d 为密封圈上2 个不同位置的磨损情况。
通过查看同批装车的外密封圈尺寸检测报告可知,密封圈尺寸精度较好,符合要求。通过了解外密封圈的压装过程,经分析最终判定为外密封圈存在压装歪斜,导致平行差不好,使泥水经由密封圈缝隙侵入到轴承中,导致轴承提前失效。
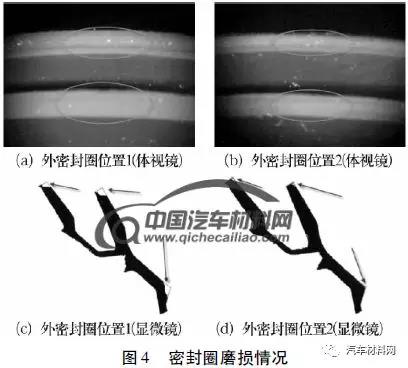
为此,建议针对存在的超差问题改进密封圈压装装置,并且产品由抽检改为全检,确保外密封圈压装平行差符合要求。
5 结束语
对轮毂轴承开发阶段涉及的各种性能试验及失效模式进行了归纳梳理,详细介绍了轮毂轴承失效分析的步骤与方法,并以某一密封失效的分析案例进行了验证。结果表明,该分析方法可为相关人员开展轴承失效模式的机理研究提供参考。
最新资讯
-
全国汽车标准化技术委员会汽车节能分技术委
2025-04-18 17:34
-
我国联合牵头由DC/DC变换器供电的低压电气
2025-04-18 17:33
-
中国汽研牵头的首个ITU-T国际标准正式立项
2025-04-18 17:32
-
为什么要进行汽车以太网接收测试?汽车以太
2025-04-18 17:26
-
产品手册下载 | NI 全新USB数据采集-NI mio
2025-04-18 16:39