利用功率循环测试以分析汽车IGBT芯片的材料性能
随着能量载荷压力的不断增加,功率电子设备创新带来了一些新的技术,例如使用能够增强热传递系数的直接键合铜基板、改进的互连技术(粗封装键合线、带式键合等)和无焊料芯片粘接技术,来增强模块的循环功能。这些新的基板有助于降低温度,载带可载荷更大的电流,而且无焊料芯片粘接可以是烧结的银,具有特别低的热阻。所有这些事实上都有助于改善器件中的热路径。但是,这些系统上的热应力和热机应力仍然会造成相关的功率循环和散热故障。这些应力可能会导致很多问题,如封装键合线降级、芯片粘接疲劳、叠层分层以及芯片或基板破裂。
结点中散发的热量是可能影响 IGBT 芯片中所用的芯片粘接材料可靠性的主要因素之一。功率循环测试是模拟模块寿命期的理想选择,因为与 IGBT 模块对应的开关循环次数可根据目标应用预测。
本文描述功率循环测试和瞬态热测试的组合实验,在此实验中我们使器件经受功率循环,从而产生故障,然后在不同的稳态之间执行瞬态热测试,以此确定 IGBT 小样品的故障原因。这些类型的测试为正确地重新设计模块的物理结构提供支持,如果需要,它还可充当热机应力仿真的输入。
我们的目标是利用可复制的流程研究当前 IGBT 模块中出现的常见故障模式。但是,这些测试的数量并未高到足以预测寿命期,我们只是通过这些测试来检查 IGBT 芯片中的降级流程。我们首先对样品进行瞬态热测试。试验测量结果显示,器件在不同稳态之间的热瞬态为 180 秒。在器件上利用 10 A 的驱动电流达到热稳态,当我们开始采集数据时它转换成 100 mA 的传感器电流。
图 1 显示了描述样品最初的“健康”状态的热瞬态函数。利用此曲线和相应的结构函数作为封装的详细数值表示的校准基础。结构函数是一维纵向热流的直接模型。在很多常用的三维几何形状中,结构函数是“本质”一维热流的直接模型,例如圆盘中的径向扩散(极坐标系中的一维流)、球面扩散、锥形扩散等。这样,结构函数可用于大致地识别几何形状/材料参数。结构函数可通过加热曲线或冷却曲线的直接数学变换获得。这些曲线可从测量结果或仿真热路径的详细结构模型中获得。
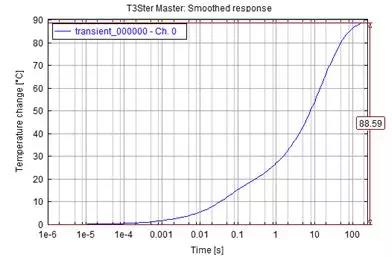
图 1:研究 IGBT 的瞬态热响应。
创建热仿真模型
我们随后会构建并验证模块的详细三维模型,以便分析结构内部的温度分布。在所有器件发生故障并拆解模块之后,再测量几何参数。图 2 中显示了模型布局(图 3 中显示的是叠层结构)。
这样,我们可以确仿真模型的行为方式与实际器件完全相同,然后我们进行材料参数调节,直到从仿真瞬态结果获得的结构函数与源自经验的结构函数相拟合。这个流程需要进行多次迭代。
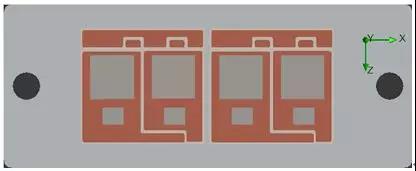
图 2:仿真模型的布局。
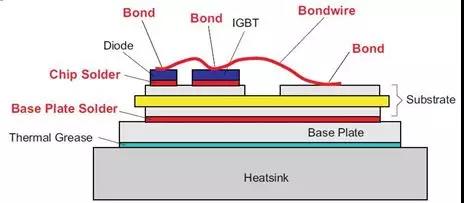
图 3:IGBT 模块的叠层结构。
根据测得的几何形状以及对材料参数的最佳猜想创建的基线模型显示,热瞬态行为与实际器件存在明显差异。此类偏差可通过校准模型并连续地完善模型数据予以消除。我们通过拟合从模型的热瞬态仿真获得的结构函数(图 4 中的红色曲线)与实际器件的测量结果生成的结构函数(蓝色曲线)实现这一目的。
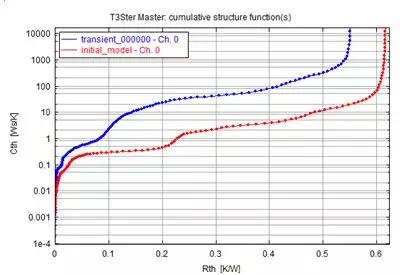
图 4:基线模型的仿真结果。
接下来,我们开始通过拟合封装的内部功能来校准器件。然后,我们沿热流路径方向从封装向外,连续地拟合不同区域的热容和热阻值。为了正确地调节芯片电容,我们要确保芯片的物理尺寸正确无误,并正确地设置热源。在这种情况下,我们需要增加受热面积,直到芯片区域的电容值在结构函数中互相重叠。
然后,我们需要确保将陶瓷层的热阻设置为适当的水平。随着陶瓷热导率的升高,结构函数中对应的热阻部分可能会降低以产生新拟合部分。在此之后,我们将器件与冷板之间的铜皮和热学界面材料 (TIM) 设置为适当的热导率以正确地匹配曲线(图 5)。
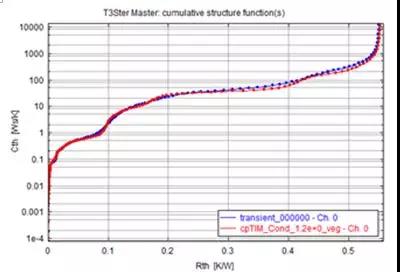
图 5:模型校准之后的仿真(蓝色)和测量(红色)瞬态的结构函数。
在功率测试仪中运行器件
只要记录了 IGBT 热结构的初始状态,器件就可以接受可靠性测试以评估其长期行为。我们将所选的 IGBT 模块固定到带有导热垫的水冷式冷板上。与大部分导热膏和导热硅脂相比,导热垫的导热性较差,但是它在早前的实验中显示出了极佳的热稳定性,因此不会影响测得的结果。冷板温度设置为 25 °C。
测试中的模块包含两个半桥模块,即四个 IGBT。将器件的门级连接到漏极,同时半桥模块使用单独的驱动电路供电(见图 6)。所有 IGBT 连接到瞬态热测试仪设备的独立通道。
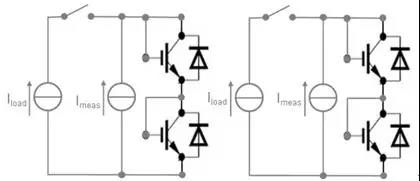
图 6:用于功率循环和瞬态热测量的 IGBT 电气连接。
我们决定在测试中对器件应用 100 °C 的变温以加速功率循环流程。选择此值是为了确保最高结温为 125 °C,这是器件允许的最高温度。我们将应用于模块的功率最大化以缩短循环时间,并选择适当的时机达到 100 °C 的目标变温。IGBT 模块可处理高达 80 A 的电流,但是由于器件的压降很高,额定功率就变成了限制因素。根据先前的试验测量,可选择 25 A 的加热电流。
我们需要使用 200 W 的功率加热 3 秒使芯片预热到 125 °C。设置的冷却时间应可确保芯片有足够的时间冷却下来,且平均温度在测试过程中不会发生变化。图 7 显示了时序图和温度分布图。
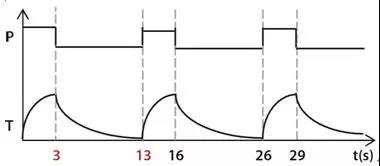
图 7:功率循环期间的加热功率和结温切换图。
无论发生压降变化还是热阻升高,应用的加热电流和测定时间在整个测试流程中均保持恒定。记录每个循环中的器件冷却瞬态,这样就能够连续地监测结温变化。每经过 200 个循环,使用 10A 加热电流执行一次全长瞬态测量,以检查热流路径的结构完整性。
门级氧化层损坏而非封装键合线缺陷引发的故障
在我们的实验中,我们会继续功率循环,直到器件完全无法工作(短路或断路)。这就是我们的故障标准。在被测的四个 IGBT 器件中,有一个器件(样品 3)发生故障明显地早于其他器件,只经过 10,158 个功率循环(图 8)。这种过早发生故障的原因可能是在冷板中安装不当或其他随机错误。其他三个器件,即样品 0、1 和 2 显示出相似的行为,分别在经过 40,660、41,476 和 43,489 个循环后发生故障。
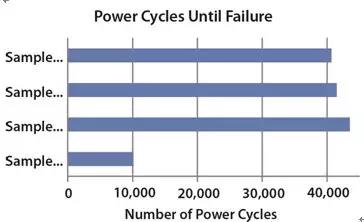
图 8:器件发生故障之前应用的功率循环数量。
在所有 IGBT 都发生故障之后,我们会拆解模块并检查芯片和封装键合线的状况。图 9 是其中一个芯片的照片,显示在测试期间有多条封装键合线断裂,芯片表面有一个区域发生烧灼,这可能是应用高电流时线路脱开形成的电弧造成的。
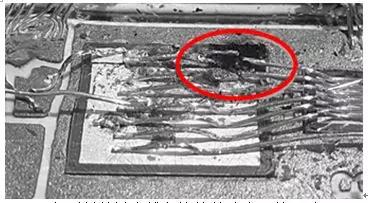
图 9:断裂封装键合线和烧灼芯片表面的照片。
尽管封装键合线出现明显的缺陷,但是中断的封装键合线并未造成器件故障。所有芯片的故障都是过热和门级氧化层损坏导致的。这些效应随后通过电气测试进行检查和跟踪:封装键合线破裂可通过 VCE(集电极-发射极)电压升高指示,门级氧化层损坏可造成 IG(门级漏电)升高。设计 IGBT 功率循环设备时,应当测量这些参数。
此外,还需要调查基板和底板之间的结点以及芯片粘接,以便了解过热来源,这是我们需要校准仿真模型的原因。图 10 显示了使用校准后的详细模型仿真加热期结束时,两个相邻 IGBT 的温度分布。相邻芯片之间的热耦合可以忽略不计;因此,可以单独地调查每个芯片。
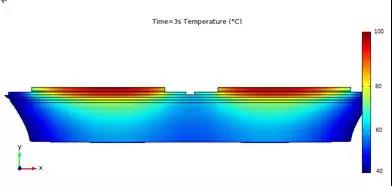
图 10:3 秒钟之后一个半桥模块的仿真温度分布。
由于加热时间短,基板-底板连接的最大温升为 71 °C,但是芯片粘接温度升高超过 100 °C。这种结果表明,结构中最易受损的地方是芯片粘接材料。
定期测量的热瞬态值允许我们根据应用的不同功率循环次数生成结构函数。图 11 显示产生的功率循环对每 5,000 个循环对应的结构函数的影响。在第一个电容阶跃之后,平坦区域对应于芯片粘接材料。结构在 17,000 个循环之前保持稳定;但是,在此之后,芯片粘接材料明显发生降级,并且其阻抗连续升高直至器件发生故障。
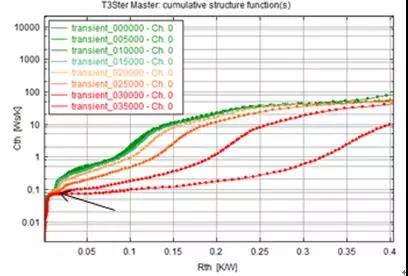
图 11:样品 0 对应于不同时间点的控制测量结果的结构函数。
如图 12 中所示,读取的芯片粘接层热阻除以系统的初始结-环境阻抗,并绘制为功率循环的函数。此计算可确认该层在 15,000 个循环之后迅速开始降级。热路径的变化极其显著,因为芯片粘接材料发生了极大的变化,在后一个结构元件中无法调查。但是,后一部分中的降级也可合理预测,只不过它们与芯片粘接材料的问题相比可忽略不计。
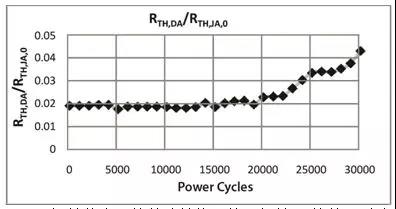
图 12:初始状态下的芯片粘接层热阻与结-环境热阻对比。
大约 20,000 个循环后,芯片粘接层的降级影响变得很明显,在大约 10,000 个循环内,样品的结-环境总热阻由于循环而倍增。在 30,000 个循环后,我们无法确定芯片粘接层的热阻,因为热扩散路径发生了变化。
最新资讯
-
我国首批5G毫米波行业标准送审稿审查通过
2025-04-28 08:56
-
5/16 厦门- 新能源汽车电驱测试技术的创新
2025-04-28 08:53
-
国内首个汽车电磁防护技术验证体系EMTA正式
2025-04-28 08:49
-
一文带你了解滤波器
2025-04-28 08:35
-
最新美国汽车技术法规清单
2025-04-28 08:31