基于齿轮修形的汽车变速器齿轮啸叫噪声改善研究
齿轮啸叫噪声是汽车变速器噪声的主要来源之一.在齿轮传动过程中,由于存在齿轮传动误差、弹性变形等因素,使得齿轮副在相互啮入、啮出时,偏离了理论啮合线,从而导致轮齿干涉、冲撞,进而产生激振力,引起传动机构的振动.在振动传动到变速箱外部结构的过程中产生共振而引发啸叫噪声.
对于齿轮副的非正常啮合,仅仅依靠提高齿轮的制造和安装精度来改善齿轮传动质量往往不能满足要求,而且会增加齿轮的制造成本;齿形修形,可将发生干涉的部分进行适量修除,改善齿面的接触,使传动变得平稳.研究表明,齿轮修形是降低变速器齿轮啸叫噪声的一种有效的途径.
1齿轮修形及仿真分析方法
1.1齿形修形
为了消除由弹性变形以及误差因素所引起的轮齿啮入、啮出冲击,需将接触齿对中发生干涉的部分进行适量修除,即为齿形修形.齿形修形有多种方式,将靠近齿顶的一部分材料去除掉,称为齿顶修缘;将靠近齿根的一部分材料去除掉,称为齿根修形.对于一对齿轮副可以分别对两个齿轮进行齿顶修缘,也可对其中一个齿轮同时进行齿顶修缘和齿根修形,两种方式可取得同样的效果.但由于齿根修整会使齿根强度减弱,通常采用前一种修形方法.由于齿轮加工误差造成齿形凸凹不平,尤其是中凹形齿形在一对齿的啮合过程中会发生两次冲击,因此在实际应用中,常采用齿形鼓形修形以改善齿轮表面接触,提高齿轮的承载能力.
1.2齿向修形
齿轮承受载荷后,由于受齿轮体和轴的弯曲扭转等弹性变形、齿轮制造误差及箱体变形的影响,会引起齿轮齿向载荷分布不均匀,造成载荷偏向轮齿一端,降低齿轮的承载能力.通过对齿轮齿向方向进行合理的微观修整,能够改善载荷在齿向的分布,使齿轮啮合更平稳.
1.3仿真模型及分析方法
借助于Masta仿真软件,以某变速器主减速齿轮副为研究对象,重点开展修形参数对齿轮传动机构特性的影响研究,以寻求降低啸叫噪声的最佳方案.运用Masta仿真软件中包含几何、强度设计以及受载齿面接触分析LTCA(loaded tooth contactanalysis)在内的高级LTCA模块,建立目标变速器传动机构的三维模型,模型包括齿轮、轴、轴承、差速器及变速器壳体等零件.其中材料、尺寸及位置关系均与实际情况一致.变速器和差速器壳体的刚度由有限元软件Hypermesh及Ansys计算得到.主减速齿轮副参数如表1所示.表1主减速齿轮副参数
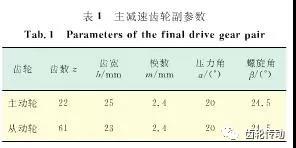
为模拟汽车变速器多变的实际工况,需要对建立的模型施加不同的载荷并进行静力学分析.
由于不同载荷下产生的弹性变形量不相同,这里选定修形参数的原则是:在确保常用工况最佳状态的前提下兼顾其它工况.按照这一原则,采用最大扭矩的50%进行理论计算.目标变速器常用工况扭矩为74.8~112N·m,其传动误差的目标值初步定为2μm,由材料20MnCr5的接触疲劳性能试验得知,最大齿面接触应力目标值不应超过1500MPa.考虑到齿轮啮合过程中刚度变化造成的影响,为了更加准确地计算传动误差和齿面接触应力,利用有限元分析方法,建立齿轮的有限元模型.同时考虑到变速器和差速器壳体的变形,运用FE(finiteelement)接口,直接导入变速器和差速器壳体等复杂异型件的有限元模型.
最终针对目标齿轮及齿面,以理论计算为Masta提供初始的修形参数,通过修形参数的调整,在圆柱齿轮微观修形与分析模块中进行的齿形优化过程,然后针对得到的传动误差和齿面接触应力进行对比分析,最终确定最佳修形参数.
2修形参数对啮合状态影响
2.1齿顶修缘量对啮合状态影响分析
为便于齿轮加工,主从动轮采取相同的齿顶修缘量,在修形曲线、修形长度等条件不变的情况下,改变齿顶修缘量,得到不同扭矩T下的传动误差TE和齿面最大接触应力σ.由图1可见,齿顶修缘后,传动误差改善不明显;由图2可见,齿顶修缘后,最大齿面接触应力明显下降,并且随着修缘量的增大,高扭矩时的应力逐渐降低,说明齿顶修缘后,齿轮啮入啮出时的干涉情况得到改善.
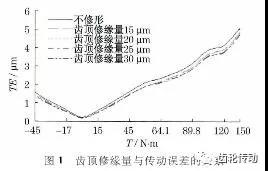
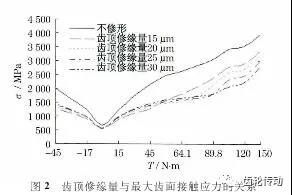
齿顶修缘改善了齿顶与齿根干涉造成的应力集中现象,但是随着修缘量的增大,齿面的接触区域逐渐变小,尤其是低扭矩下更为明显.修缘量为15μm,扭矩74.8N·m时的表面最小应力为零,说明啮合过程中有部分齿面没有接触.如图3所示,图中l为主动轮滚动距离.当修缘量为25μm时,接触区域严重缩小.为了使载荷尽可能地分布整个齿面,提高齿轮的承载能力,齿顶修缘量不宜过大.根据以上分析,认为齿顶修缘量为10μm为较适宜.
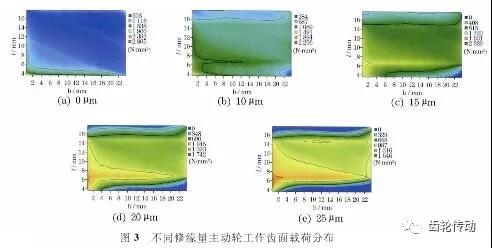
2.2齿形鼓形量对啮合状态影响分析
以齿顶修缘量为10μm,分别对鼓形量2,5,8,11μm进行齿形鼓形修形仿真,比较不同齿形鼓形量对齿轮传动特性的影响.由图4可见,齿形鼓形修形后,高扭矩下的传动误差明显降低,低扭矩下的传动误差随着鼓形量的增大不断增大,造成这种现象的原因是当齿形鼓形修形量较大时,降低了低扭矩下的重合度.
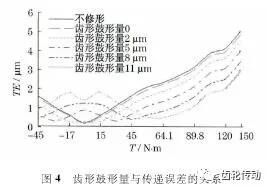
在低扭矩下,齿轮的接触情况开始变坏.由图5可见,齿形鼓形修形对齿面接触应力影响显著,鼓形修形后高扭矩下的应力降低明显.但是随着鼓形量的增大,最大应力变化的范围越来越小.当鼓形修形量为8μm和11μm时,齿面最大接触应力几乎不变.图6为扭矩在74.8N·m时,不同齿形鼓形量主动轮工作齿面载荷分布.从图6中齿面应力分布可见,齿形修形后,齿根与齿顶的干涉现象基本消除,齿面应力分布比修形前更加合理.由于齿形鼓形修形有齿顶修缘的效果,所以随着鼓形量的增大,齿面的接触区域越来越小,齿形鼓形量为11μm时,接触区域变成中间很窄的一部分.综合以上分析,从兼顾高、低扭矩的运行状态以及使载荷合理分布的角度出发,鼓形量不宜过大,推荐齿形鼓形量为5μm.
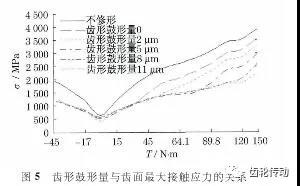
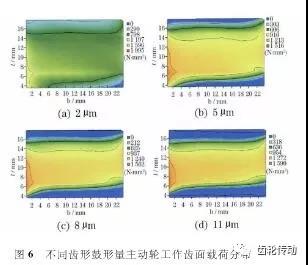
通过观察图6的应力分布图发现,在小齿轮啮入的一端,仍存在严重的应力集中现象.
这是由于轮齿啮合时,存在啮合歪斜度,而导致齿轮啮合时发生偏载,要解决这一问题,需要对其进行齿向修形.
2.3齿向修形对啮合状态影响分析
以齿顶修缘量为10μm,齿形鼓形量为5μm,进行齿向鼓形修形.从Masta分析结果得到齿轮啮合歪斜度为4.509 6μm,啮合综合刚度为15.5275N·(mm·μm)-1,选定鼓形量为8,12,16,20μm分析不同齿向鼓形量对齿轮传动特性的影响.由图7所示的齿间鼓形量与传递误差的关系可见,在高扭矩下,随着鼓形量的增大,传动误差明显降低.而鼓形量为16μm和20μm时,传动误差在74.8N·m(即最大扭矩的50%)基本达到最低点,与理论计算得17.765μm相符.
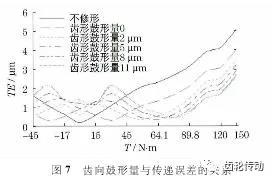
而在低扭矩时,传动误差随着鼓形量的增大不断增大,从兼顾低扭矩的传动误差角度考虑,齿向鼓形量不应过大.由图8所示的齿向鼓形量与齿面最大接触应力的关系可见,与齿形修形结果比,齿面最大接触应力明显降低.在鼓形量达到16μm时,各工况除最大扭矩之外,几乎全部低于1 500 MPa.说明齿向鼓形修形可进一步降低应力集中,使齿面的载荷分布得到改善.由图9(见下页)所示的扭矩74.8 N·m时,不同齿面鼓形量主动轮工作齿面应力分布可见,鼓形量为16μm时,最大应力基本集中在齿面中部,偏载现象已消失,基本达到了降低传动误差和改善齿面最大接触应力的预期目标.
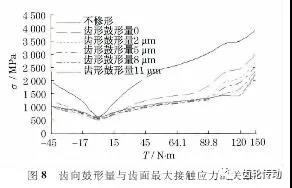
3噪声试验与分析
试验采用Head公司的Squadriga系统对车内噪声进行测量,该测试设备有两个麦克风对各工况下的室内噪声进行测量及分析,其采样频率为16kHz.测试过程中麦克风放置在司机双耳周围,以模拟乘客人耳听到的室内噪声.为得到不同输入转速下车辆的室内噪声,使用两个速度传感器来测量变速器输入和输出的速度变化.为了得到更准确的分析结果,采用阶次(振动频率与轴频的比值)分析方法,通过计算得到目标变速器主减速齿的噪声阶次为9.8阶.试验结果如图10所示,图中n为输入转速;SPL为声压级.
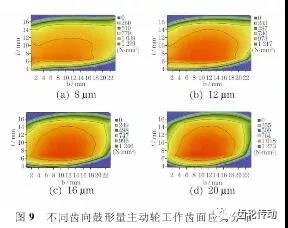
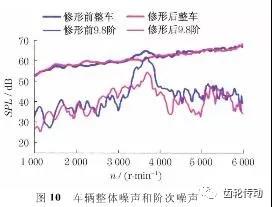
结果表明,修形后整车9.8阶噪声较修形前有明显降低,噪声峰值大约降低8dB左右.由图11所示的的车内噪声图可见:修形后整体噪声峰值消失,啸叫得到明显改善.
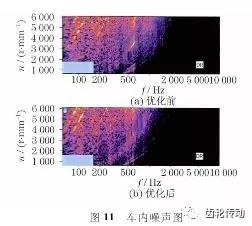
4结论
a.仿真分析得到的最佳修形量结果与50%扭矩点(即常用工况下的扭矩)理论修形量计算结论基本相符.
b.适当的齿顶修缘能有效减小齿轮啮合干涉,从而降低齿轮传动误差和最大齿面接触应力;修缘量过大,反而易导致齿轮接触区域减小,产生啮合冲击.
c.齿形鼓形修整能够使高扭矩下的应力降低明显,适当的修形量能有效改善齿根与齿顶的干涉现象,使齿面应力分布更为合理.
d.齿向鼓形修整是改善齿轮啮合时最大接触应力偏载的有效措施.
e.试验结果表明:修形后整车9.8阶噪声较修形前噪声峰值降低大约8dB左右;修形后整体噪声峰值消失,啸叫明显改善.
最新资讯
-
全国汽车标准化技术委员会汽车节能分技术委
2025-04-18 17:34
-
我国联合牵头由DC/DC变换器供电的低压电气
2025-04-18 17:33
-
中国汽研牵头的首个ITU-T国际标准正式立项
2025-04-18 17:32
-
为什么要进行汽车以太网接收测试?汽车以太
2025-04-18 17:26
-
产品手册下载 | NI 全新USB数据采集-NI mio
2025-04-18 16:39