浅析动力电池功能辅件
现在的行业趋势来看,动力电池厂商越来越朝着系统整体集成能力的tier1靠近,主要部件除了电芯要自己做,bms一些顶尖的动力电池企业也选择自己做,而除此之外其实还有很多功能辅件,这一块大多数厂商均会选择向上游二级或三级供应商进行采购,这些主要包括:比如电池包的整体结构件:如电池外壳,侧板,电池底板;模块与模块间的高压回路连接件,模块的壳体,盖板;方壳电芯的方通,盖板,软包电芯的铝塑膜;正负极与极片的金属软连接,电芯与电芯间的跨界片;绝缘隔热类的,电芯间的绝缘垫片,电芯内的衬套,电池包的密封圈或者其他,当然还有一些技术壁垒高的高压器件,如继电器,保险丝(包括MSD),HVIL回路线束等,如果是液冷系统的话还会涉及到冷却板,冷却管,heater等器件。直观一点,从第一电动网李浩晨老师《简单易懂的动力电池系统设计讲解》的文章里截了两张图,非常的清晰:
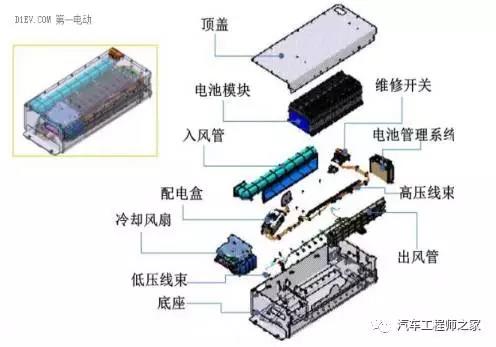
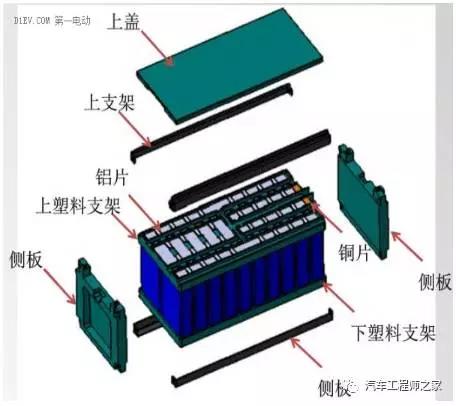
当然这是个风冷的包,包里和模块上主要的结构件大概都能看清楚,当然电芯本身还有一些结构件如下:
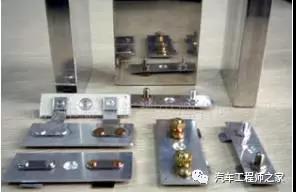
电池盖板及方通示意图
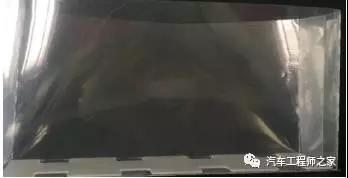
电芯内绝缘衬套示意图
实际各个厂家会因电池包设计和功能的不同而有选择性的采用以上的大部分用于自己的产品之中,从而对动力电池系统的结构完整性,绝缘性,热管理及安全性进行辅助功能的应用。
动力电池功能辅件的作用
承上所述,这些功能辅件的作用大致分一下,主要包括了结构的完整性支撑,电芯间的功能连接,绝缘阻燃与密封,热管理功能,高压安全性保护:
.jpg)
当然以上有很多设计的功能都是叠加的,不能完全区分开来,例如电芯的上盖板既保证电芯结构上的完整也通过安全阀等设计达到热失控时泄压的目的;电芯间的垫片既起到了功能上的绝缘阻燃也起到了结构上的电芯寿命后期膨胀的缓冲等作用。
不同的功能辅件所要求的技术特性是不同的,例如电芯的壳体主要作为电芯内活性物质与外界全生命周期的屏障,因此耐久,耐腐蚀等性能显得尤为重要;电芯间的跨接片又要求内阻低通过大电流时发热小,连接可靠性高,能通过振动要求,而采用软连接的多层金属则又要保证焊接的质量;而密封圈等设计又是出于对电池包的密封性能的要求,既不能过粉尘也不能过水,一般能整体通过IP67标准;继电器则要求大电流通过时不粘连,能有效开关;因此整体上来看,不同的要求和材料决定了其本身的技术难度和壁垒。
动力电池功能辅件的技术壁垒
单从市场应用上来看,目前在乘用车型中高压器件,铝塑膜以及一些超薄水冷板设计上国外产品仍占据着一定的主导地位,而在金属或塑料结构件,隔热或绝缘密封件上已是国内产品的天下。本文暂不讨论目前国外产品仍占主导地位的功能辅件,显然他们仍具有一定的技术壁垒,那么目前已经国产化的功能件,例如系统结构件和绝缘密封件等还有技术壁垒吗?
答案是肯定的。笔者早些年有幸参与过动力电池的研发过程,在产品研发过程中也经历过类似于“盖板又漏了”“安全阀怎么没开”这种结构件失效的情况,因此对锂离子电池结构件的重要性深有体会,现在随着工艺的成熟与技术的进步像笔者早些年遇到这些情况相信已经越来越少了,壁垒消失了吗?笔者认为并没有,其实技术的成熟并不意味着壁垒的消失,而是从技术难度所造成的壁垒,变成了其他因素的壁垒,笔者认为主要在于以下三个方面,从高到低依次为:
第一功能辅件已融入电池系统的热管理和安全性设计,成为一套较难分割的体系;
找个例子来说明,2016年12月16日,行业龙头CATL举行了媒体活动,展示了如下资料:
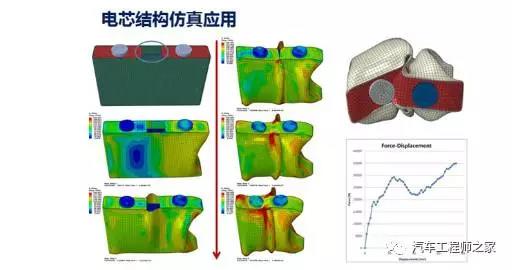
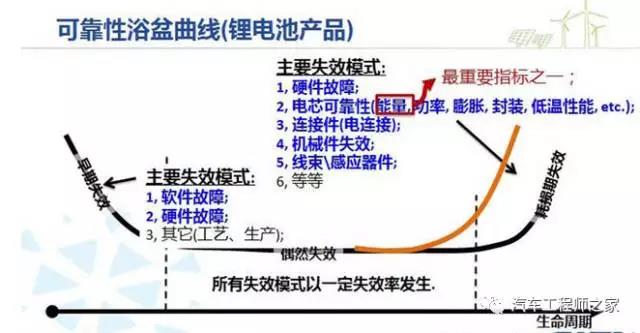
第一张图反应的是电芯受力的情况,模拟包括振动,冲击,挤压等多种工况,其实模拟的就是电芯壳体和盖板在机械应力累加时的失效情况,从而确定结构件的设计尺寸,厚度及具体焊接的强度等,而第二张图亦反应了对于电芯可靠性膨胀,封装,机械件的失效的情况,这些显然也是与结构件息息相关的,在中国专利网上搜索CATL关于电池结构方面的设计,简单搜索以下,已达数十项之多,且不说这些专利的实际应用情况,但有一点确定的是电池系统内的结构安全的设计已完全融入到整个电池系统的安全设计考量中,并扮演了重要角色;
实际电池生产企业中,针对电池盖板的设计,焊接的工艺,模块与模块间的连接,底板对模块的支撑,以及一些焊接一体化的设计,导致了目前电池结构件迁一发则动全身的情况,要对一处结构进行更改,则可能需要对整套系统进行更改,从而对安全性设计重新进行评价;同样类似绝缘密封件的搭配,亦以在早期就融入进电池的热管理系统设计中,可以说与电池的结构功能件一起共同构成了电池系统的安全性屏障。所以要对其中的一个零件进行改动或者替换需要对整套系统重新进行验证,而功能件的供应商与下游电池厂在研发过程中的捆绑,无形之中为这部分功能零件形成了极高的壁垒。
第二较长研发和验证周期造成的替代难度;
在整车厂或零配件厂商呆过的读者可能深有体会,对整车供应商的评审是一个漫长的过程,随着整车的开发,经历各个阶段不同深度广度的考核,DV,PV的验证,而最终能够SOP上车才皆大欢喜。而对于这种绝缘隔热材料和结构功能件的供应商,往往又是跟耐久相关的试验所考察的重点,一般做完耐久试验或者碰撞试验的车,都会要求做DRBTR(Design Review by Test Result),其中就需要对密封接口,机械结构件,壳体腐蚀,连接扭矩等情况进行非常细致的检查,试想如果不是供应商出现了极大的质量,谁愿意重新做这一轮验证呢?
第三材料本身的加工工艺与一致品质保证。
我认为第三个壁垒才是技术本身的,但这个技术本身的壁垒目前来看,相较于前面两个反倒成了略低的壁垒,主要涉及三个方面:功能件供应商对其上游材料例如金属,橡胶材料本身的品质把控能力,涉及到一些对特殊原料供应商的把控;配合电池厂商的设计研发能力,涉及到一些结构设计的经验,和材料的精密度的定制化服务;以及生产这些功能件的工艺能力,包括对设备的驾驭和工艺良率的提升及产品的一致性保证。
综上所述,我认为目前来看功能件的壁垒仍是非常高的,但这“个高壁垒”之所以打引号,并不是因为其功能件本身的制造工艺或者生产原料所带来的,而是在于长期的上下游研发捆绑在一起的系统设计+较长的替代周期+再加上本身材料加工的技术所综合造成的“高壁垒”。
动力电池功能辅件的市场规模
查询了三处不同的数据来源:
·来自申万宏源近期的研报显示:“不同外形的电池对于配件的需求不同,平均的成本占比约为 12%。”
·来自中国产业信息网发布的《2015-2020年中国汽车动力电池市场运营态势与投资前景分析报告》指出:电动汽车用电池结构件单车价值量约为1500元
·来自某研报:“取锂电池成组价格5.5%为锂电池结构件价值量,是可供参考的。2016年动力类方形+圆柱电池出货量25.4GWh,成组单价2.2元/wh计算,则2016年中国动力电池结构件市场规模约为25.4×22×5.5%=30.7亿元。“
以上数据的不同可能来自于对结构件种类定义和统计时间的不同,长江证券的测算主要基于动力电池的出货量,成组价格2.2元/wh,应属于较乐观估计;中国产业信息网的数据时间较早,考虑到现在纯电动和大巴车比例增加的情况,单车电池包容量增大,单车结构件平均价格可能上升;若按照申万12%测算,我们进行一个保守估算,按新能源汽车的实际销量进行计算,假设30度电每个包,1500一度电,那么16年按50万辆测算,市场规模也达到了27亿;而今年四月随着补贴的出台,新能源汽车销量又回到了高增长走势,电池出货量也将随之增加,今年电池配件的规模预计还会大幅增长;
以上统计可能无法准确反应行业市场规模的情况,我们不妨查询了一下行业龙头的情况,目前做电池功能件的主要公司包括科达利,九九华立、方林科技、以及热绝缘辅件的包括宝优际,诚懋化学等,我们挑选给行业龙头CATL供货的科达利和宝优际来分析:
科达利:主营业务主要为动力电池结构件,汽车结构件,以下为其官网展示的其主要产品,应该主要为电芯的壳体和盖板:
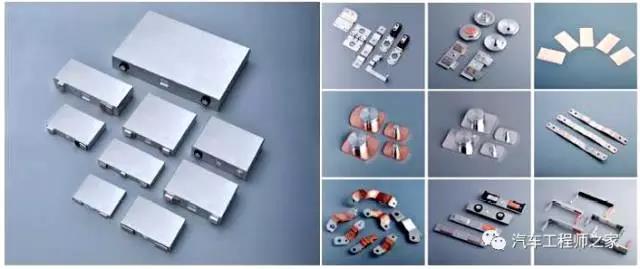
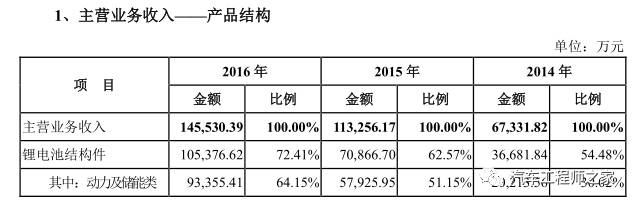
从科达利的招股说明书中可以看到,今年来科达利动力电池结构件占比逐年上升,2016年仅动力及储能类电池辅件已达到了9亿的销售规模。
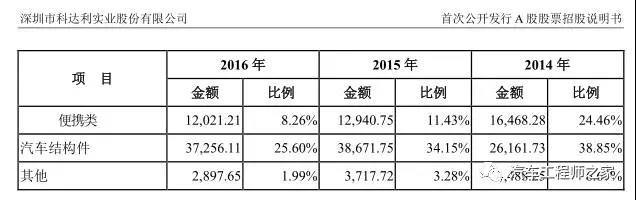
而另一家宝优际,申万宏源研究报告显示,作为CATL绝缘隔热类主要材料供应商,其功能辅件占营收比例亦大幅上升,2016年营业收入为6604.00万元,较上年同期增长28.83%;归属于挂牌公司股东的净利润为1545.55万元,较上年同期增长180.75%。而今年仍将持续大幅增长。
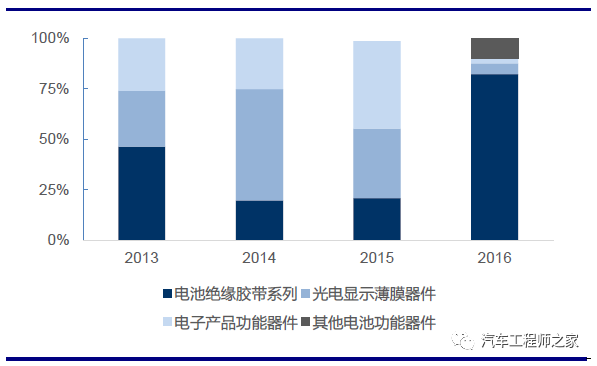
从中我们不难看出一个新兴行业的爆发,不但是一个近千亿估值龙头的诞生,连其上游的每一个细分的辅件供应商均带来了高速的增长。
动力电池功能辅件的发展趋势
1.技术高壁垒辅件的国产替代化;
最后我们来一起讨论下动力电池功能辅件的发展趋势,首先一个行业诞生之初往往都伴随着较高的技术壁垒,而随着技术的成熟,壁垒低的产品逐渐会出现越来越多的参与者,这个行业也是,锂电行业几年前四大主材的国产化率与现在不可同时日而语,而功能辅件上,目前来看例如结构件,绝缘散热件,密封件等国内厂商早已有成熟方案,而随着技术的进步,例如铝塑膜,高压继电器,超薄水冷板等壁垒较高的辅件也将逐渐形成国产替代的趋势,而这些零件即使在小,随着动力电池行业本身规模的放大,都将出现不小的市场;
2.新材料轻量化与功能性辅件多样化;
随着对电池能量密度2020年300Wh/kg的要求,应对策略一方面是电芯材料活性的提升,另一方面则显然只能是电池系统内主要结构件材料的减重。结构件的减重又将侧重于新金属材料体系的应用以及同等材料体系精确用料计算的同时维持必须的刚度和强度,这其实也对结构件厂商提出了跟高的技术要求;同时对于绝缘隔热密封等功能性设计,亦会诞生越来越多的方案,以密封为例:目前市场上就有橡胶密封圈,密封剂,海绵胶带等多种密封方案,各有利弊,而未来来看电池的隔热绝缘等功能辅件也势必会和电池包的冷却系统共同配合,而不同厂商冷却方案的不同,势必造成这个产业的定制化与多样化方向发展,其实这也更考验了功能件厂商的设计能力与工艺实现能力;
3.高毛利或将继续维持;
目前来看相较于电池的四大主材(正极、负极、隔膜、电解液),一些功能辅件的价格所占电池整体成本的比例较低,成本并不敏感,例如电池包的密封圈,承担了关键的电池整个系统能否达到IP67甚至IP68的密封作用,取个典型价格约为150元,仅占一套乘用车电池系统成本的约0.5%以下;又例如高压继电器目前一个约500元,未来国产化替代价格还会下降,按一套系统3个(正,负,charger)高压继电器算,亦只占2-3%,而除了这些之外例如金属结构件和绝缘隔热件主要为对金属和橡胶等制品的粗加工,原料成本可控,而本身所占的价格比例低,预计在未来几年内毛利或能继续维持在30-40%左右水平。
最后想说的是,随着新能源汽车整体蛋糕的做大,产业链上再小的环节都能形成一块“金矿”,而随着技术的成熟,更多的高壁垒产品将会进行国产替代,3至5年后当似乎难寻这些替代的机会时,整体的新能源车保有量又会催生大量的后市场的机会,包括新能源汽车保养与维修,动力电池的回收,新能源二手车的交易评估等等。只能说我们很庆幸,生在了这个见证行业重大变革的时代。
动力电池
特点
高能量和高功率;
高能量密度;
高倍率部分荷电状态下(HRPSOC)的循环使用;
工作温度范围宽(一30 ~65℃);
使用寿命长,要求5—10 年;
安全可靠。
应用
汽车和摩托车行业。主要是为发动机的起动点火和车载电子设备的使用提供电能;
工业电力系统。用于输变电站、为动力机组提供合闸电流,为公共设施提供备用电源以及通讯用电源;
电动汽车和电动自行车行业。取代汽油和柴油,作为电动汽车或电动自行车的行驶动力电源。
锂动力电池
锂铁电池是2000年后由美国永备公司所推出来并得到成功市场化的新型绿色高能化学电源,在应用于需要的高能量高功率电源的电子设备和电动玩具方面,显示了非常优越的性能.在中等放电电流以上时,锂铁电池的放电时间可达碱锰电池的6倍左右;而与镍氢电池相比,其放电电压平台,储存时间具有显著优势。
总的来说,锂铁电池具有以下突出优点:
1、与碱锰电池的可互换性,在任何用途上都可以和碱性锌锰电池相互换;
2、具有更长的工作时间和更高更平的工作电压,尤其是在中等电流以上放电;
3、环保绿色电源,不使用任何汞、铬、铅等有毒物质;
4、储存性能好,放置期可以长达10年。
电池型号:LFB14505(AA)
放电容量:大于2700mAh(在1000mA放电电流下)
放电电压:~1.45V(在200mA的放电电流下)
储存寿命:10年
镍氢充电电池
由于镍镉电池(Ni-Cd)中的镉有毒,使废电池处理复杂,环境受到污染,因此它将逐渐被用储氢合金做成的镍氢充电电池(Ni-MH)所替代。从电池电量来讲,相同大小的镍氢充电电池电量比镍镉电池高约1.5~2倍,且无镉的污染,现已经广泛地用于移动通讯、笔记本计算机等各种小型便携式的电子设备。 镍氢电池是有氢离子和金属镍合成,电量储备比镍镉电池多30%,比镍镉电池更轻,使用寿命也更长,并且对环境无污染。 目前,更大容量的镍氢电池已经开始用于汽油/电动混合动力汽车上,利用镍氢电池可快速充放电过程,当汽车高速行驶时,发电机所发的电可储存在车载的镍氢电池中,当车低速行驶时,通常会比高速行驶状态消耗大量的汽油,因此为了节省汽油,此时可以利用车载的镍氢电池驱动电动机来代替内燃机工作,这样既保证了汽车正常行驶,又节省了大量的汽油。[2]
分类
铅酸蓄电池
镍镉蓄电池
镍氢蓄电池
铁镍蓄电池
钠氯化镍蓄电池
银锌蓄电池
钠硫蓄电池
锂蓄电池
空气蓄电池(锌空气蓄电池、铝空气电池)
燃料蓄电池 燃料电池是一种将化学能直接转化为电能的装置,他的正极是氧电极,负极是氢或碳氢化合物或乙醇等燃料电极。催化剂在正极催化氧的还原反应,从外电路向氧电极反应部位传导电子;在负极催化燃料的氧化反应,从反应部位向外电路传导电子;电解液输送燃料电极和氧电极反应产生的离子,并且阻止电子的传递。电子通过外电路作功,并形成电的回路。只要燃料和氧不断地从装置外部供给电池,就有放电产物不断地从装置向外排出(氢氧燃料电池)。
太阳能蓄电池
超容量电容器
飞轮电池
钠硫电池。钠硫电池的理论比容量可达760 W?h/kg,实际已达到300 W?h/kg,且充电持续里程长,循环寿命长。
负极的反应物质是熔融的钠在负极腔内,正极的反应物质是熔融的硫在正极腔内。正极和负极之间用α―Al2O3电绝缘体密封。正极腔和负极腔之间有β―NaAl11O17陶瓷管电解质。电解质只能自由传导离子,而对电子是绝缘体。当外电路接通时,负极不断产生钠离子并放出电子,电子通过外电路移向正极,而钠离子通过β―NaAl11O17电解质和正极的反应物质生成钠的硫化物。
推广瓶颈
新能源汽车
新能源汽车因其节能和环保的特性被看好,但是其产业化面临最大问题是居高不下的销售价格。从国外混合动力汽车看,同类型的混合动力和燃油型丰田凯美瑞差价达到8-10万元,而国内比亚迪纯电动车型E6与同类型的燃油车的差价更是高达20多万。虽然新能源汽车后期的运营和维护成本低廉可以逐步填平一次购置的差价,但是高额购置价格无疑成为阻碍新能源汽车产业化的重要障碍。
新能源汽车价格之高源于动力锂电池
新能源汽车主要由电池驱动系统、电机系统和电控系统及组装等部分组成。其中电机、电控及组装和传统汽车基本相同,差价的原因在于电池驱动系统。从新能源汽车的成本构成看,电池驱动系统占据了新能源汽车成本的30-45%,而动力锂电池又占据电池驱动系统约75-85%的成本构成。
解决新能源汽车高价格的核心是降低动力锂电池一次采购成本。目前市场上已经商业化的动力锂电池主要包括磷酸铁锂电池、锰酸锂电池和三元材料电池等,中国市场以磷酸铁锂为主,日韩大多选择锰酸锂和三元材料的混合电池体系。赛迪经智统计数据显示目前国内的磷酸铁锂电池售价约在3-4元/Wh,锰酸锂和三元材料电池约在4-5元/Wh。考虑不同类型新能源汽车的电池容量,插电式混合动力汽车的电池容量是10-16KWh,纯电动汽车的电池容量24-60KWh,纯电动大巴的电池容量一般是200-400Kwh,对应电池售价在3-5万元、7-18万元和60-120万元水平,如此高昂的电池价格是新能源汽车价格居高不下的主要原因。
电池成本降低之路:规模化和回收资源化先行
降低电池成本,一直都是产业内重要的解决方向。除了电池体系改善和使用寿命提升带来成本降低外,当前主要的降成本方案是规模化和回收资源化。以全球新能源汽车最为成功的企业特斯拉来看,其使用18650圆柱电池(电池型号:直径18mm,长度65mm)因规模扩大从2007年到2012年成本约下降了40%左右。未来随着新能源汽车的普及动力电池的规模化生产,电池成本会进一步降低到2元/Wh以下,从而达到《节能与新能源汽车产业发展规划(2012-2020年)》中2015年的规划目标。
在资源化利用上,动力锂电池目前还存在回收体系不完善,回收价值偏弱的问题。虽然国内目前也涌现出了像格林美和湖南邦普等大型回收企业,但是动力锂电池回收存在回收成本高、回收产业链不完善的问题。动力锂电池的回收资源化需要充分借鉴铅酸电池回收利用的经验。铅酸电池建立了完备的回收网点和回收产业链,一般铅酸电池在回收时具备30%的回收价值。
动力锂电池再利用:电池成本降低的新路径
动力锂电池再利用是指介于新能源汽车和动力锂电池资源化的中间环节,通过对汽车使用后的动力电池进行拆解、检测和分类后的二次使用,实现动力电池梯级,从而实现动力电池30-60%的成本降低目的。一般来说,新能源汽车对动力锂电池报废的标准是电池容量低于80%,如果剩余容量还在70-80%电池直接进行资源化回收是极大的浪费,做好动力锂电池再利用对电池成本的降低尤为重要。
国家政策支持动力锂电池在利用的产业化探索。2012年7月出台的《节能与新能源汽车产业发展规划(2012-2020年)》明确提出“制定动力电池回收利用管理办法,建立动力电池梯级利用和回收管理体系,明确各相关方的责任、权利和义务。引导动力电池生产企业加强对废旧电池的回收利用,鼓励发展专业化的电池回收利用企业。”国家从规划层面给动力电池再利用提供了方向。
新能源汽车动力锂电池再利用领域主要瞄准ICT领域、家庭以及可再生能源发电储能等领域。虽然动力锂电池再利用实践在国内还未开展,但是在日本、美国已经有多年的示范经验。日韩从新能源汽车发展伊始就开始着力动力电池再利用的研究,这些前期研究工作给我国开展电池再利用研究提供了很好的借鉴。
多方合作建立新型的动力锂电池再利用商业模式
动力锂电池再利用商业模式需要建立多方面的合作机制。首先是动力锂电池的回收需要遵循“谁制造谁回收”责任体制,通过推行回收责任制建立回收利用网络,保证再利用电池来源。再利用核心主要包括电池回收、电池评价和二次再装配利用等环节,由于再回收和新能源汽车运营中的电池运营商密切相关,建议由运营商、汽车厂和电池企业合资建立电池服务模块,承担动力锂电池的再利用业务,对再装配电池可以考虑通过电池租赁或者零售等方式应用在终端客户上。
动力锂电池再利用商业模式
动力锂电池再利用终端主要瞄准家庭储能、店铺、新能源分布式发电、防灾据点以及通讯基站应用等领域。储能领域应用对能量密度的要求不高,但是对循环寿命和价格要求相对较为苛刻,考虑电池回收、转换及运输等多重成本,车用废旧电池实际的回收价值将不到新电池成本的10%,在价格上可以满足储能的要求,但是循环寿命的验证还需要在电池设计时予以考虑,保证在储能利用环节的寿命要求。
动力锂电池再利用的基础研究是电池再利用产业发展的关键,需要政府部门整合资源推进再回收示范工程实践。由于我国新能源汽车产业链条中各自为战的态势,车企、电池企业或者运营商主动牵头从事电池再利用的研究具有较大的难度,通过政府组织示范工程推进我国动力电池再利用的标准建立和应用实践尤为重要。此外,我国从奥运会、世博会以及各地最早运营的示范项目的新能源汽车电池逐渐进入淘汰期,如何结合这些淘汰电池进行再利用应用实践也更为迫切。
动力电池再利用业务的风险所在
动力电池再利用和回收都是我国的新能源汽车产业链考虑较少的环节,而渐行渐近的新能源汽车产业化带来的巨量动力锂电池处理已经成为急迫解决的问题。据赛迪经智研究结果,预计2015年,动力锂电池累计报废量约在2-4万吨左右,到2020年前后,我国新能源汽车动力锂电池累计报废量将达到12-17万吨的规模。如此巨大的电池回收量需要提前进行动力锂电池再利用业务的研究和商业模式的摸索。
动力锂电池再利用获益空间的不确定。虽然从目前动力锂电池企业提供的电池数据显示,新能源汽车淘汰的电池还将保留70-80%的有效能量,而且在成本上具备较强的优势,但是电池在利用领域主要集中储能领域还面临诸多挑战。我国的储能电池目前还是集中在通讯基站储能和大型数据中心、银行等UPS储能,而且主流储能方式还是铅酸电池,这些领域动力锂电池再利用的替代还存在不确定性。此外针对新能源储能,还受限于国家在新能源分布式发电领域的支持力度。[1]
动力电池隔膜
在全球重点发展电动车、储能电池等新能源产业的今天,锂电池做为公认的理想储能元件,得到了更高的关注。我国也在动力电池领域投入了巨大的资金和政策支持,已经涌现了比亚迪、比克、力神、中航锂电等全球电池行业引人注目的骨干企业。正极材料、负极材料、电池隔膜、电解液是锂电池最重要的四项原材料,锂电池隔膜由于投资风险大、技术门槛高,一直未能实现国内大规模生产,成为制约我国锂电池行业发展的瓶颈,特别是在对安全性、一致性要求更高的动力锂离子电池领域,更是我国从锂电池生产大国到锂电池生产强国难以逾越的障碍。
锂电隔膜的主要生产工艺可分为干法和湿法两大类。车用动力电池容量大,安全性要求高,这也要求隔膜具有更高的强度、保液能力及安全温度。干法工艺可以采用多层复合的形式,该种隔膜具有结构安全、孔隙均匀、透气性好、耐高温性好等诸多优势,完全满足于动力锂电池的严格要求,目前国内外众多的动力电池厂商均认可该种工艺的隔膜是动力锂电池的应用方向。
目前全球锂电池产能急速扩张,做为主要材料的锂电池隔膜产能增长速度呈现滞后的局面,已经有众多的电池厂家不同程度的表示了隔膜紧缺,隔膜材料产能的提高不仅对我国锂电池乃至世界锂电池产业的发展都是一个迫切的要求。因而,在国内尽快的涌现出更多的星源材质一样的民族企业是完善我国锂电池行业产业链,提升我国锂电池生产企业竞争和可持续发展能力的重要举措,也是关乎我国新能源汽车产业快速发展的关键环节。[3]
优势
超长寿命,长寿命铅酸电池的循环寿命在300次左右,最高也就500次,而山东海霸能源集团有限公司生产的磷酸铁锂动力电池,循环寿命达到2000次以上,标准充电(5小时率)使用,可达到2000次。同质量的铅酸电池是“新半年、旧半年、维护维护又半年”,最多也就1~1.5年时间,而磷酸铁锂电池在同样条件下使用,将达到7-8年。综合考虑,性能价格比将为铅酸电池的4倍以上。[4]
使用安全,磷酸铁锂完全解决了钴酸锂和锰酸锂的安全隐患问题,钴酸锂和锰酸锂在强烈的碰撞下会产生爆炸对消费者的生命安全构成威胁,而磷酸铁锂以经过严格的安全测试即使在最恶劣的交通事故中也不会产生爆炸。
可大电流2C快速充放电,在专用充电器下,1.5C充电40分钟内即可使电池充满,起动电流可达2C,而铅酸电池现在无此性能。
耐高温,磷酸铁锂电热峰值可达350℃~500℃而锰酸锂和钴酸锂只在200℃左右。
大容量。
无记忆效应。
体积小、重量轻 。
编辑推荐
最新资讯
-
中汽中心工程院能量流测试设备上线全新专家
2025-04-03 08:46
-
上新|AutoHawk Extreme 横空出世-新一代实
2025-04-03 08:42
-
「智能座椅」东风日产N7为何敢称“百万级大
2025-04-03 08:31
-
基于加速度计补偿的俯仰角和路面坡度角估计
2025-04-03 08:30
-
《北京市自动驾驶汽车条例》正式实施 L3级
2025-04-02 20:23