中国一汽技术中心利用LMS工程技术服务及软件产品进行疲劳工程分析,显著缩短车辆开发周期,节约研发成本
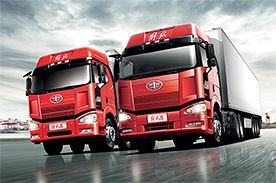
业务挑战
-优化车体结构,提升疲劳性能
-在设计早期,预测疲劳损伤敏感区域,并评估预期的疲劳寿命
-发现并解决疲劳相关问题
-通过高效的仿真方法,提前进行疲劳工程分析,从而缩短车辆开发周期
成功关键
-精确地预测道路载荷及其对零部件的影响
-采用基于道路测试数据的、完整的集成仿真解决方案
-利用试验数据,通过多体动力学虚拟仿真试验,复现试验车辆的道路载荷测试
-集成了试验测试数据,多体仿真及疲劳优化的多学科软件平台解决方案
结果
-优化部件结构,提升疲劳性能
-减少物理样机的数量和试制次数
-极大地减少了研发成本和开发周期
-比竞争对手更快地将高可靠性的汽车产品投放到市场
行业
-汽车及交通运输
客户主要业务
一汽技术中心是中国汽车行业最大的研发中心,拥有最多最全的测试检测设备。也是一汽集团和中国政府的一级汽车研发技术中心。公司一直致力于商用车、乘用车、小型货车、客车、卡车及汽车零部件的产品开发和创新。一汽技术中心拥有完整的整车开发流程。
解决方案/服务
-LMS
客户位置
长春, 吉林省
中国
"我们特别欣赏LMS完整的解决方案。通过这样高效的解决方案,在商用车设计时,驾驶室样机很容易就通过了8000公里的道路耐久测试。用同样的方法,我们还解决了一些其他设计问题。例如,我们发现并解决了一款越野车的车体前部开裂问题及悬置系统的疲劳损伤问题。"
闫 鑫
车身部
中国一汽技术中心
"在中国汽车工业的研发领域,我们是将仿真应用于疲劳寿命分析的先驱,引领了行业的发展。我们希望能一直保持领先地位。实际上,这就意味着我们需要研究更深层次的疲劳问题,如非金属材料的疲劳,优化减振器的疲劳寿命等,我们也希望能获取尽可能高的精度,因为可靠耐久性仿真能够帮助我们有效控制产品开发周期。这样也使得我们能够比竞争对手更早地将产品投放市场。"
闫 鑫
车身部
中国一汽技术中心
"LMS Virtual.Lab Durability软件有专门的焊点焊缝建模功能,能够算出疲劳损伤的敏感区域。通过专门的疲劳后处理分析,我们能够快速地识别和解决疲劳问题。"
闫 鑫
车身部
中国一汽技术中心
"扭曲路是一种很难迭代的工况,因为低频效应很显著,使得时域迭代收敛变得很困难。但是LMS Virtual.Lab Motion TWR强大的算法能够很好地处理低频迭代。得益于此,我们的模型可以考虑的很细致,甚至于包括与LMS Imagine. Lab Amesim联合仿真的空气弹簧的详细建模。"
闫 鑫
车身部
中国一汽技术中心
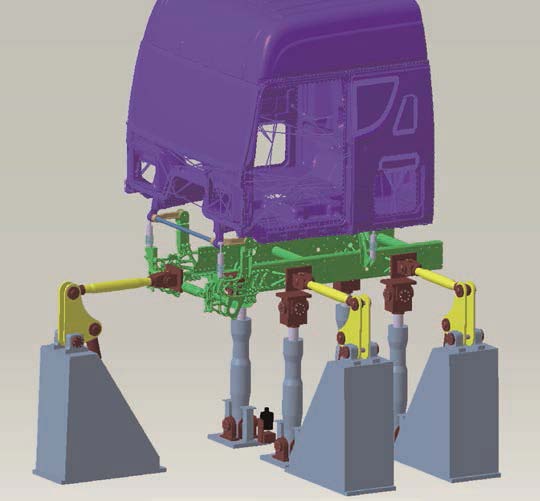
具有挑战性的时期,耐久性是衡量车辆好坏的关键因素
疲劳耐久性能极大地影响了对车辆质量的感知。它是车辆非常重要的一个卖点。客户理所当然地认为,他们买的轿车可以行驶三十万公里,或者他们的卡车可以在非常粗糙的路面环境下行驶。但是随着汽车行业的发展,车辆类型越来越多,对车辆研发工程师提出的挑战也越来越大,他们必须不断地减少车辆重量以适应燃油经济性的严苛要求,而且必须要快速地开发出可靠性好,高品质的,具有吸引力价格的汽车。所谓的“凭经验设计”将导致样车反复试验,开发周期长,成本高。因此,汽车制造厂商及其研发中心都在寻求新的疲劳工程分析技术,包括通过前期的疲劳设计仿真,在第一次样车测试就获得更好的疲劳性能。
新的疲劳工程解决方案的需求
成功预测疲劳寿命的关键是要正确定义道路载荷及理解道路载荷是如何影响车辆零部件的。计算和分析这些零部件的载荷是一个极具挑战性的任务,特别对于目前的主动悬架系统来说。在概念设计阶段,通常只有很少的测试数据,甚至于根本没有任何测试数据可用。通过这么多年的验证,多体仿真方法作为可信赖的先进技术广泛应用于精确计算道路载荷。根据模型复杂程度级别的不同及可用的测试数据,有几种不同的分析方法。
Siemens PLM Software开发了一种完全基于CAE仿真的方法,即所谓的“数字路面” 方法,以及一种测试与仿真相结合的混合路面分析方法。后者,包括LMS Virtual.Lab Motion软件在内的,称之为基于时域波形再现(TWR)技术,它起初是来源于试验室台架振动测试系统的载荷迭代测试技术。应用这个技术,中国一汽技术中心大大缩短了一款最近的商用车的开发时间。
一汽技术中心是中国汽车行业最大的研发中心,拥有最多最全的测试检测设备。一汽技术中心一直致力于商用车、乘用车、小型货车、客车、卡车及汽车零部件的产品开发和创新。一汽技术中心拥有完整的整车开发流程,从造型和结构设计,到仿真和多性能领域的试验测试,再到CAM计算机辅助制造。为了实现一种更为有效可靠的疲劳工程分析方法,技术中心的专家们决定与LMS解决方案的工程技术服务团队合作。从而建立了完整的软件集成解决方案。
“我们有一些零部件的疲劳开裂问题,比如车体前围,车身的拐角或一些局部区域的关键部件的疲劳断裂。”一汽技术中心车身部从事商用卡车车身研究的CAE工程师闫鑫说,“我们以前都是基于静强度分析,然后凭借我们的经验来评估驾驶室的疲劳。但是用这种方法,我们在样车测试阶段经常遇到疲劳开裂问题。这就意味着我们不得不反复地进行结构修改,导致开发周期延长。得益于与Siemens PLM Software的合作,我们研究了疲劳开裂的问题所在,利用这个仿真开发流程,我们可以精确得到道路载荷,针对疲劳性能进行结构优化设计。这样我们利用LMS解决方案研发的某款商用卡车驾驶室试制样车一次性地通过了疲劳性耐久试验。”
精确预测车辆部件的道路载荷
基于TWR时域波形再现技术,使得工程师可以方便地应用各种道路试验测试数据进行仿真迭代,从而预测道路载荷。这种方法利用非约束车身的多体模型,以试验测试数据作为边界条件,能够复现试验车辆的道路测试载荷,通过迭代控制算法反算得到等效的路面激励信号。通过计算轮心的等效激励信号,LMS Virtual.Lab Motion避免了一些复杂单元的建模,比如复杂轮胎模型,数字路面模型和驾驶员模型等,这些都需要耗费大量的时间进行建模。虚拟仿真等同于一个疲劳测试台架的试验。LMS Virtual.Lab Motion拥有强大的,高效精确的求解器。能够处理复杂模型如柔性体,也能通过与LMS Imagine.Lab Amesim软件实现联合仿真,从而处理如主动悬架控制系统的仿真。通过LMS Virtual.Lab Motion计算得到各个零部件的载荷,再输出到LMS Virtual.Lab Durability中进行疲劳仿真分析。
“这个全新的分析流程始于和LMS工程服务技术专家的合作”,闫鑫说。“我们做了道路测试并采集了试验数据。大量的试验数据通过LMS Tecware软件的处理,将处理后的数据用于仿真。” LMS Tecware这个软件包可以帮助工程师高效地验证和理解数以千兆的原始测试数据。试验数据将通过各种处理,比如删除异常数据,滤波处理,经数学处理方式得到新通道数据,等等。通过处理后的数据将应用于仿真分析。LMS Tecware允许减去与疲劳无关的特定数据,提供数据处理方法帮助高效地量化潜在的疲劳载荷数据。这些数据都可以导入到LMS Virtual. Lab Motion中。
下一步,工程师建立了商用车的多体模型,包括驾驶室和悬置系统。“LMS Virtual.Lab Motion用户界面非常好”,闫鑫说,“而且,我们获得了Siemens PLM Software技术支持团队很好的培训和帮助。在他们的帮助下,我们能够很容易地建立多体模型,计算激励信号,从而进一步计算部件疲劳载荷。”一汽技术中心的工程师们对 LMS Virtual.Lab Motion TWR强大的功能印象深刻。“扭曲路是一种很难迭代的工况,因为低频效应很显著,使得时域迭代收敛变得很困难。”闫鑫说,“但是LMS Virtual.Lab Motion TWR强大的算法能够很好地处理低频迭代。得益于此,我们的模型可以考虑的很细致,甚至于包括与LMS Imagine.Lab Amesim联合仿真的空气弹簧的详细建模。”
优化部件结构,以提升疲劳性能
将计算得到的部件载荷结合材料曲线,周期疲劳参数和基于有限元(FEA)分析的应力结果,LMS Virtual.Lab Durability能够精确判定关键的疲劳危险区域,评估预期的疲劳寿命。
“LMS Virtual.Lab Durability软件有专门的焊点焊缝建模功能,能够算出疲劳损伤的敏感区域,”闫鑫说,“通过专门的疲劳后处理分析,我们能够快速地识别和解决疲劳问题。”整个过程可以是参数化的,通过设计不同的试验方案进行结构优化设计。闫鑫解释道,“我们特别欣赏完整的LMS解决方案。通过这样高效的解决方案,在某款商用车设计时,驾驶室样机很容易就通过了8000公里的道路耐久测试。用同样的方法,我们还解决了一些其他设计问题,例如发现了一款越野车的车体前部开裂及悬置系统的疲劳损伤问题。”
一个额外的,也是很关键的基于TWR的疲劳工程分析的好处是,通过LMS Virtual.Lab Motion TWR反算得到的等效激励信号可以用于其它相似车型的开发。因为等效激励载荷信号可以认为是不变的。这在新车型开发的早期是很有用的。因为在设计早期,没有物理样机,也不可能做物理样机的试验测试。这样就可以在设计开发早期阶段提前进行疲劳工程分析。
“这也是我们急需要彻底打破以前的流程,从而将此流程作为我们公司的新的标准流程的原因。”闫鑫说,“基于此,我们希望建立通用的载荷谱分析流程。作为所有疲劳分析领域的研发流程,这必将大大减少我们将来在数据获取上所花费的时间。”
进一步应用这个屡获殊荣的技术
一汽技术中心工程师计划进一步部署基于仿真的疲劳分析流程,从而提升更大的能力。“在中国汽车工业研发领域,我们是将仿真应用于疲劳寿命分析的先驱,我们希望能一直保持领先地位,”闫鑫说。“实际上,这就意味着我们需要研究更深层次的疲劳问题,如非金属材料的疲劳,优化减振器的疲劳寿命。我们希望能获取尽可能高的精度,因为可靠耐久性仿真能够帮助我们有效控制产品开发周期。这样也使得我们能够比竞争对手更早地将产品投放市场。”
成功的项目已经证实如上所说是对的。“得于Siemens PLM Software旗下的LMS解决方案,我们的商用卡车研发节约了2千万元人民币的研发成本费用。”闫鑫说。他总结道,“这项新的疲劳工程分析流程给我们带来了两个奖项。我们获得了中国汽车工业科学技术奖二等奖和一汽集团科技创新一等奖。”
最新资讯
-
大卓智能端到端直播实测,16公里复杂路段挑
2025-04-25 17:16
-
《汽车轮胎耐撞击性能试验方法-车辆法》等
2025-04-25 11:45
-
“真实”而精确的能量流测试:电动汽车能效
2025-04-25 11:44
-
GRAS助力中国高校科研升级
2025-04-25 10:25
-
梅赛德斯-AMG使用VI-CarRealTime开发其控制
2025-04-25 10:21