汽车碰撞安全与轻量化研发中的若干挑战性课题
周青1,夏勇1,聂冰冰1,黄毅2,赖兴华2
1. 清华大学汽车安全与节能国家重点实验室,北京,100084,zhouqing@tsinghua.edu.cn
2. 清华大学苏州汽车研究院(相城),苏州,215200
摘 要:汽车结构与动力电池的碰撞安全性是开发轻量化、电动化汽车的强制性要求和关键的基础性支撑技术。面向汽车轻量化、电动化和智能化的研发需求,本文通过若干典型课题,介绍并论述汽车碰撞安全性研发的技术挑战。主要内容包括:采用夹层式汽车前舱罩盖技术满足汽车吸能位移限定下的行人头部碰撞响应控制;面向复杂道路交通事故工况和多样化人体特征,解决强非线性条件下的自适应智能乘员保护系统优化设计难题;研究车用动力电池碰撞下的内短路失效机理,并建立能准确预测电池变形响应的数值模型及碰撞安全评估方法;解决材料冲击测试中动态力测量信号的振荡问题,建立复杂应力和冲击载荷下轻质高强材料及复合连接接头的大变形失效断裂预报方法及仿真模型。
关键词:汽车安全;汽车轻量化;动力电池碰撞安全;行人碰撞安全;智能乘员碰撞保护
1 引言
以轻量化和电动化为主导的汽车工业产业升级是实现《中国制造2025》目标的重要内容。汽车的小型化、轻量化、电动化和智能化给汽车碰撞安全性设计提出了更大的技术挑战。在汽车轻量化和电动化技术升级与应用中,与汽车碰撞事故中人员、电池及结构碰撞安全保护相关的主要技术瓶颈体现在:
(1) 轻量化和小型化要求导致汽车碰撞刚度提高,缺乏道路事故工况和严苛碰撞波形下对行人及乘员提供有效保护的技术以及安全评测工具和设计方法,无法有效解决低成本车辆和小型车辆在碰撞吸能位移不足与降低乘员和行人伤亡风险之间的设计冲突;
(2) 车用动力电池在在碰撞冲击下变形破坏和内短路失效机理不明确,难以准确预测碰撞下动力电池的损伤和热失控风险,使得电池针对碰撞载荷的保护经常处于“过保护”或“保护不足”的状态,不利于实现车辆轻量化;
(3) 缺乏对轻质高强材料和连接接头在碰撞载荷下的大变形断裂失效的力学性能表征和仿真技术,缺乏基于异种材料和复合连接的结构设计方法和断裂控制技术,无法保障复杂工况下轻量化车身和动力电池碰撞保护设计的质量和效率。
由于存在上述诸多技术瓶颈,安全系统开发由工程经验主导,缺乏科学的正向设计方法和基础数据,导致人员安全、车用动力电池保护、车身结构存在大量不合理的冗余设计或欠设计,产品开发周期长、车辆设计和制造成本高。
基于本研究团队在过去十多年中的研究成果,本文通过八个研究课题及结果,论述汽车碰撞安全性研发中的若干技术挑战。这些研究课题的主体是汽车结构与动力电池系统的碰撞安全性设计,难题来源于工程实际,基础是冲击力学理论,研究手段是材料和结构的冲击力学试验以及计算仿真分析,它们之间的学术关联性如图1所示,基于轻量化材料的冲击失效研究,通过试验获得足够准确的材料和连接接头的力学性能数据,进行性能分析,进而建立高精度的计算仿真模型,对其在冲击载荷下的变形与失效行为进行准确预测,并应用于汽车结构的设计。一方面,为人员碰撞保护技术研究提供轻量化结构优化和非金属吸能材料力学性能表征等方面的基础,形成了面向汽车碰撞载荷的人体安全评测体系和碰撞安全保护设计与开发技术;另一方面,为车用动力电池的碰撞安全研究和防护提供了材料力学和冲击试验技术等方面的基础,形成了轻量化结构设计与车用动力电池保护技术体系。
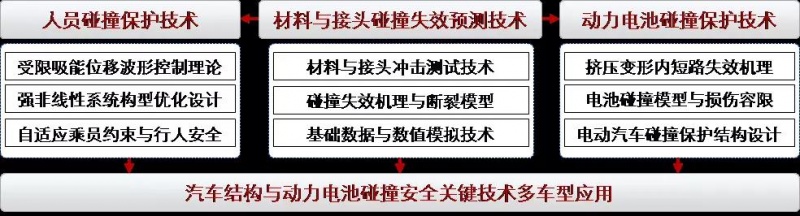
图1 汽车结构与动力电池碰撞安全关键技术的学术关联性
本文所介绍的成果多是基于本研究团队的国际合作课题和国家纵向课题产生,并结合国内汽车企业的研发需求,通过校企合作对相关方法和技术进行吸收转化,进一步研制出了具有自主知识产权的产业化应用技术,并在多款自主品牌的量产车型中得到应用,实现了国际开放合作创新基础上的自主应用。
2 汽车碰撞安全与轻量化研发中的八个挑战性课题
2.1 满足行人头部碰撞保护要求的夹层式汽车前舱罩盖技术
传统的汽车前舱罩盖结构变形强度分布不均匀、碰撞吸能效率低下,导致行人头部碰撞时伤害严重。为解决该难题,我们发明了面向行人头部碰撞安全保护的均匀构型夹层汽车前舱罩盖技术(图2)[1-6]。沿行人头部冲击方向,通过初始碰撞的惯性力和罩盖随动质量分布的设计控制初始碰撞峰,之后碰撞抗力迅速下降;随着冲击位移的增大,罩盖膜力效应开始起作用,碰撞抗力再次上升;当罩盖下方的吸能位移用尽以后,以罩盖夹层的局部压溃来控制碰撞尾峰,吸收残余动能[2]。按照行人头部碰撞响应过程主导因素的不同划分碰撞波形阶段与前舱罩盖特征区域,在罩盖的面内方向,通过夹层结构形式和厚度分布补偿因边界约束等造成的罩盖变形刚度的分布不均,实现了罩盖碰撞响应全局最优,将行人头碰撞保护所需的罩盖下方位移降低了20%。以此为基础,形成了行人头模块碰撞波形控制理论以及相应的夹层罩盖设计方法,同时突破了罩盖变形强度不均和下方吸能位移受限两个难点。
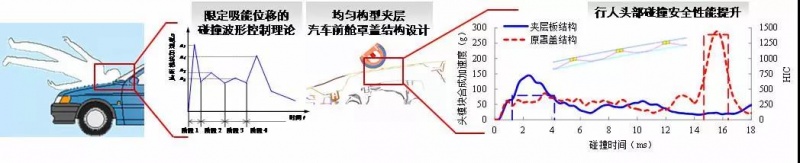
图2 面向行人头部碰撞安全的碰撞波形控制方法与均匀构型的前舱夹层罩盖技术
2.2 满足复杂工况的乘员碰撞响应控制技术
由于小型车和轻量化车的碰撞波形相比普通轿车更为复杂和严苛,车辆前部结构吸能位移和乘员舱内的生存空间有限,使得在强冲击载荷作用下,很难在被保护对象上施加均匀载荷,导致人员承受的载荷在时间和空间上呈现很强的非均匀分布特性,能量吸收空间利用率低下,损伤超标。针对乘员整体碰撞响应姿态控制的难题,我们建立了基于膝部挡板、座椅姿态和刚度调节的乘员碰撞响应姿态控制方法(图3a),其核心是利用碰撞初始的高惯性力来平衡碰撞后期的吸能位移,充分利用外载荷冲击在时间历程和空间分布的特点来控制人体碰撞响应姿态,通过控制乘员躯干和下肢约束力的作用时间及强度来控制乘员的碰撞响应姿态,使其在碰撞历程中经历更为均衡的约束力,优化安全系统的变形模式和响应次序,提高能量吸收效率,实现损伤敏感部位冲击力的降低,从而最小化乘员损伤风险[7-9]。
在此基础上,通过对乘员约束构型谱的研究,进一步得到了自适应乘员约束系统的关键影响参数和损伤输出之间的关系,实现了乘员约束载荷针对乘员身材和碰撞强度可调(图3b),可进一步使系统成为主动、被动一体化的自适应乘员约束系统,对复杂碰撞工况和中国人体特征提供有针对性的碰撞保护,为未来智能汽车环境下具有多种朝向和姿态的乘员碰撞保护提供了先期研究结果。
我们提出的滑动吸能座椅技术(图3c)与后倾乘员的姿态控制和碰撞保护技术,不仅能有效降低尾撞工况下颈部挥鞭伤的风险,还可与气囊及安全带协同作用,有效控制乘员的整体运动姿态,避免乘员发生下潜运动,并在主动、被动一体化技术层面利用主动座椅控制和碰撞动能快速调整后倾乘员姿态[10-17]。
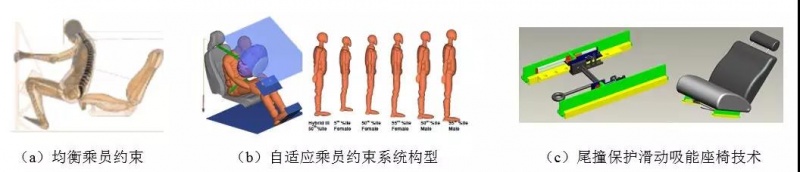
图3 乘员碰撞响应姿态控制技术和装置
2.3 适应多方向碰撞响应的碰撞假人技术
作为汽车碰撞安全性的人员损伤评价装置,国际上现有的碰撞假人仅能适应单一工况,分为正面碰撞假人和侧面碰撞假人。而实际道路交通事故中人体所经受的载荷多为斜向碰撞,这不仅因为实际事故工况复杂,也因为座椅安全带对人体的加载本身就是非对称的。为实现多工况下对人员损伤的准确评估,研发了具有高生物逼真度的多方向碰撞假人柔性胸部结构(图4a),可以同时满足正面碰撞、侧面碰撞和斜向碰撞的响应要求,其离散式构型的设计还可满足安全带对胸部的局部侵入变形的响应[18];我们还研发了行人四自由度膝关节下肢模块(图4b),不仅在多个碰撞方向上能更好的再现实际人车碰撞中的复杂工况,还可更加真实的表征行人下肢模块与保险杠变形交互作用时的运动学响应[19-20],为今后建立基于复杂工况、中国道路交通事故特性和中国人群体型特征的汽车碰撞安全评价方法、标准和法规奠定了基础。
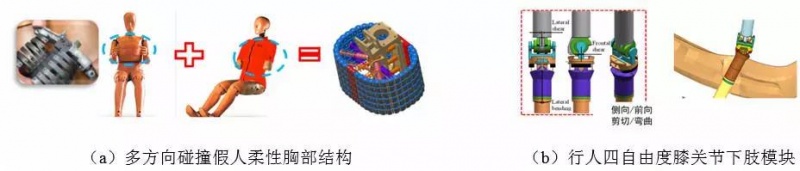
图4 适应多方向碰撞的假人结构
2.4 车用动力电池碰撞挤压工况下的变形失效机理与损伤容限
电芯受到局部挤压导致短路失效是电动汽车碰撞事故中危险性比较高的典型工况。基于大量试验观测,对挤压工况下软包电芯、方形硬壳电芯等不同类型电芯的内部损伤积累进行了细致分析,发现了宏观力学响应变化特征、断裂模式与局部损伤演化的高度一致性[21-22]。对不同类型电芯实施球头挤压试验,对试验获得的挤压力-位移响应进行分析总结,发现了宏观力学响应曲线斜率拐点对应着内部损伤特征演化的起始时刻。利用扫描电镜观测解剖后的变形电芯样品,对不同载荷水平下的电芯内部形貌加以分析,揭示了电芯挤压变形过程中的内部损伤特征,包括电极活性涂层颗粒的压裂和滑移、活性涂层从金属集流体上的脱落、隔膜局部压缩减薄、隔膜陶瓷涂层脱附、以及电极活性涂层与隔膜的局部粘连等,证实了电芯内部发生的材料和界面不可逆损伤累积是形成最终局部断裂和内短路的主导因素(图5),组分材料的断裂位置与损伤累积显著的区域吻合较好[23-24],宏观力学响应和电热响应特征存在良好的一致性。同时发现,不同挤压工况下电芯的局部断裂位置和断裂模式存在差异,对电热响应影响显著。基于宏微观测试和仿真联合分析,揭示了电池碰撞挤压内短路的触发机理,为开发电池碰撞响应预测模型和确定电芯变形阈值提供了必要的物理基础。
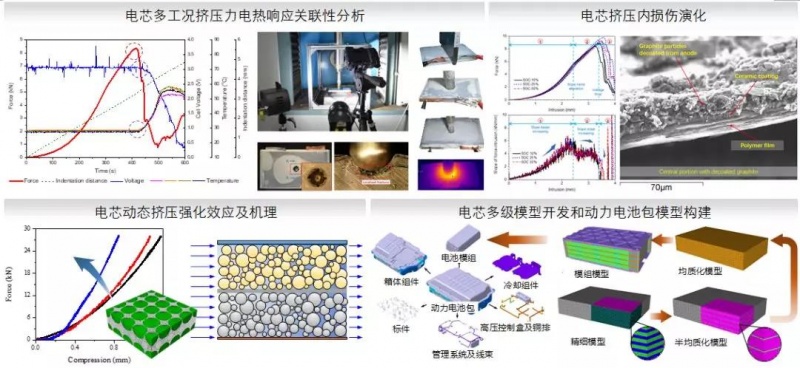
图5 车用动力电池碰撞挤压内短路失效机理与电池碰撞挤压计算模型
2.5 车用动力电池的碰撞仿真分析方法及失效预测模型
动力电池系统设计开发一直缺乏可准确预测碰撞变形和失效的电池数值模型,使得电池包结构存在技术盲区,基于工程经验和迭代试验的技术方法开发成本高,并且易导致结构过设计。
我们开展的试验研究结果表明,除了组分材料本身力学性能的影响,活性涂层与隔膜之间的界面变化显著影响挤压工况下的电芯结构刚度。通过对不同加载速率下电芯挤压变形与失效机理差异进行深入研究,揭示了电池力学响应加载速率相关性的力学机理。在落锤冲击台上搭建了电池模组冲击测试系统(图6),建立起了完整、通用的电池模组测试规程。在此基础上,对多种构型的电池模组进行了一系列不同冲头、不同冲击速度和不同冲击方向上的冲击试验,获取了多工况电池模组碰撞响应规律[25-26]。试验结果表明,动态冲击载荷下电芯的结构刚度增大,载荷峰值降低,内短路时刻对应的变形量减小,即电池在动态载荷下的安全变形阈值更低。进一步设计实施了干湿状态电芯的对比试验,并开展了解析模型与液固耦合数值模型的建模分析,结果表明,电芯中的电解液在碰撞冲击下呈现明显的动态强化效应和破裂诱导作用。
有限元仿真方法可以大幅提高汽车碰撞安全设计工作的效率,而对于电动汽车的碰撞安全性研究,现阶段还缺乏合理的动力电池仿真模型进行辅助设计。由于电池内部的多层结构特点,电池的特征尺度跨越了多个量级,如果按最小特征尺度建模的话,一个完整的电芯模型单元数量在百万量级以上,这将导致高昂的计算成本。因此在建立电芯数值模型时,在保证所需模拟精度的前提下,可以采用合适的单元类型、合理减少单元数量,以提高计算效率。基于精细化模型、半均质化模型和均质化模型的多级模型开发和参数传递策略[26-27],对电芯主体层状结构宏观力学特性进行均质化等效表征,能够有效模拟电芯和电池模组结构力学行为的拉压不对称性、各向异性和应变率相关性(图6)。通过试验观测和多级模型仿真分析,量化了局部应力应变参数与电芯内短路的关联性,建立了基于等效应变、考虑受力状态影响的电芯损伤判据,可以准确地预测多种挤压工况下的电芯局部结构失效,实现了电芯和电池模组碰撞挤压变形容限的精确估计,突破了电池包抗撞性和轻量化虚拟设计的技术瓶颈,可应用于构建电池碰撞安全仿真分析与试验评价体系。
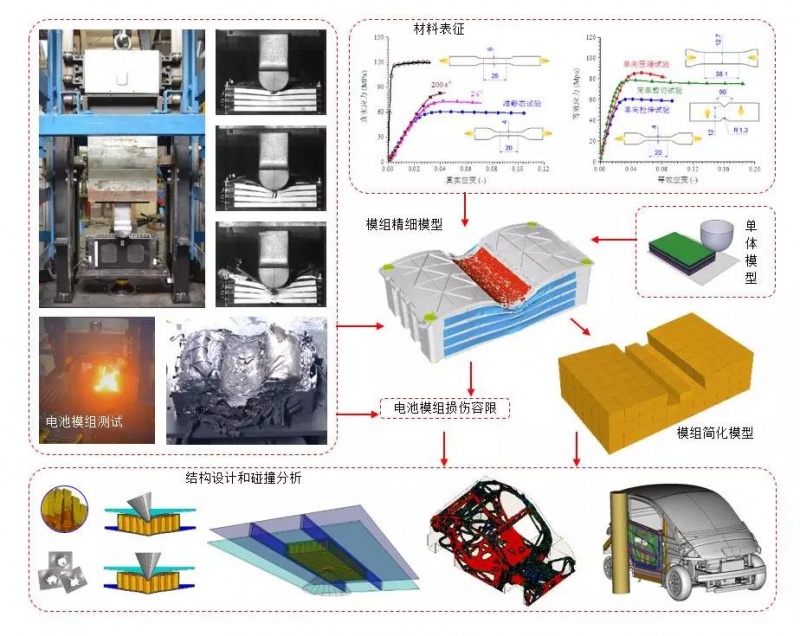
图6 电池模组碰撞安全试验评价、失效预测模型及电池包碰撞安全设计
2.6 车用动力电池的抗撞设计技术及电动汽车碰撞运动姿态控制策略
将电池均质化数值模型应用于电动汽车的碰撞仿真,针对2013年发生在美国的一起电动车底部异物碰撞引发的电池着火事故(图6),我们对该极端碰撞工况的边界条件、撞击过程中底部护板的破断模式以及局部电池的挤压变形进行了再现分析[27],对比分析了多种底部碰撞保护结构形式,提出了兼顾轻量化和底部碰撞保护性能的波纹构型填充的三明治底部护板结构[28]。在此基础上构建了电动汽车电池箱结构轻量化设计平台,提出了允许电池碰撞变形同时避免电池内短路发生的电池碰撞保护设计策略[29],并将电池碰撞响应预测技术和电池箱碰撞保护技术应用于国内自主品牌电动车的设计开发(图7)。
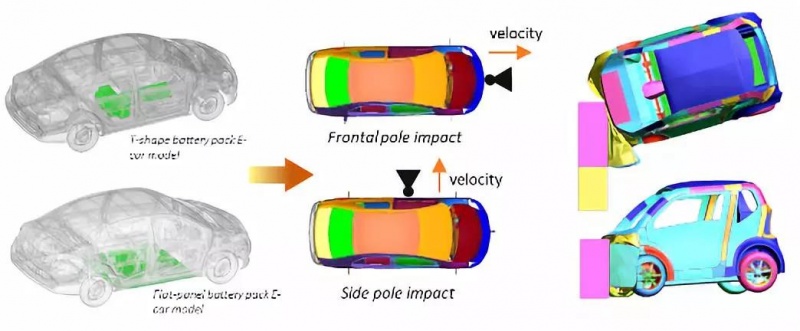
图7 电动汽车多碰撞工况分析及碰撞运动姿态控制
目前电动汽车上重量占比最大的部件是电池包,即使是电池能量利用率较高且续航里程要求较低的城市小型通勤电动汽车,电池包重量通常也达到车辆总重的三分之一左右。小型轻量化电动车对电池排布方式更为敏感,电池布置很大程度上影响着整车质心位置和转动惯量,进而影响碰撞响应(图7)。针对常见的电池布置方式、典型的碰撞工况以及不同的碰撞强度开展多工况碰撞仿真分析,研究发现,在正面全宽碰撞中,车辆重心越高,碰撞过程中俯仰运动越大,初始动能转化为重力势能越多;在偏置碰撞中,车辆重心越低,碰撞过程中俯仰运动越小,后轮与地面的接触压力越大,车辆偏转运动所需的摩擦能耗越大。通过电池包布置方式调节车辆重心,可优化控制电动车在碰撞过程中的俯仰和偏转等运动姿态,从而为碰撞安全性能优化引入新的控制因素[30],基于此建立了将单方向碰撞冲击转化为复合运动响应的碰撞运动姿态控制策略,有效提升了小型轻量化电动汽车的碰撞保护性能,解决了小型电动汽车的电池布置空间和碰撞变形吸能位移的设计冲突。
2.7 轻量化材料与连接接头的碰撞失效机理与预测技术
轻量化是汽车设计与制造中长期存在的研究课题,是汽车节能减排的重要手段之一;同时,面向新能源汽车的发展需求和车用动力电池能量密度的制约,纯电动汽车对轻量化的需求被提升到更高的优先级。
车身结构轻量化追求“正确的材料用于正确的用途”。这需要对材料的性能和材料的应用条件有全面深入的认识。对于汽车结构而言,耐撞性是最需要优先保障的性能之一。在汽车碰撞事故中,车身结构中的材料以及连接接头将经历动态冲击、塑性变形甚至失效的过程。只有全面掌握材料、连接接头在动态冲击下的力学特性,认识其变形破坏机理,并为基于CAE的虚拟设计建立准确高效的预测能力,才能设计出满足耐撞性要求的轻量化车身结构。
碰撞载荷下材料和接头断裂的预测精度不足制约了汽车碰撞安全性和轻量化设计的质量和效率,这是由于汽车碰撞事故中材料的断裂是发生在复杂应力状态下,且和应变率效应耦合。我们基于精细化的材料力学行为表征(图8),揭示了中高应变率范围内轻质合金和高强钢材料力学特性的变化规律,建立了考虑应变率和应力状态耦合影响的轻质合金塑性和断裂表征方法[31-34];提出了多级应变率下某类高强钢的统一塑性硬化主曲线理论,由此建立了该类材料的应变率相关塑性硬化特性表征方法[35];与MIT合作研究发展的MMC断裂准则预测断裂位移的精度,比常规的弹塑性材料模型的精度提高了55%以上;揭示了应变率、温度与应力状态对热塑性高分子材料屈服、流动和断裂特性的影响规律,建立了完整的热塑性高分子材料大变形和断裂力学行为表征方法[36-37];针对碳纤维三维编织复合材料,通过试验和仿真,我们研究了编织和铺层形式对碳纤维复合材料结构耐撞性能的影响[38-39]。
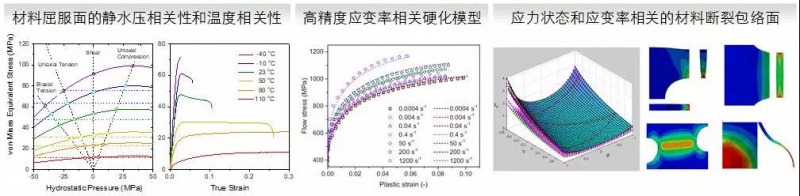
图8 轻量化材料的塑性变形和断裂行为及失效预测技术
在结构连接接头碰撞失效研究中(图9),开发了冲击韧化环氧胶粘剂的应变率相关材料模型和失效准则[40],提出了点焊接头拉拔失效的等效模拟方法[41],建立了点焊与胶接复合连接接头的高效率仿真模型[42-43],揭示了点焊和胶接连接在典型载荷作用下的互补机制,证明点焊在胶层裂纹扩展中发挥了有效的止裂作用,胶层则显著缓解了结构性能对点焊数量的依赖程度[42-43],为胶焊连接的轻量化车身设计提供了理论依据。针对点焊部件的碰撞失效,探明了随加载速率和加载模式变化的点焊接头失效模式转变规律、内在机理及其与点焊工艺条件的关联性,揭示了焊点排布对薄壁结构变形模式和吸能特性的影响规律[44]。
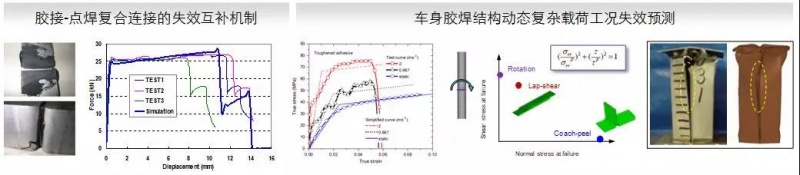
图9 轻量化车身复合连接失效机理与复杂工况失效预测
基于我们开发的轻量化材料在复杂应力状态下的大变形表征和断裂预报、基础材料数据和计算模型等理论、方法和技术[31-45],我们与汽车企业合作,针对轻量化设计、工艺和成本等要求,灵活选择材料并匹配连接方式,为实现高强钢、铝合金、复合材料、工程塑料、孔隙填充材料、点焊、胶粘、铆接等多种材料混合的轻量化结构设计材料和连接的灵活组合提供优化设计方法和仿真计算模型,使企业在车型设计开发中具备可靠的方法和数据,CAE仿真能更加准确的预测材料和接头的断裂,并依此评估对碰撞力的传递路径和碰撞吸能的影响,设计冲击载荷下结构中材料和接头失效的诱导和控制策略,实现对轻量化车身结构的大变形响应和断裂控制的最优设计(图10),在满足碰撞安全性目标下实现结构的轻量化,提高了虚拟设计的可靠性和产品研发效率。
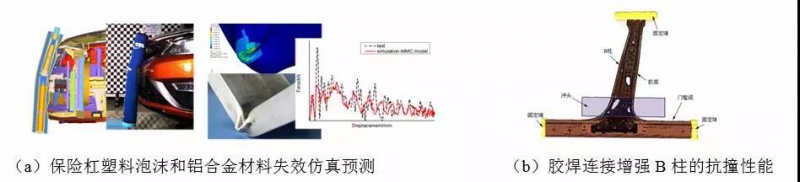
图 10 高精度材料模型在汽车轻量化结构上的开发应用
2.8 材料大变形冲击测试技术
中高应变率材料冲击试验中的载荷测量失真一直是材料冲击力学性能测试中的难题,在102 /s应变率量级的材料力学性能测试中,载荷传感器获得的冲击载荷信号耦合了传递路径的系统响应,呈现明显的振荡,难以从中提取正确的材料自身力学响应,无法满足车身结构耐撞性及轻量化的设计仿真分析需求。
针对主流冲击测试系统的核心组件载荷传递路径,通过分析中高应变率冲击力学性能测试中载荷信号振荡失真的根源(图11),我们发现,载荷信号与测试过程中的载荷输入、试样形式、夹持方式和测量装置密切相关,进而揭示了夹具和测量组件的质量、刚度和阻尼对系统振荡的影响规律,提出了通过调整载荷测量环节固有频率消除系统振荡的关键思路,将被测对象(材料试件)纳入到冲击测试力学系统中,提出了集成载荷传感器的轻型夹具工装设计方法,用于中高应变率的材料动态试验,有效消除了力测量信号中的振荡[46-48]。
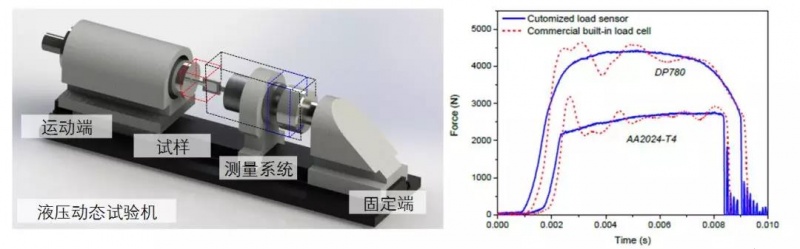
图11 有效消除材料动态试验中冲击力测量信号振荡的技术
除了测试系统参数外,被测材料的力学属性也会对动态载荷测量信号质量产生影响。对于具有明显屈服平台的材料(例如HSLA340),当目标应变率达到200s-1的时候,使用了前述的集成载荷传感器轻型夹具也不能有效抑制载荷信号振荡,这对材料硬化行为的表征带来很大困难。研究发现,引起载荷信号振荡的原因是,材料的切线模量在弹性与塑性过渡区发生较急剧的变化,从而引起测试系统的谐振。对此,我们提出了对材料进行预加载,使材料越过屈服平台,卸载之后进行动态冲击测试的试验方案。试验与仿真结果表明该方法可显著减小载荷信号振荡,提高材料在中高应变率下塑性行为表征的精度[49]。
我们建立的材料冲击下的动态力学性能表征方法以及消除中高应变率的材料动态试验中力测量信号振荡的技术,为在碰撞仿真分析中复现材料在冲击载荷下的高速率、大变形,乃至断裂、失效的行为提供了可靠的数据。
3 小结
汽车碰撞安全与轻量化研发中的技术挑战性课题以冲击力学领域为主,并与冲击损伤生物力学、材料技术、工艺技术、数字化仿真技术和结构优化设计等学科交叉,其难点主要源于工程实际问题的复杂性、汽车碰撞吸能位移限定的制约、轻量化和安全裕量两方面设计要求的冲突以及制造成本的约束等。以本研究团队在过去十多年中完成的八项研究为例,本文阐述了在行人头部碰撞保护罩盖技术、智能乘员碰撞保护技术、车用动力电池碰撞失效机理和预测技术、车身轻量化材料和连接接头的冲击大变形力学行为表征和仿真方法和冲击力测量技术等方面的研究难点,展示了材料碰撞失效机理、预测方法和模型等成果在汽车碰撞安全与轻量化设计中的应用。同时表明,以应用为导向的基础研究对汽车产品技术提升具有重要的意义。
致谢
本文介绍的研究内容和结果得益于过去十多年中本研究团队获得的多项国家纵向课题和国内外校企合作研究的资助,作者在此一并感谢所有资助方的支持及合作者的技术贡献!
参考文献
[1] Nie Bingbing, Zhou Qing, Xia Yong, Tang Jisi. Influence of Feature Lines of Vehicle Hood Styling on Headform Kinematics and Injury evaluation in Car-to-pedestrian Impact Simulations. SAE International Journal of Transportation Safety 2 (2014)182-189.
[2] 聂冰冰, 周青, 夏勇. 行人头部撞击汽车发动机罩盖的多波峰特征与结构设计. 汽车安全与节能学报,2017.3.15: 65-71.
[3] Vehicle Hood Assembly. US Patent 8991902 B2.
[4] Vehicle hood with sandwich inner structure. US Patent 7735908.
[5] Energy absorbing vehicle hood assembly with asymmetric sandwich inner structure. US Patent7690720.
[6] Vehicle hood assembly with rippled cushion support. US Patent 7635157 B2.
[7] HuangY, Zhou Q, Ji P, Nie B. Using Adaptive Shoulder Bolster and Knee Bolster to Achieve Protection Effect Comparable to Seatbelt and Airbag. SAE 2018-01-1170,SAE World Congress, Detroit, US, 2018.
[8] Ji PJ,Huang Y, Zhou Q. Mechanisms of Using Knee Bolster to Control Kinematical Motion of Occupant in Reclined Posture for Lowering Injury Risk. International Journal of Crashworthiness, 2016. DOI:10.1080/13588265.2016.1275430.
[9] Ji PJ,Zhou Q. Preliminary Study of Uniform Restraint Concept for Protection at Wider Range of Impact Severity. SAE 2016-01-1528, SAE World Congress, Detroit, US,2016.
[10] 唐亮, 刘晋浩, 程朋乐, 周青, 王青春. 乘员下潜倾向判断准则的研究. 汽车工程, 2014, 36(6): 694-698+693.
[11] 应用于尾撞滑动吸能座椅的互锁保护装置及座椅. 中国专利ZL201510455535.2.
[12] 多级控制的防下潜汽车座椅. 中国专利ZL201510064413.0.
[13] 一种尾撞自适应防挥鞭伤的滑动座椅. 中国专利ZL201310703085.5.
[14] 一种防挥鞭伤的智能型滑动座椅. 中国专利ZL201310552617.X.
[15] 一种坐垫刚度可变的汽车座椅. 中国专利ZL 201310479058.4.
[16] 一种用于追尾碰撞下自适应的智能型平动吸能座椅. 中国专利ZL201310412094.9.
[17] 用于追尾碰撞的颈部保护的平动吸能座椅. 中国专利ZL201010200843.8.
[18] 赖兴华, 徐辰, 马春生, 周青, 张金换. 具有多方向生物力学逼真特性的碰撞假人胸部集总参数建模. 清华大学学报 (自然科学版), 2014, (06): 750-755.
[19] HuangJun, Nie Bingbing, Zeng Long, Xia Yong and Zhou Qing. Development of a legform impactor with 4-DOF knee-joint for pedestrian safety assessment inomni-direction impacts. SAE 2011-01-0085, SAE World Congress, Detroit, US, 2011.
[20] 用于人体碰撞保护试验的四自由度假人膝关节机构. 中国专利ZL200610011609.4.
[21] Luo Hailing, Jiang Xuqian, Xia Yong, Zhou Qing. Fracture mode analysis of lithium-ion battery under mechanical loading. ASME International Mechanical Engineering Congress & Exposition, IMECE2015-52595, Houston, Texas, US,2015.
[22] Li Wei, Xia Yong, Zhu Juner, Luo Hailing. State-of-charge dependence of mechanical response of lithium-ion batteries: a result of internal stress. Journal of The Electrochemical Society, 165 (7) (2018) A1537-A1546.
[23] Luo Hailing, Xia Yong, Zhou Qing. Mechanical damage in a lithium-ion pouch cell under indentation loads. Journal of Power Sources 357 (2017) 61-70.
[24] Zhu Juner, Li Wei, Xia Yong, Sahraei Elham. Testing and modeling the mechanical properties of the granular materials of graphite anode. Journal of The Electrochemical Society, 165 (5) (2018) A1160-A1168.
[25] Xia Yong, Chen Guanhua, Zhou Qing, Shi Xiangnan, Shi Fangyuan. Failure behaviours of 100% SOC lithium-ion battery modules under different impact loading conditions. Engineering Failure Analysis 82 (2017) 149-160.
[26] Chen Guanhua, Li Wei, Luo Hailing, Xia Yong. Influence of mechanical interaction between lithium-ion pouch cells in a simplified battery module under impact loading. Proceedings of the ASME 2017 International Mechanical Engineering Congress and Exposition IMECE2017, November 3-9, 2017, Tampa, Florida, USA.
[27] Xia Yong, Wierzbicki Tomasz, Sahraei Elham, Zhang Xiaowei. Damage of cells and battery packs due to ground impact. Journal of Power Sources 267 (2014) 78-97.
[28] Zhu Juner, Zhang Xiaowei, Wierzbicki Tomasz, Xia Yong, Chen Guanhua. Structural designs for Electric Vehicle battery pack against ground impact. SAE Technical Paper 2018-01-1438, SAE 2018 World Congress and Exhibition, April 10-12, 2018,Detroit, Michigan, USA.
[29] 混合动力汽车可充电储能装置的后碰防护装置. 中国专利ZL201520801778.2。
[30] Zhang Songan, Zhou Qing, Xia Yong. Influence of mass distribution of battery and occupant on crash response of small lightweight electric vehicle. SAE Technical Paper 2015-01-0575, SAE 2015 World Congress and Exhibition, April 21-23, 2015,Detroit, Michigan, USA, doi: 10.4271/2015-01-0575.
[31] Gu GY, Lin ST, Meng Y, Xia Y, Zhou Q. Influence of Strain Rate and Stress State on the Mechanical Behavior of Die-Casting AM60 Magnesium Alloy. ASME 2011, IMECE2011-65196, Denver, Colorado, USA. November 2011.
[32] Li Wei, Zhu Juner, Xia Yong, Zhou Qing. Testing and modeling the effect of strain-rateon plastic anisotropy for a traditional high strength steel. ASME 2015 International Mechanical Engineering Congress & Exposition,IMECE2015-53270, Houston, Texas, USA.
[33] Zhu Juner, Xia Yong, Luo Hailing, Gu Gongyao, Zhou Qing. Influence of flow rule and calibration approach on plasticity characterization of DP780 steel sheets using Hill48 model. International Journal of Mechanical Sciences 89 (2014) 148–157.
[34] Zhu Juner, Xia Yong, Gu Gongyao and Zhou Qing. Extension of non-associated Hill48 model for characterizing dynamic mechanical behavior of a typical high-strength steel sheet. Proceedings of the ASME 2014 International Mechanical Engineering Congress & Exposition, IMECE2014, November 14-20, 2014, Montreal, Quebec,Canada.
[35] Zhu Juner, Xia Yong, Zhou Qing, Wierzbicki Tomasz. A rate-dependent model for metals based on a master curve of normalized hardening behavior of DP steels. Journal of Dynamic Behavior of Materials 2 (2016) 1-11.
[36] Gu Gongyao, Xia Yong, Lin Chin-hsu, Lin Shaoting, Meng Yan, Zhou Qing. Experimental study on characterizing damage behavior of thermoplastics.Materials and Design 44 (2013) 199-207.
[37] Meng Yan, Xia Yong, Zhou Qing, Lin Shaoting. Identification of true stress-strain curve of thermoplastic polymers under biaxial tension. SAE International Journal of Materials and Manufacturing 9 (2016) 768-775.
[38] Yang Dongyang, Stalin Benoit, Xia Yong, Zhou Qing. Identification of shear properties for woven fiber reinforced polymer simulation. IMECE 2016-66263,Proceedings of the ASME 2016 International Mechanical Engineering Congress and Exposition, November 11-17, 2016, Phoenix, Arizona, USA.
[39] Stalin Benoit, Yang Dongyang, Xia Yong, Zhou Qing. Influence of basic parameters for fiber reinforced polymer crushing simulation. IMECE 2016-66635, Proceedings of the ASME 2016 International Mechanical Engineering Congress and Exposition,November 11-17, 2016, Phoenix, Arizona, USA.
[40] Yang Xin, Xia Yong, Zhou Qing, Wang Pei-Chung, Wang Kathy. Modeling of high strength steel joints bonded with toughened adhesive for vehicle crash simulations.International Journal of Adhesion & Adhesives 39 (2012) 21-32.
[41] Yang Xin, Xia Yong, Zhou Qing. A simplified FE model for pull-out failure of spot welds. Engineering Fracture Mechanics 77 (2010) 1224-1239.
[42] Xia Yong, Zhou Qing, Wang PC, Johnson NL, Gayden XQ, Fickes JD. Development of high efficiency modeling technique for weld-bonded steel joints in vehicle structures, Part I: static experiments and simulations. International Journal of Adhesion and Adhesives 29 (2009) 414-426.
[43] Xia Yong, Zhou Qing, Wang PC, Johnson NL, Gayden XQ, Fickes JD. Development of high efficiency modeling technique for weld-bonded steel joints in vehicle structures, Part II: Dynamic experiments and simulations. International Journal of Adhesion and Adhesives 29 (2009) 427-433.
[44] Zhou Qing, Wu Xueyuan, Xia Yong, Cai Wayne. Spot weld layout optimization of tube crash performance with manufacturing constraints. Journal of Manufacturing Science and Engineering 136 (2014) MANU-12-1343.
[45] Zeng Long, Xia Yong, Zhao He, Zhou Qing. On utilization of material failure criterion in modeling pull-out failure of spot-welded joints. ASME 2013 International Mechanical Engineering Congress & Exposition, San Diego, California, USA.
[46] Xia Yong, Zhu Juner, Wang Kai, Zhou Qing. Design and verification of a strain gauge based load sensor for medium-speed dynamic tests with a hydraulic test machine.International Journal of Impact Engineering 88 (2016) 139-152.
[47] Qin Zihao, Li Wei, Zhu Juner, Xia Yong. Experimental and numerical analysis of the system ringing in intermediate strain rate tests. IMECE 2016-66321, Proceedings of the ASME 2016 International Mechanical Engineering Congress and Exposition, November 11-17, 2016, Phoenix, Arizona, USA.
[48] 一种高速动态试验力测量环节的设计方法. 中国专利ZL201310606117.X.
[49] Qin Zihao, Zhu Juner, Li Wei, Xia Yong, Zhou Qing. System ringing in impact test triggered by upper-and-lower yield points of materials. International Journal of Impact Engineering 108 (2017) 295-302.
最新资讯
-
国内现货!GRAS 46AE/146AE 限时优惠直降 5
2025-04-22 16:22
-
仿真测试必要性及标准法规
2025-04-22 16:22
-
福特退出中国,进入倒计时!
2025-04-22 16:21
-
高效三通道双向电源:释放测试潜能
2025-04-22 09:23
-
R171.01对DCAS的要求⑦
2025-04-22 09:20