电池包液冷板支撑用泡沫硅橡胶疲劳测试分析
泡沫硅橡胶是硅橡胶经过发泡后制成的一种柔性、多孔高分子弹性材料,是将硅橡胶与泡沫材料的特性结合于一体的新型高分子材料。泡沫硅橡胶材料具有良好的热稳定性、耐腐蚀性以及耐高温冲击等性能,能满足很大范围的使用要求。相对于实体硅橡胶材料,泡沫硅橡胶具有其独特的特点,如密度小、比表面积大、能量吸收性好、热导率低、吸声性能好、隔音性佳等,应用领域广泛。现就泡沫硅橡胶在新能源电池包支撑方面的应用详细介绍。
在新能源电池包设计中,液冷板通过导热介质跟电池组紧密接触,传递走多余热量,但是高温的工况和长期的颠簸受力,导热介质厚度会变薄,与液冷板接触变差,使液冷板不能有效传递出电池组的热量。为了使液冷板与导热介质持续紧密接触,用于支撑的泡沫硅橡胶必须提供持久的反弹力,使电池包长期保持良好的工作性能。由于泡沫硅橡胶制品是在承受一定压力和反复形变的情况下使用的,在周期性交变负荷作用下,泡沫硅橡胶制品会因疲劳而性能变差甚至使材料破坏,降低其使用质量,即产生压缩疲劳现象。为了明确泡沫硅橡胶的使用期限,需要对泡沫硅橡胶进行耐疲劳性能方面的测试,表征其产生压缩疲劳的时间及性能变化。
泡沫硅橡胶的耐疲劳性测试称为压缩疲劳试验(compression fatigue test),是研究泡沫橡胶在受到反复压缩应力作用下所引起生热和疲劳破坏的试验。试验时对某一形状试样在规定预应力或预应变条件下,再叠加上周期性应力或应变,随后测定试样的温度升高、应力和形变的变化,或者一直进行到试样破坏所需的时间。疲劳性能试验是目前作为反映软质泡沫材料耐用性最重要的物理性能指标。
二、现状分析
2.1 现有测试标准
对于软质泡沫聚合材料的动态疲劳试验通常是指通过专门的疲劳试验机分别采用恒定形变或恒定负荷的疲劳方式,在低于材料屈服极限的限度以内,使材料经受交变的应力或形变。目前对于动态疲劳试验,国际和国内都制定了相关的测试标准。
国际标准ISO 3385 Flexible cellular polymeric materials -- Determination of fatigue by constant-load pounding试验方法采用的是恒定负荷重复压陷的疲劳试验方法。该标准使用特制的软质泡沫疲劳试验机,用比试样面积小的压头,70±5 Hz的频率,对软泡试样进行反复压陷,达8万次,每次当最大压陷负荷达到限定值(750 N±20 N)时返回。然后对材料进行试验前后力学性能的对比(厚度和硬度的损失),从而了解软质泡沫聚合材料的疲劳性能。该标准的试样是长宽均为380 mm±20 mm,厚度为50 mm±2 mm的长方体,数量为三块。美国材料试验协会标准ASTM D 3574-I3 《软质泡沫材料-块状、粘合及模塑聚氨酯软质泡沫塑料性能试验方法》的测试原理及对试样的要求与ISO 3385一致。
中国轻工业行业标准QBT 2819-2006《软质泡沫材料长期疲劳性能的测定-厚度和硬度损失》的制定就是参考ISO 3385标准制定的,也是恒定负荷重复压陷的疲劳试验方法,测试原理与试样要求同标准ISO 3385一致。对于国标GB/T 1687.3-2016《硫化橡胶 在屈挠试验中温升和耐疲劳性能的测定 第3部分:压缩屈挠试验(恒应变型)》提供了硫化橡胶在恒应变振幅压缩屈挠试验中温升和疲劳性能的测试方法。该标准测定硫化橡胶的疲劳寿命时,由于材料破坏是从内部开始的,看不到,因此该标准的测试方法只是间接的。
目前恒定负荷反复压陷法使用的更广泛,这是因为恒定负荷方法对于软质泡沫聚合材料疲劳性能的评定更为有效。由于恒定负荷反复压陷法能够确保软泡材料所承受的最大负荷(包括当试样由于经受反复压陷逐渐变软后)始终维持在限定范围以内。恒定变形反复压陷法在试样由于经受反复压陷逐渐变软后,相对于试验开始时为达到维持恒定形变(例如厚度的50%),所需要的最大负荷值将会有较大的下降,从而会表现出疲劳试验过程中的前后不均匀性,因而不是很科学。当然恒定变形反复压陷法的疲劳试验机制造起来较为容易,试验过程也较为简单,因此也常用于反映泡沫硅橡胶耐疲劳性。
2.2 测试的影响因素
根据泡沫硅橡胶的压缩反弹力的计算公式

其中,P为抗压强度,即泡沫硅橡胶的压缩反弹力,单位Pa;
F为压力,即接触表面的作用力,单位N;
S为试样的截面积,单位m2。
对同种材料,把相同截面积试样压缩不同高度,所得到的压力不同,因此泡沫材料的压缩反弹力与试样的压缩厚度和截面积有关。对不同材料,压力的大小与材质本身和材料结构有关,材料结构包括相结构、孔结构、相排列组合等。
三、现有产品及对比产品数据分析
泡沫硅橡胶材料在电池包中用于支撑作用时处于压缩状态,同时由于这种材料本身老化速度慢,甚至可以在10年内保证正常使用,若按照2.1中的测试标准,压缩次数太少,无法更好的预测材料的使用周期。
为了反映泡沫硅橡胶的耐疲劳性,收集相同材质、密度相近的泡沫硅橡胶,观察其动态压缩后厚度和压缩反弹力的损失,同时为了加大测试力度,对现有产品做100万(106)次反复压缩试验,试验方式采用恒定形变压缩,压缩量为试样厚度的40 %。
3.1 样品准备
收集试样:密度约为500 kg/m3,东莞市广迈电子科技有限公司生产的GM-500和TZ-500泡沫硅橡胶产品,美国某公司生产的同等密度的XXX泡沫硅橡胶产品
采集试样:厚度约为6 mm,直径为38 mm的圆柱体。
3.2 百万次压缩数据测试及分析
采用厚度测试仪测量试样的具体厚度;采用电子比重计测得试样的密度;采用台式电子显微镜(上海HITACHI, TM3030Plus)观察产品微观形貌。采用电子动静态万能材料试验机(美国INSTRON, E3000),使用动态恒定变形模式,频率为3.5 Hz,记录样品被压缩100万次的载荷变化,并计算得出压缩反弹力变化曲线(见图1)。样品测试完成后恢复24 h,测量并记录其厚度。样品的密度、厚度及反弹力损失数据整理见表1。
从图1和表1可以看出,在百万次压缩过程中,三个产品的厚度损失都很小,几乎为0%,但反弹力损失和载荷损失相差很大;产品GM-500的压缩反弹力在227~210 KPa范围内波动,产品TZ-500的压缩反弹力在251~233 KPa范围内波动,两者的反弹力损失和载荷损失都<8%;产品XXX的反弹力损失和载荷损失>30%。
目前国际上对于不同软质泡沫材料的疲劳试验性能要求没有硬性规定,但综合各类标准,在软泡聚合材料疲劳性能试验中,耐疲劳性反复压陷8万次或10万次后,通常对于厚度损失要求≤5%,而对于40%压陷硬度损失则根据不同的用途要求≤13%~50%。对比表1中百万次反复压缩后厚度和硬度损失数据,产品GM-500和TZ-500的性能远远优于国际标准的要求,而产品XXX的性能在标准要求的范围内。
电池包液冷板支撑用泡沫硅橡胶疲劳测试分析
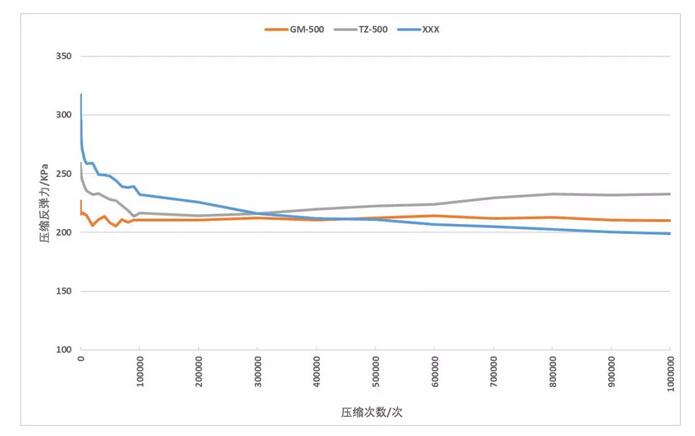
图1 三种产品的百万次压缩曲线
表1 产品测试结果汇总
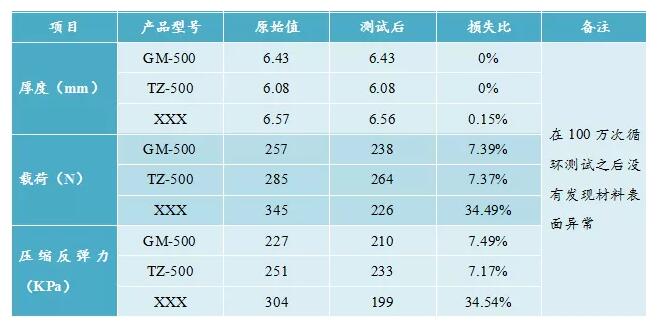
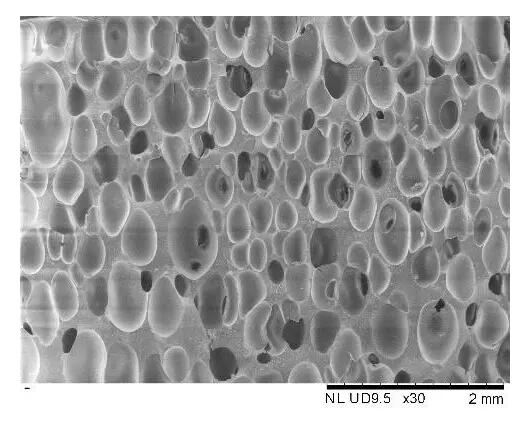
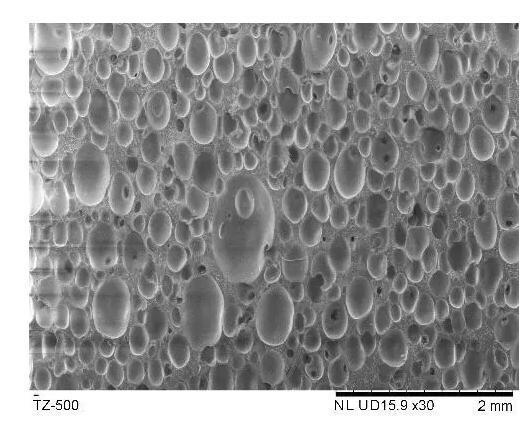
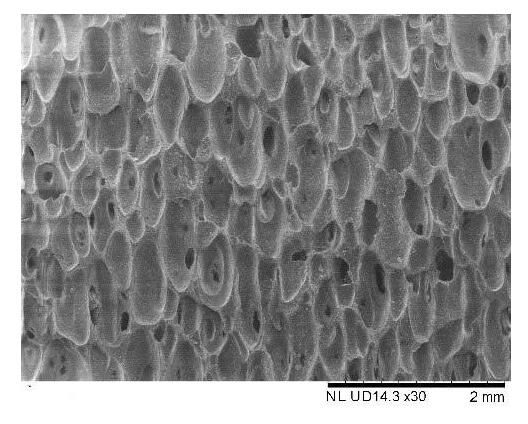
图2 产品GM-500(上)、TZ-500(中)和XXX(下)的显微结构
对于上述产品性能的变化我们可以从图2的微观结构中得到解释。产品GM-500和TZ-500的电镜照片中,大孔与小孔错落有致的排列,孔壁较厚;产品XXX中,大孔数量远多于小孔,孔径分布不均匀,而且孔壁较薄。
3.3、反弹力影响因素分析
不同样品耐疲劳试验压缩反弹力损失的原因主要有两个:① 压缩过程中,闭孔所受外力>孔壁的承受极限,使闭孔被压破;② 随压缩次数的增加,孔壁的结构和性能变差。
对于原因一,由于泡沫材料中并不完全是开孔或闭孔,一般将开孔率>90 %(也有将95 %作为分界点)称为开孔材料。对于开孔材料,泡孔之间相互连通,施加外力时,只需将泡沫材料中的空气挤出;外力消失时,空气又可以进入泡沫材料。对于闭孔材料,在压缩过程中随外界施加压力,闭孔内的空气被压缩,使内部压强增加,若与受力方向垂直的孔壁承受压缩气体的压力(具体作用力示意图见图2)大于孔壁承受的极限,闭孔会被压破;当外力消失时,压缩气体快速扩散使泡孔恢复原状。对于混合孔型泡沫材料,两种受力方式共同存在,其中泡沫材料的孔壁所能承受的外力的极限由材料本身的弹性和厚度决定,对同种材料,孔壁越薄,闭孔易被压破,反弹力损失越大。
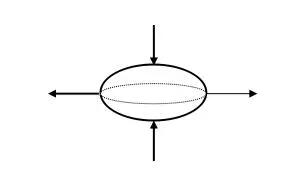
图3 闭孔的受力分析
对于原因二,孔壁的结构和性能与材料本身(包括橡胶的结构、硫化体系、填充剂等)有关,材料本身是由配方和工艺决定的。如玻璃化温度低的橡胶耐疲劳性好,有极性基团的橡胶耐疲劳性差;单硫键的硫化体系,疲劳性最好,而交联剂用量的增加会使硫化胶的疲劳性能下降。
由于泡沫硅橡胶耐老化性好,结合图2和图3的分析可知,三种产品百万次压缩后反弹力的损失差别主要是因为XXX的泡孔结构不均匀,孔壁较薄。
根据上述分析可知,在实际应用中,选择电池包中支撑用泡沫硅橡胶材料时应当选择压缩反弹力损失小的产品即GM-500或TZ-500,否则不能满足长期提供持久的反弹力。
四、结论
通过对密度相当的三款产品GM-500、TZ-500、XXX百万次定形压缩后反弹力的损失研究,可以得出以下结论:
(1) 产品GM-500和TZ-500的百万次压缩反弹力损失分别为7.49%、7.17%,均<8%,这两者产品的厚度损失均为0%,微观形貌中大孔和小孔分布均匀,且孔壁较厚;
(2) 产品XXX的百万次压缩反弹力损失为34.54%,厚度损失均为0.15%,微观形貌中大孔较多,孔壁较薄。
(3) 选择电池包中支撑用泡沫硅橡胶材料时应当选择压缩反弹力损失小的产品即GM-500或TZ-500,否则不能满足长期提供持久的反弹力。
最新资讯
-
大卓智能端到端直播实测,16公里复杂路段挑
2025-04-25 17:16
-
《汽车轮胎耐撞击性能试验方法-车辆法》等
2025-04-25 11:45
-
“真实”而精确的能量流测试:电动汽车能效
2025-04-25 11:44
-
GRAS助力中国高校科研升级
2025-04-25 10:25
-
梅赛德斯-AMG使用VI-CarRealTime开发其控制
2025-04-25 10:21